TM Data Loaders
About the Thickness Monitoring (TM) Data Loaders
The following Data Loaders are available in Thickness Monitoring:
- Thickness Monitoring (TM) Equipment Data Loader
- Thickness Monitoring (TM) Functional Location Data Loader
Throughout the documentation, these Data Loaders are collectively called the Thickness Monitoring (TM) Data Loaders. You can use them to implement Thickness Monitoring when you have thickness measurement data in a legacy system. To import data using these Data Loaders, APM provides the following Excel templates:
- Thickness Monitoring (TM) Equipment.xlsx
- Thickness Monitoring (TM) Functional Location.xlsx
These templates support baseline Thickness Monitoring in APM. You must export measurement data from your legacy system so that the data can be used to populate the templates. The data from the templates will then be imported into APM using the corresponding Data Loaders.
The data loader workbooks allow you to:
- Create or update Corrosion Analysis Settings (CAS) records for an Asset (i.e., Equipment or Functional Location), TML Group, or TML.
- Create or update TML Group records, and link each of them to an Asset.
- Create or update TML records, and link each of them to an Asset or TML Group.
- Create or update Thickness Measurement records, and link them to a TML.
About the Thickness Monitoring (TM) Data Loaders Requirements
Before you use the data loader workbooks, you must complete the following steps:
- Ensure that the Thickness Monitoring module is deployed.
- Ensure that the following licenses are active:
- APM Connect Plus
- Thickness Monitoring
-
Ensure that the following data is present:
- Site Reference
- Equipment Taxonomy
- Equipment and Functional Location Families
- Units of Measure Conversion Sets
-
Stress Tables (APM provides Stress Tables for Piping, Pressure Vessels, and Tanks. If you want to use values from these Stress Tables with the data loader workbook, you must ensure that the records are imported into your database prior to performing the data load).
- Ensure that you have set up appropriate relationships and key fields. To do so, you must login as a member of the MI Thickness Monitoring Administrator Security Group.
-
Create a relationship between TML Groups and Assets. To do so, configure family preferences, specifying the following values:
- Asset-to-Subcomponent Relationship: Has TML Group
- Subcomponent-to-Asset Relationship: Has TML Group
- Component ID Field: TML Group ID
Note: By default, the relationship is created between Equipment and TML Groups. If you want to use the Thickness Monitoring (TM) Functional Location Data Loader, in the drop-down list box at the top of the workspace, select Functional Location. -
The Security User loading the data must be associated with either the MI Data Loader User or MI Data Loader Admin Security Role, and must also be associated with the MI Thickness Monitoring Administrator or the MI Thickness Monitoring Inspector Security Group or a Security Role that is associated with at least one of these Security Groups.
- The data loader workbooks contain sample data in each column. It is only for your reference. You must remove this data before using the data loader workbooks.
About the Thickness Monitoring (TM) Data Loaders Data Model
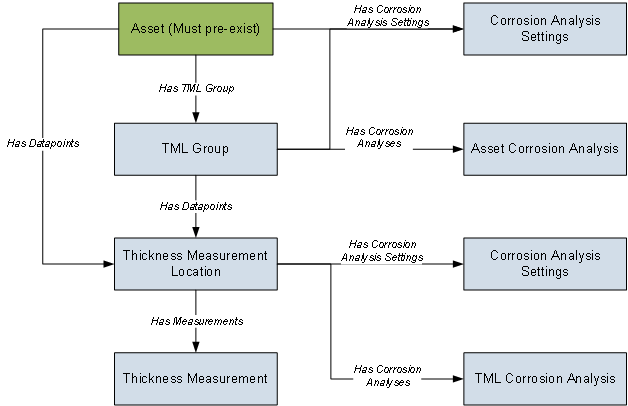
About the Thickness Monitoring (TM) Data Loaders General Loading Strategy
This topic describes the best practices to loading the data and the order in which the data will be loaded.
Best Practices
- For Oracle databases, valid cell values are case-sensitive.
- The imported data must load in a specific sequence in order to successfully populate fields, to create records, and to link them to the predecessor and successor records.
- If a data loader worksheet contains any blank cells:
- When you create new records, the fields corresponding to the blank cells are updated with the default values, if any.
- When you update existing records, the fields corresponding to the blank cells are not updated.
- The Thickness Monitoring (TM) Data Loaders map the datasheet columns in the data loader workbooks to fields in APM families by their position. Therefore, you must not change the column positions and IDs. You can, however, change the captions if needed.
- ID fields must not include special characters or spaces.
- Columns (including columns representing custom fields) in the worksheets should be formatted as Text.
- You must consider the rules described in the Workbook Layout and Use section of this document while using the data loader workbooks.
- Details related to an Equipment that is linked to a TML Group or a TML must always be entered on the assets and Asset_CAS worksheets of the Thickness Monitoring (TM) Equipment Data Loader even if the asset has already been loaded earlier. Similarly, details related to a Functional Location that is linked to a TML Group or a TML must always be entered on the Functional_Location and Functional_Location_CAS worksheets of the Thickness Monitoring (TM) Functional Location Data Loader even if the Functional Location has already been loaded earlier.
- When you override the values for Minimum Thickness and Minimum Thickness Type fields, the values from the data loader will be considered.
-
In addition to the fields included in the data loader workbooks, if you want to add values for more fields for a record, you can add columns for those fields on the appropriate worksheet.
Note: The fields that you want to add to the data loader workbooks must already exist in the corresponding family. If not, you must add the fields to the family via Configuration Manager. - Do not delete a worksheet in the data loader workbooks.
Load Sequence
The data must be loaded in the following sequence to successfully populate fields, create records, and link them to the predecessor and successor records:
- The Assets or the Functional_Location worksheet is processed.
If you are using the Thickness Monitoring (TM) Equipment Data Loader, it searches for the Equipment that corresponds to the Equipment ID, CMMS System, and Equipment Technical Number information that you provide on the Assets worksheet. If you are using the Thickness Monitoring (TM) Functional Location Data Loader, it searches for the Functional Location that corresponds to the Functional Location ID and CMMS System information that you provide on the Functional_Location worksheet.
If an asset specified on the worksheet does not exist, it will not be loaded. In addition, the TML Groups and TMLs linked to the asset are not loaded.
- The Asset_CAS or the Functional_Location_CAS worksheet is processed.
If you have entered values in all the mandatory cells and if the details of an asset on this worksheet match the details on the Assets or the Functional_Location worksheet:
- A Corrosion Analysis Settings record is created and linked to the asset using the Has Corrosion Analysis Settings relationship.
- An Asset Corrosion Analysis record is created and linked to the asset using the Has Corrosion Analyses relationship.
If you do not enter values (in cells other than the mandatory ones) on this worksheet, the default values are used.
- The TML_Group worksheet is processed. For each TML Group, if the details of the asset on the TML_Group worksheet match the details on the assets or the Functional_Location worksheet, a TML Group record is created and linked to the asset using the Has TML Group relationship.
- The TML_Group_CAS worksheet is processed. For each TML Group:
- A Corrosion Analysis Settings record is created, and linked to the TML Group using the Has Corrosion Analysis Settings relationship. The fields in the Corrosion Analysis Settings record are populated with the corresponding values on the Asset_CAS or the Functional_Location_CAS worksheet.
- If you have entered values on the TML_Group_CAS worksheet, the values in the fields in the Corrosion Analysis Settings record linked to the TML Group are replaced with the values on the TML_Group_CAS worksheet.
