Workflows
APM Strategy: RCM and FMEA Workflow
The RCM workflow describes the process of determining optimal maintenance and operational strategies based on the probability and consequence of the analyzed failure modes. Reliability Centered Maintenance (RCM) is a process to establish the safe minimum levels of maintenance while ensuring equipment continues to perform to its design function within the current operating context.
The workflow focuses on identifying the potential failures of equipment and locations, describing the possible effect of each failure, and making recommendations for actions that can be taken to prevent the failures from occurring.
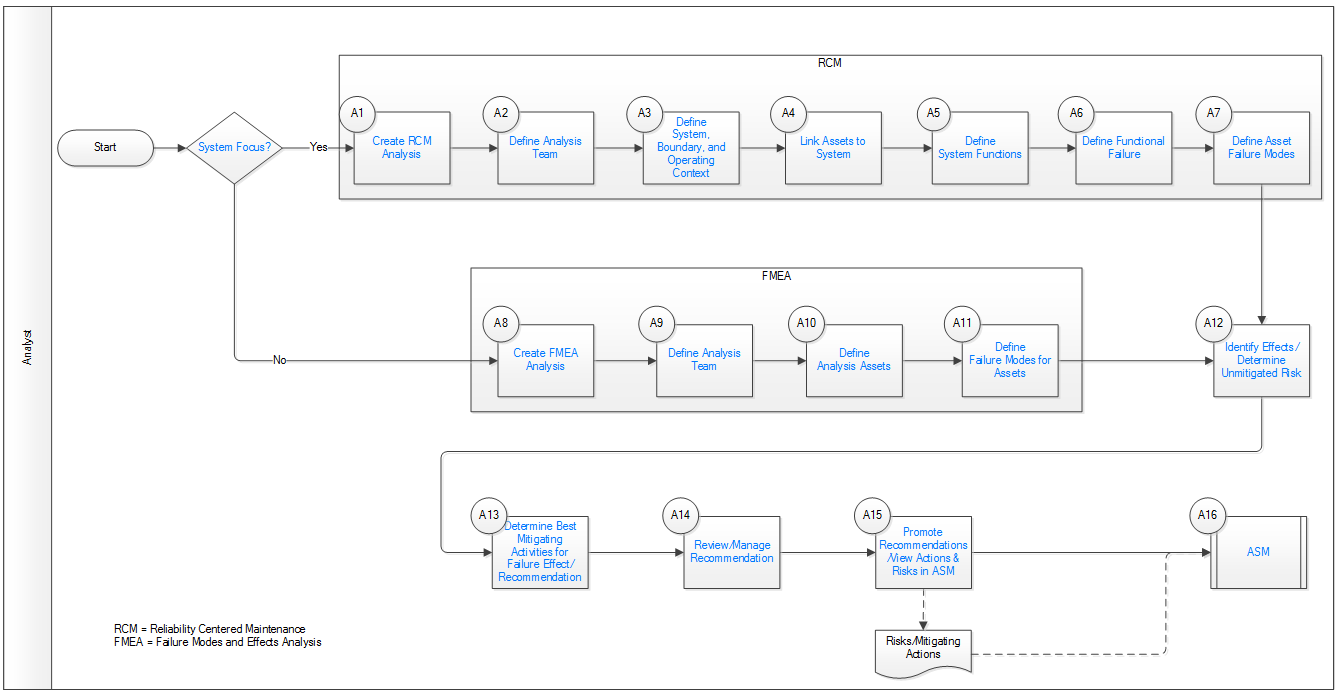
System Focus?
Persona: Analyst
Choose RCM if you need an analysis that is conducted at the system level. Choose FMEA if you need the analysis at the asset level.
Create RCM Analysis
Persona: Analyst
Create the RCM analysis and add details, including some high-level attributes such as analysis start date and a re-evaluation date.
Define Analysis Team
Persona: Analyst
Define at least one analysis team member, and probably more, who are subject matter experts from maintenance, operations, and engineering.
Define System, Boundary, and Operating Context
Persona: Analyst
Create the system in this step at a high level, including common identifier(s) relevant to site terminology. Create a boundary to clearly identify the system and system functions being analyzed. Typically, a drawing or drawings, such as P&ID, are referenced in this step with mark-ups showing boundaries for the analysis. It is useful to understand the operating context of the system. An operating context document is assembled and reviewed with the team. The operating context diagram will include system functional flow description, equipment list, operating parameter ranges, and references.
