Inspections
About Inspections
Inspections are a way to document, manage, and analyze data associated with the inspections of equipment and locations in your facility.
About Types of Inspections
You will record the results of each inspection in an Inspection and its linked successors. The baseline APM database contains Inspection families that you can use for recording the results of each type of inspection.
Details
Using Inspection Management, you can record inspection results for the following types of inspections:
- Shell and tube heat exchanger inspections.
- General routine inspections performed against any piece of equipment or location for compliance purposes.
- General routine inspections performed against any piece of equipment or location by operators versus inspectors (does not necessarily meet compliance standards).
- Hydrostatic tests (i.e., the process of filling a pressure vessel with liquid, such as water, and increasing the internal pressure to test for leaks).
- External and internal pressure vessel inspections (following API 510 standards).
- Internal exchanger inspections (following API 510 standards).
- External piping inspections (following API 570 standards).
- External and internal tank inspections (following API 653 standards).
- External visual inspections of pressure relief devices (PRDs).
- External functional inspections of PRDs (following API 576 standards).
Baseline Inspection Families
The following table lists the baseline Inspection families and the type of inspection to which each corresponds.
Family | Inspection Type |
---|---|
Bundle Inspection Bundle Sub-Inspection | Shell and tube heat exchanger inspections. |
Full Inspection | General routine inspections performed against any piece of equipment or location for compliance purposes. |
General Inspection | General routine inspections performed against any piece of equipment or location by operators versus inspectors (does not necessarily meet compliance standards). |
Pressure Test Inspection Pressure Test Sub Inspection Report | Hydrostatic tests. |
API 510 External Checklist API 510 Internal Exchanger Checklist API 510 Internal Checklist | External and internal pressure vessel inspections and internal exchanger inspections (following API 510 standards). |
API 570 External Checklist | External piping inspections (following API 570 standards). |
API 653 External Checklist API 653 Internal Checklist | External and internal tank inspections (following API 653 standards). |
External PRD Checklist | External visual inspections of PRDs. |
PRD Pop Test Checklist | External functional inspections of PRDs (following API 576 standards). |
About Inspection Reports
The baseline Inspection Management module includes reports that can be used to view information about an inspection. When you view an Inspection report, you are viewing a main report and various subreports that exist in the Catalog. These reports are based on supporting queries that gather information from the Inspection record and records to which it is linked.
The following table lists the main reports that correspond with each Inspection subfamily, the query and subreports that are associated with each main report, and the sections that are included in each main report. Note that the subreports are not meant to be run independently of the associated main report.
Inspection Subfamily | Query Behind Main Report | Main Report(s) | Contributing Reports | Sections Included in Main Report |
---|---|---|---|---|
Bundle Inspection | MI INSPBUND | Bundle Inspection Report |
|
|
Checklists | Checklist Report Query | Checklist Inspection Report |
|
|
Checklists | Checklist Report Query | Blank Checklist Inspection Report | Checklist Finding Report | Checklist Findings |
Full Inspection | MI INSPFULL | Full Inspection Report |
|
|
General Inspection | MI INSP GEN | General Inspection Report |
|
|
Pressure Test Inspection | MI INSPPTST | Pressure Test Inspection Report |
|
|
Interpreting Inspection Reports
In the baseline database, one report is provided for each of the following Inspection families:
- Checklists
- Bundle Inspection
- Full Inspection
- General Inspection
- Pressure Test Inspection
While each family has its own report, many of the sections in the reports are common to all of the reports. This section of the documentation describes the sections that are included in the baseline reports and indicates whether or not the section is common to all reports.
Asset Corrosion Analysis
The Asset Corrosion Analysis section appears when an Asset Corrosion Analysis in Thickness Monitoring is linked to the inspection for which you are generating a report. This section displays information that is stored in the Asset Corrosion Analysis. An example of the Asset Corrosion Analysis section is shown in the following image.

The following table lists the items that are included in the Asset Corrosion Analysis section and their corresponding fields. Note that the table displays field captions, which may differ from datasheet captions.