- An Asset Corrosion Analysis record is created, and linked to the TML Group using the Has Corrosion Analyses relationship.
- The TML worksheet is processed.
- If you have entered a value in the TML Group ID column on this worksheet, a Thickness Measurement Location is created and linked to the TML Group using the Has DataPoints relationship. Otherwise, the TML is linked to the asset that you have specified on this worksheet.
- The TML_CAS worksheet is processed. For each TML:
- A Corrosion Analysis Settings record is created, and linked to the TML using the Has Corrosion Analysis Settings relationship. The fields in the Corrosion Analysis Settings record are populated with the corresponding values on the TML_Group_CAS, Asset_CAS, or Functional_Location_CAS worksheet, depending on whether the TML is linked to a TML Group, Equipment, or Functional Location respectively.
- A TML Corrosion Analysis record is created, and linked to the TML using the Has Corrosion Analyses relationship.
- If you have entered values on this worksheet, the values in the fields in the Corrosion Analysis Settings record linked to the TML are replaced with the values on the TML_CAS worksheet.
- The Measurements worksheet is processed. For each row on this worksheet, a Thickness Measurement record is created (or updated), and linked to the TML using the Has Measurements relationship.Note: For a given TML, if two or more rows contain the same value in the Measurement Date field, then only one Measurement record is created. The fields in that record are populated with values in the last row among them.
After you load the data, the updated assets appear in the Assets and Assets Requiring a Calculation sections on the Thickness Monitoring Overview page. You must calculate all the analyses that you have loaded because they are not calculated automatically after you load the data.
- Asset Level Data
- TML Groups in 100-count batches
- Thickness Measurement Locations in 100-count batches
- Measurements in 250-count batches
If an error occurs while loading data, you can reduce the transaction scopes as per your requirement. For information on modifying the transaction scopes, refer to the Configure Data Loader Transaction Scopes topic.
About the Thickness Monitoring (TM) Data Loaders Workbook Layout and Use
Color Coding
Certain columns on the worksheets have different functions and requirements. To illustrate this, certain columns are color-coded. The following table lists the colors and what they represent.
Color |
Description |
Comments |
Grey |
Lookup Fields |
Indicates columns that contain values that are used by the Thickness Monitoring Data Loader to look up and create records. If these columns are removed from the worksheets, the data load will fail. While the worksheets require that these columns be present, values are not necessarily required in these columns. |
Red |
Fields Required for Calculation |
Indicates columns that contain values that are required to perform calculations in Risk Based Inspection. Some cells only require values in certain cases. Such cases are found in parentheses in the first row of each worksheet. |
Blue |
Recommended Fields |
Indicates columns that, according to APM Best Practice for Risk Based Inspection, should contain values. |
Green |
Custom Fields |
Indicates columns where you can specify custom fields. |
Limitations
The Thickness Monitoring (TM) Data Loaders have the following limitations:
- If you modify the format of the values in columns on any of the worksheets, you will not be able to import data.
- You cannot create or update nominal measurements using the data loader workbooks. You can only create or update actual measurements.
- The values that you enter in the data loader workbooks are case-sensitive.
- You cannot link an RBI Component to a TML Group using the data loader workbooks.
- You cannot relocate, renew, or organize TMLs using the data loader workbooks.
- You cannot skip measurements using the data loader workbooks.
-
If you reimport data, the records that have been created by the Thickness Monitoring (TM) Data Loaders will be updated. Therefore, while reimporting data related to a record, if you remove the data for a field in the data loader workbooks, the value for the corresponding field in APM will be either a default value or blank.
Tip: If you do not want to update a field value, you can remove the corresponding column from the data loader workbooks. You cannot, however, remove columns that correspond to required fields.
Assets Worksheet
Field Caption |
Field ID |
Data Type (Length) |
Comments |
---|---|---|---|
Equipment ID |
MI_EQUIP000_EQUIP_ID_C |
Character (255) |
This column requires at least one cell to have a value. To upload Functional Location data in the same worksheet, specify the Functional Location ID in this column. |
CMMS System |
MI_EQUIP000_SAP_SYSTEM_C |
Character (255) |
If the Equipment record for an asset has a value in the CMMS System field, enter that value in this column. To upload Functional Location data in the same worksheet, specify the CMMS System for the Functional Location value in this column. |
Equipment Technical Number |
MI_EQUIP000_EQUIP_TECH_NBR_C |
Character (255) |
If you are required to enter a value for the CMMS System cell for a piece of equipment, and the Equipment record has a value in the Equipment Technical Number field, enter that value in this column. If there is no value in the CMMS System field, this column can be blank, even if the Equipment record contains a value for the Equipment Technical Number field. |
Asset Family ID | ASSET_FAMILY_ID | Character (255) | If you are uploading Functional Location data in the Assets worksheet, specify the MI_FNCLOC00 value in this column. If the column is not present or data is null in this field, APM will consider it as Equipment data. |
Functional_Location Worksheet
On the Functional_Location worksheet, you will specify Functional Locations to which you want to link Thickness Measurement Locations (TMLs) and TML Groups. This worksheet is included only in the Thickness Monitoring (TM) Functional Location Data Loader. The columns that appear on this worksheet also appear on every subsequent worksheet in the Thickness Monitoring (TM) Functional Location Data Loader. They are used to identify the records that will be linked, directly or indirectly, to the Functional Locations. The combination of values in the two columns on this worksheet must be unique.
Field Caption |
Field ID |
Data Type (Length) |
Comments |
---|---|---|---|
Functional Location ID |
MI_FNCLOC00_FNC_LOC_C |
Character (255) |
This column requires at least one cell to have a value. |
CMMS System |
MI_FNCLOC00_SAP_SYSTEM_C |
Character (255) |
If the Functional Location record for an asset has a value in the CMMS System field, enter that value in this column. |
Asset_CAS Worksheet
On the Asset_CAS worksheet, you will specify Corrosion Analysis Settings records for an Equipment. If you do not enter values on this worksheet, the default values are used. This worksheet is included only in the Thickness Monitoring (TM) Equipment Data Loader.
In addition, the values that you enter on this worksheet are used to specify Corrosion Analysis Settings for associated TML Groups and TMLs. You can, however, overwrite these values by specifying different values on the TML_Group_CAS and TML_CAS worksheets respectively.