Link Assets to System
Persona: Analyst
Link the assets that comprise the system being analyzed, including all relevant equipment by tag or ID. This is an important step, because Failure Modes and mitigating Recommendations will be defined with respect to the ID.
Define System Functions
Persona: Analyst
Identify and document system functions as a prerequisite to identifying failures and Failure Modes, and to developing effective maintenance strategies. Primary functions are the basic reasons that the system is acquired and installed. Secondary functions are usually less obvious, but can still have serious failure consequences and need to be understood. Define the function with a meaningful name and identify it with a function type of either Primary or Secondary. Quantify the functional performance in order to properly measure it.
Define Functional Failure
Persona: Analyst
Define the Functional Failure based upon the function statement. Functional Failure is the inability to perform the desired function. The Functional Failure can be a total failure or partial failure.
Define Failure Modes
Persona: Analyst
Define Failure Modes to clearly represent how the failures occur. For every failure, there is a least one Failure Mode, and often, there are multiple. Understanding Failure Modes is critical because maintenance activities are selected to address the modes.
Create FMEA Analysis
Persona: Analyst
Create an FMEA Analysis and add details, including some high-level attributes such as analysis start date and a re-evaluation date. Failure Modes and Effects Analysis (FMEA) focuses on actual equipment and locations. It analyzes how each piece of equipment or location can fail and the effect of each failure.
Define Analysis Assets
Persona: Analyst
Define the assets (equipment or functional locations) that make up the system being analyzed. This will include all relevant equipment by tag or ID. This is an important step, because Failure Modes and mitigating Recommendations will be defined with respect to the ID.
Define Failure Modes for Assets
Persona: Analyst
Define Failure Modes for each asset to clearly represent how the failures occur. For every failure, there is a least one Failure Mode, and often, there are multiple. Understanding Failure Modes is critical because maintenance activities are selected to address the modes.
Identify Effects/Determine Unmitigated Risk
Persona: Analyst
Identify the effects of failure and determine the unmitigated risk in order to understand the effects/consequences of failure and the probability of failure. Run decision logic, if necessary. Failure effects and consequences of failure are closely related and are often used interchangeably. Think of effects as the direct outcome of failure and consequences as the safety (health/environment) or economic outcome. Together, consequence and probability define a criticality (or Risk) associated with failure. When assessing consequences of failure, first identify whether they are hidden or evident. Secondly, assess whether there are Safety, Health, and Environmental consequences. Two items, Stored Energy and Toxic Material, are usually key indicators of potential risk to personnel Safety, Health, and/or the Environment. After identifying failure risks to Safety, Health, and the Environment, all other failure risks are identified using economic terms. This identification is not an either/or process. It is highly likely that Safety, Health, and the Environment Failure Modes will also have an economic consequence.
Determine Best Mitigating Activities for Failure Effect/Recommendation
Persona: Analyst
Decide the mitigating activities for the plan. The Maintenance Strategy is the outcome of the FMEA analysis. It is the plan (activities) to manage an asset. All maintenance actions fall into one of four categories:
- Time- or Cycle-Based (Preventive) maintenance actions
- Condition-Based (Predictive) maintenance actions
- Failure-Finding Tasks (Detective) maintenance actions
- Run-to-failure (Maintenance Inaction)
Review/Manage Recommendation
Persona: Analyst
Review and manage the recommendations that make up asset strategies for each asset in the system. Similar or duplicate recommendations designed to address different Failure Modes can sometimes be consolidated as one activity that requires only one visit (e.g., shutdown) in a given time frame. This clearly reduces the stress on the machine and on the plant operations. For example, the condition-based activity of Vibration Analysis will often be recommended to mitigate the failure modes associated with bearing wear, misalignment, and unbalance. These recommendations may be consolidated into one actionable recommendation to be managed forward, while also maintaining an association to mitigated Failure Modes.
Promote Recommendations/View Actions & Risks in ASM
Persona: Analyst
Promote recommendations so they can be managed as a comprehensive asset strategy. The recommendations will be represented in the asset strategy as actions to be reviewed, approved, and implemented.
Asset Strategy Management (ASM)
Persona: Analyst
RCM and FMEA are APM workflows from which you can promote Risks and Mitigating Actions to ASM to create strategies based on those recommendations.
Go to the ASM Workflow.