Report item | Asset Corrosion Analysis field |
---|---|
Controlling Corrosion Rate | Controlling Corrosion Rate |
Controlling Next Inspection Date | Controlling Next Inspection Date |
Controlling Remaining Life | Controlling Remaining Life |
Controlling Retire Date | Controlling Retire Date |
Bundle Inspection
The Bundle Inspection section appears only if you are viewing a report for a Bundle Inspection record. This section displays information that is stored in the Bundle Inspection record. An example of the Bundle Inspection section is shown in the following image.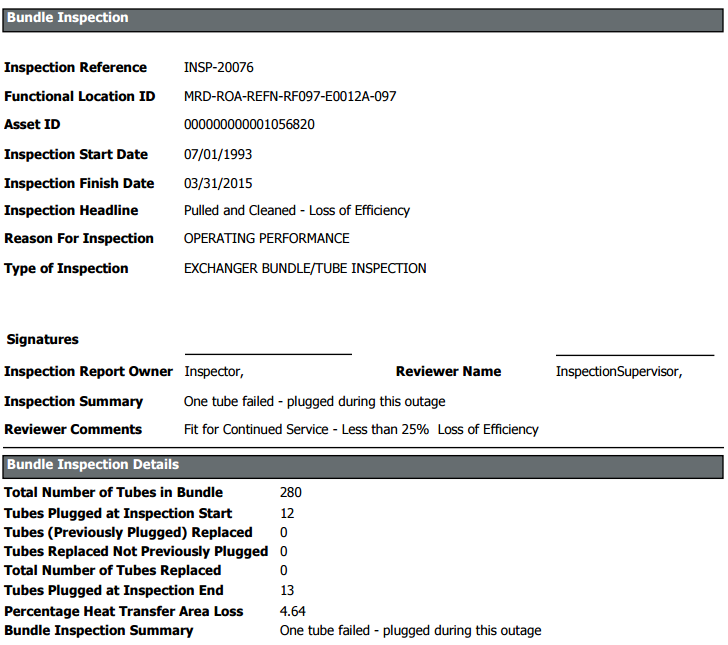
The following table lists the items that are included in the Bundle Inspection section and their corresponding Bundle Inspection fields. Note that the table displays field captions, which may differ from datasheet captions.
Report item | Bundle Inspection field |
---|---|
Asset ID | Asset ID |
Bundle Inspection Summary | Inspection Summary |
Functional Location ID | Functional Location ID |
Inspection Finish Date ) | Completion Date |
Inspection Headline | Inspection Headline |
Inspection Reference | Inspection Reference |
Inspection Start Date | Commencement Date |
Inspection Summary | Inspection Summary |
Inspection Report Owner | Inspection Report Owner |
Percentage Heat Transfer Area Loss | Percentage Heat Transfer Area Loss |
Reason for Inspection | Reason for Inspection |
Reviewer Comments | Reviewers Comments |
Reviewer Name | Reviewers Name |
Total Number of Tubes in Bundle | Total Number of Tubes in Bundle |
Total Number of Tubes Replaced | Total Number of Tubes Replaced at Inspection End |
Tubes (Previously Plugged) Replaced | Tubes (Plugged At Start) Replaced |
Tubes Plugged at Inspection End | Total Number of Tubes Plugged at Inspection End |
Tubes Plugged at Inspection Start | Tubes Plugged at Inspection Start |
Tubes Replaced Not Previously Plugged | Tubes (Not Previously Plugged) Replaced |
Type of Inspection | Type of Inspection |
Bundle Sub Inspection
The Bundle Sub Inspections section appears if you are viewing a report for one of the following records:
- Checklists (unless you are viewing a blank Checklist Inspection report)
- Full Inspection
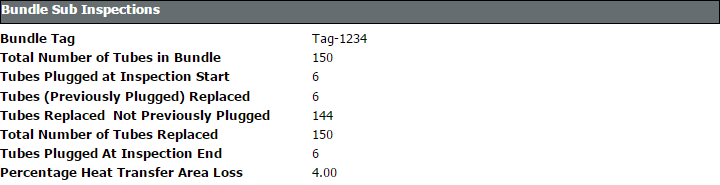
Report item | Bundle Sub-inspection field |
---|---|
Bundle Inspection Summary | Inspection Summary |
Bundle Tag | Asset ID |
Percentage Heat Transfer Area Loss | Percentage Heat Transfer Area Loss |
Total Number of Tubes in Bundle | Total Number of Tubes in Bundle |
Total Number of Tubes Replaced | Total Number of Tubes Plugged at Inspection End |
Tubes (Previously Plugged) Replaced | Tubes (Plugged At Start) Replaced |
Tubes Plugged at Inspection End | Total Number of Tubes Plugged at Inspection End |
Tubes Plugged at Inspection Start | Tubes Plugged at Inspection Start |
Tubes Replaced Not Previously Plugged | Tubes (Not Previously Plugged) Replaced |
Checklist Findings
The Checklist Findings section appears only if you are viewing a Checklist Inspection report. The items that appear in this section depend upon the finding sections that are associated with the Inspection family for which you ran the report and will vary based on what type of Checklist Inspection report you are viewing. If you are viewing a Checklist Inspection report that is:
- Associated with a particular Inspection record, this section displays values that are stored in the Checklist Finding records that are linked to the Inspection record.