Field Caption |
Field ID |
Data Type (Length) |
Comments | ||||||||
---|---|---|---|---|---|---|---|---|---|---|---|
Equipment ID |
MI_EQUIP000_EQUIP_ID_C |
Character (255) |
This column requires at least one cell to have a value. To upload Functional Location data in the same worksheet, specify the Functional Location ID in this column. | ||||||||
CMMS System |
MI_EQUIP000_SAP_SYSTEM_C |
Character (255) |
If the Equipment record for an asset has a value in the CMMS System field, enter that value in this column. To upload Functional Location data in the same worksheet, specify the CMMS System for the Functional Location value in this column. | ||||||||
Equipment Technical Number |
MI_EQUIP000_EQUIP_TECH_NBR_C |
Character (255) |
If you are required to enter a value for the CMMS System cell for an asset, and the Equipment record for the asset has a value in the Equipment Technical Number field, enter that value in this column. If there is no value in the CMMS System field, this column can be blank, even if the Equipment record contains a value for the Equipment Technical Number field. | ||||||||
Inspection Type | MI_CA_SET_ANALY_TYPE_CHR | Character (50) |
If you do not enter a value in this cell, then data in this row is not loaded. In the baseline APM system, this cell may only contain one of the following System Code IDs:
The list in this field is populated by the CITP System Code Table. If the system code table has been customized, the valid values could be different. To verify which options are acceptable in your APM system, via Configuration Manager, refer to the appropriate table. | ||||||||
Controlling Corrosion Rate | MI_CA_SET_CR_ROLL_OPT_CHR | Character (50) |
This cell may only contain one of the following values:
The default value is Maximum. | ||||||||
Comments | MI_CA_SET_COM_CON_COR_RAT_CHR | Character (2500) | None | ||||||||
Apply CCR to TML Rem Life Next Insp Date Calc | MI_CA_SET_APPLY_CR_FLG | Boolean | Enter True or False. The default value is False. | ||||||||
Safety Factor | MI_CA_SET_AVG_CR_SFTY_FCTR_NBR | Numeric | The default value is 1. | ||||||||
Minimum Number of TMLs | MI_CA_SET_AVG_CR_MN_TML_NBR | Numeric | The default value is 1. | ||||||||
Percentile | MI_CA_SET_AVG_CR_PERC_NBR | Numeric |
The default value is 100. | ||||||||
Std Deviation Factor | MI_CA_SET_STD_DEV_FCTR_NBR | Numeric | The default value is 2. | ||||||||
Remaining Life Critical Number of TMLs | MI_CA_SET_RM_LIF_CRIT_TMLS_NBR | Numeric | The default value is 1. Enter a value between 0 and 1. | ||||||||
Corrosion Rate Options - Least Squares | MI_CA_SET_CR_OPT_LS_FLG | Boolean | Enter True or False. The default value is False. | ||||||||
Corrosion Rate Options - Short Term | MI_CA_SET_CR_OPT_ST_FLG | Boolean | Enter True or False. The default value is True. | ||||||||
Corrosion Rate Options - Long Term | MI_CA_SET_CR_OPT_LT_FLG | Boolean | Enter True or False. The default value is True. | ||||||||
Corrosion Rate Options - Custom A | MI_CA_SET_CR_OPT_A_F | Boolean | Enter True or False. The default value is False. | ||||||||
Corrosion Rate Options - Custom B | MI_CA_SET_CR_OPT_B_F | Boolean | Enter True or False. The default value is False. | ||||||||
Default Inspection Interval (Months) | MI_CA_SET_INSP_INTRVL_NBR | Numeric | The default value is 0. | ||||||||
Inspection Interval Options - Factor Remaining Life | MI_CA_SET_INSP_INT_OPT_FRL_FLG | Boolean | Enter True or False. The default value is True. | ||||||||
Inspection Interval Options - Inspection Interval | MI_CA_SET_INSP_INT_OPT_II_FLG | Boolean | Enter True or False. The default value is True. | ||||||||
Default T-Min (Inches) | MI_CA_SET_REF_TMIN_NBR | Numeric | The default value is 0. | ||||||||
Minimum Corrosion Rate (Mils/year) | MI_CA_SET_MN_CR_NBR | Numeric | The default value is 5. | ||||||||
Use Minimum Corrosion Rate | MI_CA_SET_USE_MN_CR_FLG | Boolean | Enter True or False. The default value is False. | ||||||||
Remaining Life Factor | MI_CA_SET_REM_LIFE_FCTR_NBR | Numeric | The default value is 0.5. Enter a number between 0 and 1. | ||||||||
Allowable Measurement Variance (inches) | MI_CA_SET_ALLOW_VARIA_NBR | Numeric | The default value is 0. | ||||||||
Corrosion Rate Variance | MI_CA_SET_CRV_N | Numeric | The default value is 0. |
Functional_Location_CAS Worksheet
On the Functional_Location_CAS worksheet, you will specify Corrosion Analysis Settings records for a Functional Location. If you do not enter values on this worksheet, the default values are used. This worksheet is included only in the Thickness Monitoring (TM) Functional Location Data Loader.
In addition, the values that you enter on this worksheet are used to specify Corrosion Analysis Settings for associated TML Groups and TMLs. You can, however, overwrite these values by specifying different values on the TML_Group_CAS and TML_CAS worksheets respectively.
Field Caption |
Field ID |
Data Type (Length) |
Comments | ||||||||
---|---|---|---|---|---|---|---|---|---|---|---|
Functional Location ID |
MI_FNCLOC00_FNC_LOC_C |
Character (255) |
This column requires at least one cell to have a value. | ||||||||
CMMS System |
MI_FNCLOC00_SAP_SYSTEM_C |
Character (255) |
If the Functional Location record for an asset has a value in the CMMS System field, enter that value in this column. | ||||||||
Inspection Type | MI_CA_SET_ANALY_TYPE_CHR | Character (50) |
If you do not enter a value in this cell, then data in this row is not loaded. In the baseline APM system, this cell may only contain one of the following System Code IDs:
The list in this field is populated by the CITP System Code Table. If the system code table has been customized, the valid values could be different. To verify which options are acceptable in your APM system, via Configuration Manager, refer to the appropriate table. | ||||||||
Controlling Corrosion Rate | MI_CA_SET_CR_ROLL_OPT_CHR | Character (50) |
This cell may only contain one of the following values:
The default value is Maximum. | ||||||||
Comments | MI_CA_SET_COM_CON_COR_RAT_CHR | Character (2500) | None | ||||||||
Apply CCR to TML Rem Life Next Insp Date Calc | MI_CA_SET_APPLY_CR_FLG | Boolean | Enter True or False. The default value is False. | ||||||||
Safety Factor | MI_CA_SET_AVG_CR_SFTY_FCTR_NBR | Numeric | The default value is 1. | ||||||||
Minimum Number of TMLs | MI_CA_SET_AVG_CR_MN_TML_NBR | Numeric | The default value is 1. | ||||||||
Percentile | MI_CA_SET_AVG_CR_PERC_NBR | Numeric |
The default value is 100. | ||||||||
Std Deviation Factor | MI_CA_SET_STD_DEV_FCTR_NBR | Numeric | The default value is 2. | ||||||||
Remaining Life Critical Number of TMLs | MI_CA_SET_RM_LIF_CRIT_TMLS_NBR | Numeric | The default value is 1. | ||||||||
Corrosion Rate Options - Least Squares | MI_CA_SET_CR_OPT_LS_FLG | Boolean | Enter True or False. The default value is False. | ||||||||
Corrosion Rate Options - Short Term | MI_CA_SET_CR_OPT_ST_FLG | Boolean | Enter True or False. The default value is True. | ||||||||
Corrosion Rate Options - Long Term | MI_CA_SET_CR_OPT_LT_FLG | Boolean | Enter True or False. The default value is True. | ||||||||
Corrosion Rate Options - Custom A | MI_CA_SET_CR_OPT_A_F | Boolean | Enter True or False. The default value is False. | ||||||||
Corrosion Rate Options - Custom B | MI_CA_SET_CR_OPT_B_F | Boolean | Enter True or False. The default value is False. | ||||||||
Default Inspection Interval (Months) | MI_CA_SET_INSP_INTRVL_NBR | Numeric | The default value is 0. | ||||||||
Inspection Interval Options - Factor Remaining Life | MI_CA_SET_INSP_INT_OPT_FRL_FLG | Boolean | Enter True or False. The default value is True. | ||||||||
Inspection Interval Options - Inspection Interval | MI_CA_SET_INSP_INT_OPT_II_FLG | Boolean | Enter True or False. The default value is True. | ||||||||
Default T-Min (Inches) | MI_CA_SET_REF_TMIN_NBR | Numeric | The default value is 0. | ||||||||
Minimum Corrosion Rate (Mils/year) | MI_CA_SET_MN_CR_NBR | Numeric | The default value is 5. | ||||||||
Use Minimum Corrosion Rate | MI_CA_SET_USE_MN_CR_FLG | Boolean | Enter True or False. The default value is False. | ||||||||
Remaining Life Factor | MI_CA_SET_REM_LIFE_FCTR_NBR | Numeric | The default value is 0.5. Enter a number between 0 and 1. | ||||||||
Allowable Measurement Variance (inches) | MI_CA_SET_ALLOW_VARIA_NBR | Numeric | The default value is 0. | ||||||||
Corrosion Rate Variance | MI_CA_SET_CRV_N | Numeric | The default value is 0. |
TML_Group Worksheet
On the TML_Group worksheet, you will specify the TML groups (which are or will be represented by TML Group records) that you want to create or update.