- A blank Checklist Inspection report, the finding sections associated with the Inspection family for which you ran the report will appear, but the cells in the Value and Finding Summary columns will be empty.
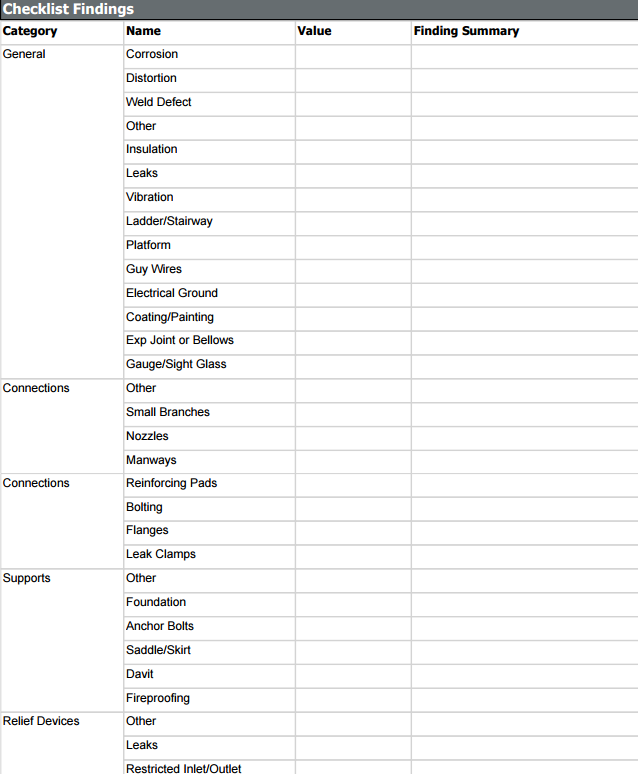
Findings
The Findings section appears in all reports except blank Checklist Inspection reports and displays information that is stored in the General Finding records that are linked to the Inspection record. An example of the Findings section is shown in the following image.
Report item | General Finding field |
---|---|
Action Taken Code | Action Taken Code |
Action Taken Description | Action Taken Description |
Deterioration Mechanism | Deterioration Mechanism |
Deterioration Mode | Deterioration Mode |
Headline | Headline |
Location Details | Location Details |
Predictable | Predictable |
Predicted | Predicted |
Profile Item | Inspection Profile Item |
Summary | Finding Summary |
Type | Type |
Full Inspection
The Full Inspection section appears only if you are viewing a report for a Full Inspection record. This section displays information that is stored in the Full Inspection record. An example of a Full Inspection section is shown in the following image.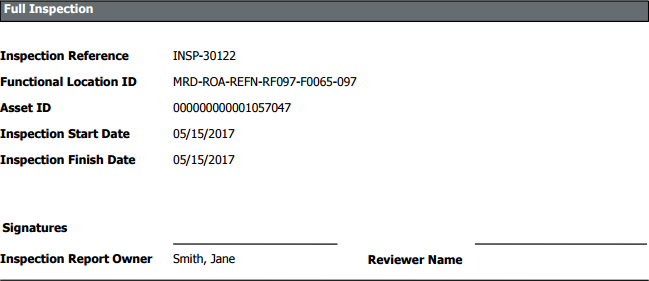
The following table lists the items that are included in the Full Inspection section and their corresponding Full Inspection fields. Note that the table displays field captions, which may differ from datasheet captions.