Field Caption |
Field ID |
Data Type (Length) |
Comments |
---|---|---|---|
Equipment ID |
MI_EQUIP000_EQUIP_ID_C |
Character (255) |
This column requires at least one cell to have a value. This column appears only in the Thickness Monitoring (TM) Equipment Data Loader. To upload Functional Location data in the same worksheet, specify the Functional Location ID in this column. |
Functional Location ID |
MI_FNCLOC00_FNC_LOC_C |
Character (255) |
This column requires at least one cell to have a value. This column appears only in the Thickness Monitoring (TM) Functional Location Data Loader. |
CMMS System |
MI_EQUIP000_SAP_SYSTEM_C |
Character (255) |
If the Equipment or the Functional Location record for an asset has a value in the CMMS System field, enter that value in this column. To upload Functional Location data in the same worksheet, specify the CMMS System for the Functional Location value in this column. |
Equipment Technical Number |
MI_EQUIP000_EQUIP_TECH_NBR_C |
Character (255) |
This column appears only in the Thickness Monitoring (TM) Equipment Data Loader. If you are required to enter a value for the CMMS System cell for an asset, and the Equipment record for the asset has a value in the Equipment Technical Number field, enter that value in this column. If there is no value in the CMMS System field, this column can be blank, even if the Equipment record contains a value for the Equipment Technical Number field. |
TML Group ID |
MI_TMLGROUP_ID_C |
Character (50) |
A value is required and must be unique among all the TML Groups linked to an Asset. Note: Although the TML Group ID field is disabled and populated automatically in APM, you can override the value using the data loader workbook.
|
Description | MI_TMLGROUP_DESCR_C | Character (255) | None |
Corrosion Group | MI_TMLGROUP_CORRO_GROUP_C | Character (255) | None |
Comments | MI_TMLGROUP_COMME_T | Character (2500) | None |
TML_Group_CAS
On the TML_Group_CAS worksheet, you will specify Corrosion Analysis Settings records for a TML Group. If you do not enter values on this worksheet, the values on the Asset_CAS or Functional_Location_CAS worksheet for the associated asset are used. Otherwise, the values that you enter on the TML_Group_CAS are used for the TML Group.
Field Caption |
Field ID |
Data Type (Length) |
Comments |
---|---|---|---|
Equipment ID |
MI_EQUIP000_EQUIP_ID_C |
Character (255) |
This column requires at least one cell to have a value. This column appears only in the Thickness Monitoring (TM) Equipment Data Loader. To upload Functional Location data in the same worksheet, specify the Functional Location ID in this column. |
Functional Location ID |
MI_FNCLOC00_FNC_LOC_C |
Character (255) |
This column requires at least one cell to have a value. This column appears only in the Thickness Monitoring (TM) Functional Location Data Loader. |
CMMS System |
MI_EQUIP000_SAP_SYSTEM_C |
Character (255) |
If the Equipment or the Functional Location record for an asset has a value in the CMMS System field, enter that value in this column. To upload Functional Location data in the same worksheet, specify the CMMS System for the Functional Location value in this column. |
Equipment Technical Number |
MI_EQUIP000_EQUIP_TECH_NBR_C |
Character (255) |
This column appears only in the Thickness Monitoring (TM) Equipment Data Loader. If you are required to enter a value for the CMMS System cell for an asset, and the Equipment record for the asset has a value in the Equipment Technical Number field, enter that value in this column. If there is no value in the CMMS System field, this column can be blank, even if the Equipment record contains a value for the Equipment Technical Number field. |
Inspection Type | MI_CA_SET_ANALY_TYPE_CHR | Character (50) | If you do not enter a value in this cell, then data in this row is not loaded. This cell may only contain a value that you entered in the Inspection Type cell for the associated asset on the Asset_CAS or Functional_Location_CAS worksheet. |
TML Group ID |
MI_TMLGROUP_ID_C |
Character (50) |
A value is required and must match one of the value in the corresponding cell on the TML Group worksheet. |
Controlling Corrosion Rate | MI_CA_SET_CR_ROLL_OPT_CHR | Character (50) |
This cell may only contain one of the following values:
|
Comments |
MI_CA_SET_COM_CON_COR_RAT_CHR |
Character (2000) | None |
Apply CCR to TML Rem Life Next Insp Date Calc | MI_CA_SET_APPLY_CR_FLG | Boolean |
Enter True or False. If you do not enter a value in this cell, the value in the corresponding cell on the Asset_CAS or the Functional_Location_CAS worksheet is used. |
Safety Factor | MI_CA_SET_AVG_CR_SFTY_FCTR_NBR | Numeric |
If you do not enter a value in this cell, the value in the corresponding cell on the Asset_CAS or the Functional_Location_CAS worksheet is used. |
Minimum Number of TMLs | MI_CA_SET_AVG_CR_MN_TML_NBR | Numeric |
If you do not enter a value in this cell, the value in the corresponding cell on the Asset_CAS or the Functional_Location_CAS worksheet is used. |
Percentile | MI_CA_SET_AVG_CR_PERC_NBR | Numeric |
If you do not enter a value in this cell, the value in the corresponding cell on the Asset_CAS or the Functional_Location_CAS worksheet is used. |
Std Deviation Factor | MI_CA_SET_STD_DEV_FCTR_NBR | Numeric |
If you do not enter a value in this cell, the value in the corresponding cell on the Asset_CAS or the Functional_Location_CAS worksheet is used. |
Remaining Life Critical Number of TMLs | MI_CA_SET_RM_LIF_CRIT_TMLS_NBR | Numeric |
If you do not enter a value in this cell, the value in the corresponding cell on the Asset_CAS or the Functional_Location_CAS worksheet is used. |
Corrosion Rate Options - Least Squares | MI_CA_SET_CR_OPT_LS_FLG | Boolean |
Enter True or False. If you do not enter a value in this cell, the value in the corresponding cell on the Asset_CAS or the Functional_Location_CAS worksheet is used. |
Corrosion Rate Options - Short Term | MI_CA_SET_CR_OPT_ST_FLG | Boolean |
Enter True or False. If you do not enter a value in this cell, the value in the corresponding cell on the Asset_CAS or the Functional_Location_CAS worksheet is used. |
Corrosion Rate Options - Long Term | MI_CA_SET_CR_OPT_LT_FLG | Boolean |
Enter True or False. If you do not enter a value in this cell, the value in the corresponding cell on the Asset_CAS or the Functional_Location_CAS worksheet is used. |
Corrosion Rate Options - Custom A | MI_CA_SET_CR_OPT_A_F | Boolean |
Enter True or False. If you do not enter a value in this cell, the value in the corresponding cell on the Asset_CAS or the Functional_Location_CAS worksheet is used. |
Corrosion Rate Options - Custom B | MI_CA_SET_CR_OPT_B_F | Boolean |
Enter True or False. If you do not enter a value in this cell, the value in the corresponding cell on the Asset_CAS or the Functional_Location_CAS worksheet is used. |
Default Inspection Interval (Months) | MI_CA_SET_INSP_INTRVL_NBR | Numeric |
If you do not enter a value in this cell, the value in the corresponding cell on the Asset_CAS or the Functional_Location_CAS worksheet is used. |