Report item | Full Inspection field |
---|---|
Asset ID | Asset ID |
Functional Location ID | Functional Location ID |
Inspection Finish Date | Completion Date |
Inspection Headline | Inspection Headline |
Inspection Reference | Inspection Reference |
Inspection Start Date | Commencement Date |
Inspection Summary | Inspection Summary |
Inspection Report Owner | Inspection Report Owner |
Reason for Inspection | Reason of Inspection |
Reviewer Comments | Reviewers Comments |
Reviewer Name | Reviewers Name |
Type of Inspection | Type of Inspection |
Report item | Reference Document Field |
---|---|
ID | ID |
Description | Description |
General Inspection
The General Inspection section appears only if you are viewing a report for a General Inspection record. This section displays information that is stored in the General Inspection record. An example of a General Inspection section is shown in the following image.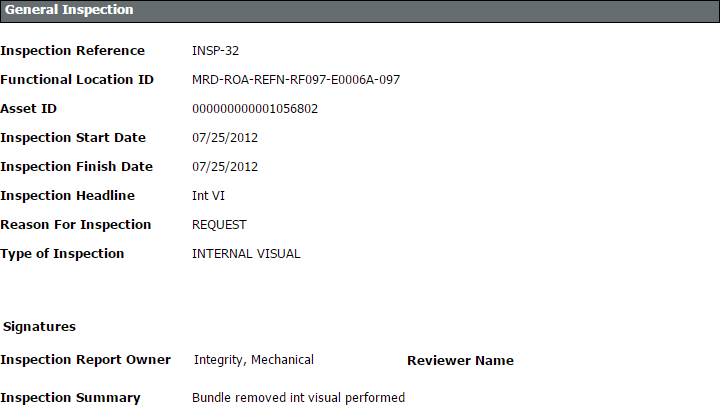
The following table lists the items that are included in the General Inspection section and their corresponding General Inspection fields. Note that the table displays field captions, which may differ from datasheet captions.
Report item | General Inspection field |
---|---|
Asset ID | Asset ID |
Functional Location ID | Functional Location ID |
Inspection Finish Date | Completion Date |
Inspection Headline | Inspection Headline |
Inspection Reference | Inspection Reference |
Inspection Start Date | Commencement Date |
Inspection Summary | Inspection Summary |
Inspection Report Owner | Inspection Report Owner |
Reason for Inspection | Reason of Inspection |
Reviewer Comments | Reviewers Comments |
Reviewer Name | Reviewers Name |
Type of Inspection | Type of Inspection |
Report item | Reference Document Field |
---|---|
ID | ID |
Description | Description |
Inspection Team Members
The Inspection Team Members section appears in all reports except blank Checklist Inspection reports and displays information that is stored in the Inspection Team Member records that are linked to the Inspection record. An example of the Inspection Team Members section is shown in the following image.
Pressure Test Inspection
The Pressure Test Inspection section appears only if you are viewing a report for a Pressure Test Inspection record. This section displays information that is stored in the Pressure Test Inspection record. An example of the Pressure Test Inspection section is shown in the following image.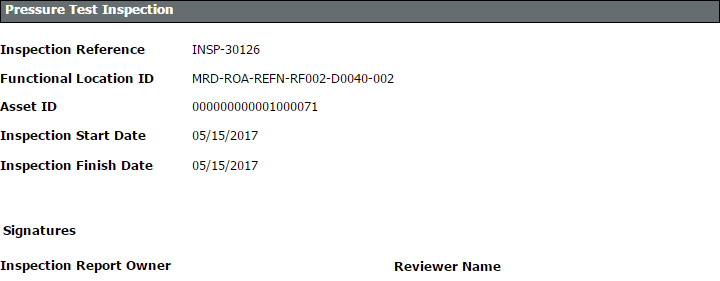
The following table lists the items that are included in the Pressure Test Inspection section and their corresponding Pressure Test Inspection fields. Note that the table displays field captions, which may differ from datasheet captions.