Inspection Interval Options - Factor Remaining Life | MI_CA_SET_INSP_INT_OPT_FRL_FLG | Boolean |
Enter True or False. If you do not enter a value in this cell, the value in the corresponding cell on the Asset_CAS or the Functional_Location_CAS worksheet is used. |
Inspection Interval Options - Inspection Interval | MI_CA_SET_INSP_INT_OPT_II_FLG | Boolean |
Enter True or False. If you do not enter a value in this cell, the value in the corresponding cell on the Asset_CAS or the Functional_Location_CAS worksheet is used. |
Default T-Min (Inches) | MI_CA_SET_REF_TMIN_NBR | Numeric |
If you do not enter a value in this cell, the value in the corresponding cell on the Asset_CAS or the Functional_Location_CAS worksheet is used. |
Minimum Corrosion Rate (Mils/year) | MI_CA_SET_MN_CR_NBR | Numeric |
If you do not enter a value in this cell, the value in the corresponding cell on the Asset_CAS or the Functional_Location_CAS worksheet is used. |
Use Minimum Corrosion Rate | MI_CA_SET_USE_MN_CR_FLG | Boolean |
Enter True or False. If you do not enter a value in this cell, the value in the corresponding cell on the Asset_CAS or the Functional_Location_CAS worksheet is used. |
Remaining Life Factor | MI_CA_SET_REM_LIFE_FCTR_NBR | Numeric |
Enter a number between 0 and 1. If you do not enter a value in this cell, the value in the corresponding cell on the Asset_CAS or the Functional_Location_CAS worksheet is used. |
Allowable Measurement Variance (inches) | MI_CA_SET_ALLOW_VARIA_NBR | Numeric |
If you do not enter a value in this cell, the value in the corresponding cell on the Asset_CAS or the Functional_Location_CAS worksheet is used. |
Corrosion Rate Variance | MI_CA_SET_CRV_N | Numeric |
If you do not enter a value in this cell, the value in the corresponding cell on the Asset_CAS or the Functional_Location_CAS worksheet is used. |
TML Worksheet
On the TML worksheet, you will specify the TMLs (that are or will be represented by Thickness Measurement Location records) that you want to create. For some of the cells, if you do not enter a value on this worksheet, after you load data, the corresponding fields are populated automatically in APM.
Field Caption | Field ID | Data Type (Length) | Comments | ||||||||||||||||||||
---|---|---|---|---|---|---|---|---|---|---|---|---|---|---|---|---|---|---|---|---|---|---|---|
Equipment ID |
MI_EQUIP000_EQUIP_ID_C |
Character (255) |
This column requires at least one cell to have a value. This column appears only in the Thickness Monitoring (TM) Equipment Data Loader. To upload Functional Location data in the same worksheet, specify the Functional Location ID in this column. | ||||||||||||||||||||
Functional Location ID |
MI_FNCLOC00_FNC_LOC_C |
Character (255) |
This column requires at least one cell to have a value. This column appears only in the Thickness Monitoring (TM) Functional Location Data Loader. | ||||||||||||||||||||
CMMS System |
MI_EQUIP000_SAP_SYSTEM_C |
Character (255) |
If the Equipment or the Functional Location record for an asset has a value in the CMMS System field, enter that value in this column. To upload Functional Location data in the same worksheet, specify the CMMS System for the Functional Location value in this column. | ||||||||||||||||||||
Equipment Technical Number |
MI_EQUIP000_EQUIP_TECH_NBR_C |
Character (255) |
This column appears only in the Thickness Monitoring (TM) Equipment Data Loader. If you are required to enter a value for the CMMS System cell for an asset, and the Equipment record for the asset has a value in the Equipment Technical Number field, enter that value in this column. If there is no value in the CMMS System field, this column can be blank, even if the Equipment record contains a value for the Equipment Technical Number field. | ||||||||||||||||||||
TML Group ID | MI_TMLGROUP_ID_C |
Character (50) | If you do not enter a value in this cell, the TML is directly linked to the Asset. | ||||||||||||||||||||
TML ID |
MI_DP_ID_CHR |
Character (50) |
A value is required, and must be unique among all the TMLs linked to a TML Group or an Asset. | ||||||||||||||||||||
TML Analysis Type |
MI_TML_TYPE_CHR |
Character (50) | A value is required. This cell may only contain one of the values that you entered in the Inspection Type cell in the Asset_CAS, Functional_Location_CAS, or TML_Group_CAS worksheet, whichever is linked to the TML. | ||||||||||||||||||||
Component Type |
MI_TML_COMP_TYPE_CHR |
Character (10) |
In the baseline APM system, this cell may only contain one of the following System Code IDs:
| ||||||||||||||||||||
Location | MI_DP_LOCTN_CHR | Character (50) | None | ||||||||||||||||||||
ISO Drawing Number | MI_DP_ISO_DRAW_CHR | Character (50) | None | ||||||||||||||||||||
Access |
MI_DP_ACCESS_CHR |
Character (50) |
In the baseline APM system, this cell may only contain one of the following System Code IDs:
The list in this field is populated by the DPAC System Code Table. If the system code table has been customized, the valid values could be different. To verify which options are acceptable in your APM system, via Configuration Manager, refer to the appropriate table. | ||||||||||||||||||||
Inspection Sequence Number |
MI_DP_INSP_SEQ_NBR |
Numeric | None | ||||||||||||||||||||
Insulated Flag |
MI_TML_INSLTED_FLG |
Boolean |
Enter True or False. The default value is False. | ||||||||||||||||||||
TML Comment | MI_DP_COMMNT_CHR | Character (255) | None | ||||||||||||||||||||
Minimum Thickness |
MI_TML_MIN_THICK_NBR |
Numeric | If you do not enter a value in this cell, the value in the Default T-Min (Inches) cell on the TML_CAS worksheet is used. | ||||||||||||||||||||
Additional Thickness |
MI_THICK_MEASU_LOCAT_ADDIT_THI |
Numeric | None | ||||||||||||||||||||
Excluded From Analysis | MI_DP_EXCL_FROM_ANALYSIS_FLG | Logical | Enter True or False. The default value is False. | ||||||||||||||||||||
Number of Readings |
MI_TML_READ_NUM_N |
Numeric | Enter a number between 1 and 26. The default value is 1. | ||||||||||||||||||||
Design Code |
MI_TML_DSGN_CODE_CHR |
Character (50) |
In the baseline APM system, this cell may only contain one of the following System Code IDs based on the value in the Component Type cell:
The list in this field is populated by the DSCD System Code Table. If the system code table has been customized, the valid values could be different. To verify which options are acceptable in your APM system, via Configuration Manager, refer to the appropriate table. | ||||||||||||||||||||
Code Year (T-Min Formula) |
MI_TML_CODE_YEAR_C |
Character (4) |
A value is required if the value in the Design Code cell is not N/A. This cell may only contains one of the following values:
| ||||||||||||||||||||
Code Year (Allowable Stress Lookup) |
MI_TML_CODE_YEAR_STRESS_C |
Character (4) |
A value is required if the value in the Design Code cell is not N/A. The following table provides the valid values that you can enter in this cell based on the value in the Design Code cell.
| ||||||||||||||||||||
Material Specification |
MI_TML_MAT_SPEC_CHR |
Character |
A value is required if the value in the Override Allowable Stress cell is False, and if you want APM to calculate T-min values. Refer to the (Picklist) worksheet in the data loader workbook for valid values that you can enter in this cell based on the values in the Design Code and Code Year (Allowable Stress Lookup) cells. | ||||||||||||||||||||
Material Grade |
MI_TML_MAT_GRADE_CHR |
Character (50) |
A value is required if the value in the Override Allowable Stress cell is False, and if you want APM to calculate T-min values. Refer to the (Picklist) worksheet in the data loader workbook for valid values that you can enter in this cell based on the values in the Design Code, Code Year (Allowable Stress Lookup), and Material Specification cells. | ||||||||||||||||||||
Material Type |
MI_TML_MATER_TYPE_CHR |
Character | None | ||||||||||||||||||||
Design Pressure |
MI_TML_DSGN_PRESS_NBR |
Numeric | A value is required if you want APM to calculate T-min values. | ||||||||||||||||||||
Design Temperature |
MI_TML_DSGN_TEMP_NBR |
Numeric | A value is required if you want APM to calculate T-min values. | ||||||||||||||||||||
Nominal Thickness |
MI_TML_NOM_THICK_NBR |
Numeric | None | ||||||||||||||||||||
Override Allowable Stress | MI_TML_OVRD_ALLOW_STRES_F | Boolean |
Enter True or False. | ||||||||||||||||||||
Allowable Stress |
MI_TML_ALLOWABLE_STRESS_N |
Numeric |
A value is required if the value in the Override Allowable Stress cell is True, and you want APM to calculate T-min values. | ||||||||||||||||||||
Outside Diameter |
MI_TML_OUTSD_DIAM_NBR |
Numeric |
A value is required if all of the following conditions are satisfied:
| ||||||||||||||||||||
Inside Diameter |
MI_TML_INSD_DIAM_NBR |
Numeric |
A value is required if all of the following conditions are satisfied:
| ||||||||||||||||||||
Joint Factor |
MI_TML_JOINT_EFF_NBR |
Numeric |
A value is required if all of the following conditions are satisfied:
The default value is 1. | ||||||||||||||||||||
Corrosion Allowance |
MI_TML_CORR_ALLOW_NBR |
Numeric | None | ||||||||||||||||||||
Piping Nominal Diameter - NPS |
MI_TML_NOM_DIAM_NBR |
Numeric |
Refer to the (Picklist) worksheet in the data loader workbook for a list of values that you can enter in this cell. The values in the Piping Nominal Diameter - NPS and Piping Nominal Diameter - DN cells are mapped using the Piping Properties reference table. Therefore, if you enter a value in one of these cells, the other field is populated with the mapped value after you load data. If you enter a value that is not mapped to the value in the Piping Nominal Diameter - DN cell, then the value in this cell is ignored, and the corresponding field is populated with the value mapped to the value in the Piping Nominal Diameter - DN cell. For example, if the value in the Piping Nominal Diameter - DN cell is 6, then the value in this cell must be 0.125. If you enter a different value in this cell or leave it blank, then the value 0.125 is used to populate the corresponding field in APM. | ||||||||||||||||||||
Piping Nominal Diameter - DN |
MI_TML_PIPING_NOM_DIAM_DN_N |
Numeric |
Refer to the (Picklist) worksheet in the data loader workbook for a list of values that you can enter in this cell. The values in the Piping Nominal Diameter - NPS and Piping Nominal Diameter - DN cells are mapped using the Piping Properties reference table. Therefore, if you enter a value in one of these cells, the other field is populated with the mapped value after you load data. | ||||||||||||||||||||
Schedule |
MI_TML_SCHED_CHR |
Character (50) | A value is required if you have entered a value in the Piping Nominal Diameter - NPS cell. Refer to the (Picklist) worksheet in the data loader workbook for a list of values that you can enter in this cell based on the value in the Piping Nominal Diameter - NPS cell. | ||||||||||||||||||||
Piping Formula |
MI_TML_PIPING_FORMULA_C |
Character (4) |
In the baseline APM system, this cell may only contain one of the following System Code IDs based on the values in the Design Code cell:
The list in this field is populated by the PIPFMU System Code Table. If the system code table has been customized, the valid values could be different. To verify which options are acceptable in your APM system, via Configuration Manager, refer to the appropriate table. | ||||||||||||||||||||
Mechanical Allowance |
MI_TML_MECH_ALLOWANCE_N |
Numeric | The default value is 0. | ||||||||||||||||||||
Design Factor |
MI_TML_DESIGN_FACTOR_N |
Numeric |
A value is required if all of the following conditions are satisfied:
The default value is 1. | ||||||||||||||||||||
Temperature Factor |
MI_TML_TEMP_FACTOR_N |
Numeric | A value is required if the value in the Component Type cell is Piping, and if you want APM to calculate T-min values. The default value is 1. | ||||||||||||||||||||
Tank Type |
MI_TML_TANK_TYPE_C |
Character (50) |
In the baseline APM system, this cell may only contain one of the following System Code IDs:
The list in this field is populated by the TNKT System Code Table. If the system code table has been customized, the valid values could be different. To verify which options are acceptable in your APM system, via Configuration Manager, refer to the appropriate table. | ||||||||||||||||||||
Shell Type |
MI_TML_SHELL_TYPE_C |
Character (50) | None | ||||||||||||||||||||
API Method |
MI_TML_API_METHOD_C |
Character (50) | None | ||||||||||||||||||||
Plate Thickness |
MI_TML_PLATE_THICKNESS_N |
Numeric |
A value is required if all of the following conditions are satisfied:
| ||||||||||||||||||||
Minimum Yield Strength |
MI_TML_MIN_YIELD_STR_N |
Numeric |
A value is required if all of the following conditions are satisfied:
| ||||||||||||||||||||
Minimum Tensile Strength |
MI_TML_MIN_TENSILE_STR_N |
Numeric |
A value is required if all of the following conditions are satisfied:
| ||||||||||||||||||||
Course Height |
MI_TML_COURSE_HEIGHT_N |
Numeric | None | ||||||||||||||||||||
Course Number |
MI_TML_COURSE_NUMBER_N |
Numeric |
A value is required if all of the following conditions are satisfied:
| ||||||||||||||||||||
Fill Height |
MI_TML_FILL_HEIGHT_N |
Numeric | None | ||||||||||||||||||||
Specific Gravity |
MI_TML_SPECIFIC_GRAVITY_N |
Numeric |
A value is required if all of the following conditions are satisfied:
| ||||||||||||||||||||
Floor Plate has Detection? |
MI_TML_FLR_PLATE_DETECTION_L |
Boolean |
Enter True or False. The default value is False. | ||||||||||||||||||||
Floor Plate has Reinforced Lining? |
MI_TML_FLR_PLATE_REINFORCED_LINING_L |
Boolean |