Report item | Pressure Test Inspection field |
---|---|
# of Gauges Used | No. of Gauges Used (Shell) |
# of Gauges Used | No. of Gauges Used (Tube) |
Asset ID | Asset ID |
Functional Location ID | Functional Location ID |
Inspection Finish Date | Completion Date |
Inspection Headline | Inspection Headline |
Inspection Reference | Inspection Reference |
Inspection Start Date | Commencement Date |
Inspection Summary | Inspection Summary |
Inspection Report Owner | Inspection Report Owner |
Reason for Inspection | Reason for Inspection |
Reviewer Comments | Reviewers Comments |
Reviewer Name | Reviewers Name |
SRV Set Pressure | SRV Set Pressure (Shell) |
SRV Set Pressure | SRV Set Pressure (Tube) |
Test Comments | Test Comments (Shell) |
Test Comments | Test Comments (Tube) |
Test Duration | Test Duration (Shell) |
Test Duration | Test Duration (Tube) |
Test Media | Test Media (Shell) |
Test Media | Test Media (Tube) |
Test Media Temp. | Test Media Temperature (Shell) |
Test Media Temp. | Test Media Temperature (Tube) |
Test Pressure | Test Pressure (Shell) |
Test Pressure | Test Pressure (Tube) |
Type of Inspection | Type of Inspection |
Witnessed By | Witnessed By (Shell) |
Witnessed By | Witnessed By (Tube) |
Pressure Test Sub Inspections Section
The Pressure Test Sub Inspections section appears if you are viewing a report for one of the following records:- Bundle Inspection
- Checklists (except blank Checklist Inspection reports)
- Full Inspection
- General Inspection
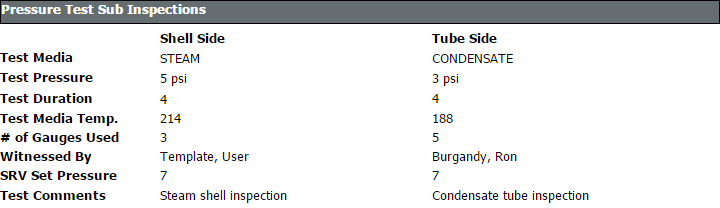
The following table lists the items that are included in the Pressure Test Sub Inspections section and their corresponding Pressure Test Sub-Inspection fields. Note that the table displays field captions, which may differ from datasheet captions.
Report item | Pressure Test Sub-Inspection field |
---|---|
# of Gauges Used | No. of Gauges Used (Shell) |
# of Gauges Used | No. of Gauges Used (Tube) |
SRV Set Pressure | SRV Set Pressure (Shell) |
SRV Set Pressure | SRV Set Pressure (Tube) |
Test Comments | Test Comments (Shell) |
Test Comments | Test Comments (Tube) |
Test Duration | Test Duration (Shell) |
Test Duration | Test Duration (Tube) |
Test Media | Test Media (Shell) |
Test Media | Test Media (Tube) |
Test Media Temp. | Test Media Temperature (Shell) |
Test Media Temp. | Test Media Temperature (Tube) |
Test Pressure | Test Pressure (Shell) |
Test Pressure | Test Pressure (Tube) |
Witnessed By | Witnessed By (Shell) |
Witnessed By | Witnessed By (Tube) |
Recommendations
The Recommendations section is included in all reports except blank Checklist Inspection reports and displays information that is stored in the Inspection Recommendation records that are linked to the Inspection record. An example of the Recommendations section is shown in the following image.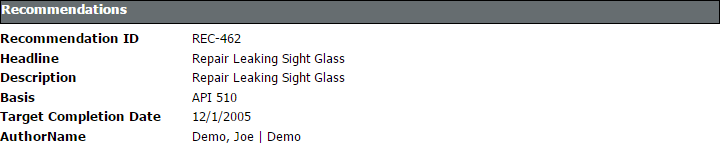
The following table lists the items that are included in the Recommendations section and their corresponding Inspection Recommendation fields. Note that the table displays field captions, which may differ from datasheet captions.