Enter True or False. The default value is False. | ||||||||||||||||||||
Maximum Operating Fill Height |
MI_TML_MAX_OP_FILL_HEIGHT_N |
Numeric |
A value is required if all of the following conditions are satisfied:
| ||||||||||||||||||||
Distance From the Bottom |
MI_TML_DIST_FROM_BOTT_NBR |
Numeric | None | ||||||||||||||||||||
Tank Diameter |
MI_TML_TANK_DIAMETER_N |
Numeric |
A value is required if all of the following conditions are satisfied:
| ||||||||||||||||||||
Vessel Type |
MI_TML_VESSEL_TYPE_C |
Character (50) |
In the baseline APM system, this cell may only contain one of the following System Code IDs:
The list in this field is populated by the VSTP System Code Table. If the system code table has been customized, the valid values could be different. To verify which options are acceptable in your APM system, via Configuration Manager, refer to the appropriate table. | ||||||||||||||||||||
PV Formula |
MI_TML_PV_FORMULA_C |
Character (10) |
In the baseline APM system, this cell may only contain one of the following System Code IDs:
The list in this field is populated by the PVFMU System Code Table. If the system code table has been customized, the valid values could be different. To verify which options are acceptable in your APM system, via Configuration Manager, refer to the appropriate table. | ||||||||||||||||||||
Dish Radius |
MI_TML_DISH_RADIUS_N |
Numeric |
A value is required if:
| ||||||||||||||||||||
Knuckle Radius |
MI_TML_KNUCKLE_RADIUS_N |
Numeric |
A value is required if:
| ||||||||||||||||||||
apex_angle |
MI_TML_APEX_ANGLE_N |
Numeric |
A value is required if:
| ||||||||||||||||||||
Inside Radius |
MI_TML_INSIDE_RADIUS_N |
Numeric |
A value is required if all of the following conditions are satisfied:
| ||||||||||||||||||||
Outside Radius |
MI_TML_OUTSIDE_RADIUS_N |
Numeric |
A value is required if all of the following conditions are satisfied:
| ||||||||||||||||||||
Head Diameter |
MI_TML_HEAD_DIAMETER_N |
Numeric | None |
TML_CAS Worksheet
On the TML_CAS worksheet, you will specify Corrosion Analysis Settings records for a TML.
- If you do not enter values on this worksheet, and:
- If the TML is linked to a TML Group, then the values on the TML_Group_CAS worksheet for the associated TML Group are used.
- If the TML is not linked to a TML Group, the values that you enter on the Asset_CAS or Functional_Location_CAS worksheet are used.
- Otherwise, the values on the TML_CAS worksheet are used.
Field Caption |
Field ID |
Data Type (Length) |
Comments |
---|---|---|---|
Equipment ID |
MI_EQUIP000_EQUIP_ID_C |
Character (255) |
This column requires at least one cell to have a value. This column appears only in the Thickness Monitoring (TM) Equipment Data Loader. To upload Functional Location data in the same worksheet, specify the Functional Location ID in this column. |
Functional Location ID |
MI_FNCLOC00_FNC_LOC_C |
Character (255) |
This column requires at least one cell to have a value. This column appears only in the Thickness Monitoring (TM) Functional Location Data Loader. |
CMMS System |
MI_EQUIP000_SAP_SYSTEM_C |
Character (255) |
If the Equipment or the Functional Location record for an asset has a value in the CMMS System field, enter that value in this column. To upload Functional Location data in the same worksheet, specify the CMMS System for the Functional Location value in this column. |
Equipment Technical Number |
MI_EQUIP000_EQUIP_TECH_NBR_C |
Character (255) |
This column appears only in the Thickness Monitoring (TM) Equipment Data Loader. If you are required to enter a value for the CMMS System cell for an asset, and the Equipment record for the asset has a value in the Equipment Technical Number field, enter that value in this column. If there is no value in the CMMS System field, this column can be blank, even if the Equipment record contains a value for the Equipment Technical Number field. |
Inspection Type | MI_CA_SET_ANALY_TYPE_CHR | Character (50) | If you do not enter a value in this cell, then data in this row is not loaded. If the TML is linked to a TML Group, then this cell may only contain a value that you have entered in the Inspection Type cell for the associated TML Group on the TML_Group_CAS worksheet. Otherwise, this cell may only contain a value that you have entered in the Inspection Type cell for the associated asset on the Asset_CAS worksheet. |
TML Group ID | MI_TMLGROUP_ID_C |
Character (50) | A value is required if the TML is linked to a TML Group. The value should match the value in the TML Group ID cell for the corresponding TML on the TML worksheet. If you do not enter a value in this cell, the TML is directly linked to the Asset. |
TML ID |
MI_DP_ID_CHR |
Character (50) |
A value is required and must be unique. |
Std Deviation Factor | MI_CA_SET_STD_DEV_FCTR_NBR | Numeric |
If you do not enter a value in this cell, and if the TML is linked to a TML Group, then the value in the corresponding cell on the TML_Group_CAS worksheet is used. Otherwise, the value in the corresponding cell on the Asset_CAS or the Functional_Location_CAS worksheet is used. |
Default Inspection Interval (Months) | MI_CA_SET_INSP_INTRVL_NBR | Numeric |
If you do not enter a value in this cell, and if the TML is linked to a TML Group, then the value in the corresponding cell on the TML_Group_CAS worksheet is used. Otherwise, the value in the corresponding cell on the Asset_CAS or the Functional_Location_CAS worksheet is used. |
Minimum Corrosion Rate (Mils/year) | MI_CA_SET_MN_CR_NBR | Numeric |
If you do not enter a value in this cell, and if the TML is linked to a TML Group, then the value in the corresponding cell on the TML_Group_CAS worksheet is used. Otherwise, the value in the corresponding cell on the Asset_CAS or the Functional_Location_CAS worksheet is used. |
Allowable Measurement Variance (inches) | MI_CA_SET_ALLOW_VARIA_NBR | Numeric |
If you do not enter a value in this cell, and if the TML is linked to a TML Group, then the value in the corresponding cell on the TML_Group_CAS worksheet is used. Otherwise, the value in the corresponding cell on the Asset_CAS or the Functional_Location_CAS worksheet is used. |
Corrosion Rate Variance | MI_CA_SET_CRV_N | Numeric |
If you do not enter a value in this cell, and if the TML is linked to a TML Group, then the value in the corresponding cell on the TML_Group_CAS worksheet is used. Otherwise, the value in the corresponding cell on the Asset_CAS or the Functional_Location_CAS worksheet is used. |
Measurements Worksheet
On the Measurements worksheet, you will specify the TMs (that are or will be represented by Thickness Measurement records) that you want to create or update.
Field Caption |
Field ID |
Data Type (Length) |
Comments |
---|---|---|---|
Equipment ID |
MI_EQUIP000_EQUIP_ID_C |
Character (255) |
This column requires at least one cell to have a value. This column appears only in the Thickness Monitoring (TM) Equipment Data Loader. To upload Functional Location data in the same worksheet, specify the Functional Location ID in this column. |
Functional Location ID |
MI_FNCLOC00_FNC_LOC_C |
Character (255) |
This column requires at least one cell to have a value. This column appears only in the Thickness Monitoring (TM) Functional Location Data Loader. |
CMMS System |
MI_EQUIP000_SAP_SYSTEM_C |
Character (255) |
If the Equipment or the Functional Location record for an asset has a value in the CMMS System field, enter that value in this column. To upload Functional Location data in the same worksheet, specify the CMMS System for the Functional Location value in this column. |
Equipment Technical Number |
MI_EQUIP000_EQUIP_TECH_NBR_C |
Character (255) |
This column appears only in the Thickness Monitoring (TM) Equipment Data Loader. If you are required to enter a value for the CMMS System cell for an asset, and the Equipment record for the asset has a value in the Equipment Technical Number field, enter that value in this column. If there is no value in the CMMS System field, this column can be blank, even if the Equipment record contains a value for the Equipment Technical Number field. |
TML Group ID | MI_TMLGROUP_ID_C | Character (50) |
A value is required if the corresponding TML is linked to a TML Group. The value that you enter must match the value in the TML Group ID cell for the corresponding TML on the TML worksheet. |
TML ID |
MI_DP_ID_CHR |
Character (50) |
A value is required and should match the value in the TML ID cell for the corresponding TML on the TML worksheet. Otherwise, data in this row is not loaded. |
Readings |
MI_THICK_MEASU_READI_C |
Character (2000) |
A value is required. Enter a number greater than 0. If you have multiple readings, separate them with semicolons. If you do not enter a value in this cell, the data in this row is not loaded. |
Measurement Date |
MI_DP_MEAS_TAKEN_DT |
Date |
Enter a value in the following format: YYYY-MM-DD hh:mm:ss If you do not enter a value, the current date is used. |
Measurement Taken By | MI_DP_MEAS_TAKEN_BY_CHR | Character |
Enter a value in the following format: <Last Name>, <First Name> ~ <User ID> When you want to create a Thickness Monitoring record using the data loader workbook, and if your user ID appears in the Measurement Taken By field on a Thickness Measurement datasheet, then you need not enter a value in this cell. The appropriate value is automatically populated in the Measurement Taken By field after you load data. If not, enter a value that matches the user ID of a Security User in APM. Otherwise, the data in this row is not loaded. If, however, you do not want the Measurement Taken by field to be populated automatically, using the data loader workbook, update the Thickness Monitoring record by leaving the Measurement Taken By cell blank. |
Measurement Comment |
MI_DP_MEAS_COMMENT_CHR |
Character (255) | None |
Temperature |
MI_THICK_MEAS_TEMP_TAKEN_AT_N |
Numeric | None |
About the Thickness Monitoring (TM) Data Loaders Load Verification
About This Task
Procedure
- Access the details of the import job. These details indicate if any errors were encountered during the data load. The log may help account for any records that are not loaded.
- In Thickness Monitoring or Record Manager, access the assets specified in the data loader workbook, and then verify that the expected TML Groups and TMLs are present or updated, and that any associated records that you expected to be created are also present in the database.
- To view a list of TML Groups created after a specific date, run the following query:
- For an SQL database:
SELECT [MI_TMLGROUP].[MI_TMLGROUP_ID_C] "TML Group ID", [MI_TMLGROUP].[MI_TMLGROUP_DESCR_C] "Description", [MI_TMLGROUP].LAST_UPDT_DT "LAST_UPDT_DT" FROM [MI_TMLGROUP] WHERE [MI_TMLGROUP].LAST_UPDT_DT >= CONVERT(VARCHAR(255), (? :d :caption='Enter a Date'), 110)
- For an Oracle or Postgres database:
SELECT [MI_TMLGROUP].[MI_TMLGROUP_ID_C] "TML Group ID", [MI_TMLGROUP].[MI_TMLGROUP_DESCR_C] "Description", [MI_TMLGROUP].LAST_UPDT_DT "LAST_UPDT_DT", [MI_TMLGROUP].ENTY_ID "ENTY_ID" FROM [MI_TMLGROUP] WHERE [MI_TMLGROUP].LAST_UPDT_DT >= to_date(to_char((? :d :caption='Enter a Date'), 'mm/dd/yyyy'), 'mm/dd/yyyy')
- For an SQL database:
- To view a list of TMLs created after a specific date, run the following query:
- For an SQL database:
SELECT [MI Thickness Measurement Location].[MI_DP_ID_CHR] "TML ID", [MI Thickness Measurement Location]. [MI_DP_ASSET_ID_CHR] "TML Asset ID", [MI Thickness Measurement Location].LAST_UPDT_DT "LAST_UPDT_DT" FROM [MI Thickness Measurement Location] WHERE [MI Thickness Measurement Location].LAST_UPDT_DT >= CONVERT(VARCHAR(255), (? :d :caption='Enter a Date'), 110)
- For an Oracle or Postgres database:
SELECT [MI Thickness Measurement Location].[MI_DP_ID_CHR] "TML ID", [MI Thickness Measurement Location]. [MI_DP_ASSET_ID_CHR] "TML Asset ID", [MI Thickness Measurement Location].LAST_UPDT_DT "LAST_UPDT_DT", [MI Thickness Measurement Location].ENTY_KEY "ENTY_KEY" FROM [MI Thickness Measurement Location] WHERE [MI Thickness Measurement Location].LAST_UPDT_DT >= to_date(to_char((? :d :caption='Enter a Date'), 'mm/dd/yyyy'), 'mm/dd/yyyy')
- For an SQL database:
- To view a list of Thickness Measurements created after a specific date, run the following query:
- For an SQL database:
SELECT [MI Thickness Measurement].[MI_THICK_MEASU_ID_CHR] "Measurement ID", [MI Thickness Measurement]. [MI_DP_MEAS_TAKEN_BY_CHR] "Measurement Taken By", [MI Thickness Measurement].[MI_THICK_MEAS_TML_KEY_C] "TML Key", [MI Thickness Measurement].LAST_UPDT_DT "LAST_UPDT_DT" FROM [MI Thickness Measurement] WHERE [MI Thickness Measurement].LAST_UPDT_DT >= CONVERT(VARCHAR(255), (? :d :caption='Enter a Date'), 110)
- For an Oracle or Postgres database:
SELECT [MI Thickness Measurement].[MI_THICK_MEASU_ID_CHR] "Measurement ID", [MI Thickness Measurement]. [MI_DP_MEAS_TAKEN_BY_CHR] "Measurement Taken By", [MI Thickness Measurement].[MI_THICK_MEASU_READ_PF_C] "Readings Pass/Fail", [MI Thickness Measurement].[MI_THICK_MEAS_TML_KEY_C] "TML Key", [MI Thickness Measurement].LAST_UPDT_DT "LAST_UPDT_DT", [MI Thickness Measurement].ENTY_KEY "ENTY_KEY" FROM [MI Thickness Measurement] WHERE [MI Thickness Measurement].LAST_UPDT_DT >= to_date(to_char((? :d :caption='Enter a Date'), 'mm/dd/yyyy'), 'mm/dd/yyyy')
- For an SQL database:
Configure Data Loader Transaction Scopes
Before You Begin
About This Task
- Asset Level Data
- TML Groups in 100-count batches
- Thickness Measurement Locations in 100-count batches
- Measurements in 250-count batches
However, based on the speed of your network connection, configuration of the APM Server, or other such factors, you may notice transaction scope errors while uploading large batches of data. To resolve this issue, you can configure the transaction scopes to reduce the number of TML Groups, TMLs, and Measurements per batch.