Report item | Inspection Recommendation field |
---|---|
Author Name | Author Name |
Basis | Recommendation Basis |
Description | Recommendation Description |
Headline | Recommendation Headline |
Profile Item | Inspection Profile Item |
Recommendation ID | Inspection Recommendation ID |
Target Completion Date | Target Completion Date |
Reference Documents
The Reference Documents section is included in all reports except blank Checklist Inspection reports and displays information that is stored in the Reference Document records that are linked to the Inspection record. An example of the Reference Documents section is shown in the following image.
The following table lists the items that are included in the Reference Documents section and their corresponding Reference Document fields. Note that the table displays field captions, which may differ from datasheet captions.
Report item | Reference Document field |
---|---|
Description | Description |
Document Path | Document Path |
Reference Document ID | ID |
About Inspection Checklists
The Inspection Finding Checklist represents subcomponents belonging to the item that you are inspecting. Since the subcomponents that you will need to inspect will differ based upon the type of inspection that you are performing, the items that appear in the Inspection Finding Checklist will differ based upon the Inspection subfamily.
Checklist Details
The baseline Inspection families are:
- Checklist Inspection Template
- External Checklist
- Internal Checklist
- Internal Exchanger Checklist
- PRD Pop Test Checklist
Each of these families is hard-coded to use a particular System Code Table to create the finding sections and rows that appear in the grid on the Inspection Findings Checklist page. The sections and rows on the Inspection Findings Checklist page are built from System Code Tables and referenced System Codes.
Example: API 653 External Checklist Findings
The baseline APM database contains the following System Code Table:
- ID: MI API 653 EXTERNAL CHECKLIST FINDING SECTIONS
- Description: API 653 External Checklist Finding Section
This System Code Table contains the following System Codes:
- General
- Connections
- Supports
Each of the System Codes that belong to this System Code Table contain referenced System Codes. For example, the System Code Supports contains the following referenced System Codes:
- Anchor Bolts
- Dike/Retaining Wall
- Foundation
- Other
Together, the System Code Tables, System Codes, and referenced System Codes determine which sections and rows you will see on the Inspection Finding Checklist page. Using this example:
- Each System Code belonging to the System Code Table MI API 653 EXTERNAL CHECKLIST FINDING SECTIONS becomes a finding section.
- In each finding section, each referenced System Code becomes a separate row.
Each field within the checklist can be modified by the user to best fit the work process.
About Active and Archived Inspections
Inspections that are still in the process of being completed or reviewed are referred to as Active Inspections.
Archived Inspections are Inspections that have been reviewed, locked, and archived.
Locking the Inspection record ensures that the information that you supplied will not be deleted or modified. After you lock an Inspection record, you cannot unlock it. You can lock Inspection records defined for any of the following families by accessing Record Manager.
- Bundle Inspection
- Full Inspection
- General Inspection
- Pressure Test Sub-Inspection
About Inspection Intervals
An inspection interval identifies the length of time between Equipment inspections. Various factors will impact the inspection intervals that you will define at various levels in your location hierarchy.
About Inspection Intervals
When populating the value in the Desired Interval field in Inspection Tasks, the APM System uses the value stored in the Time-Based Inspection Interval Settings that you defined.
Example: Inspection Intervals
For example, jurisdictional regulations might dictate that a particular inspection must be conducted every two months. However, your organizational policy might dictate that this particular inspection be conducted every 30 days. In this case, you would define an inspection interval of 30 days.
About Inspection Health Evaluations
Inspection Health Evaluations allow you to assign Health Assessment values to Inspections and Inspection Checklist Categories. When the Health Evaluations admin setting is enabled for an Inspection Event Family, the Health Evaluation icon is available for new inspections created in the same Inspection Event Family.
About Image Gallery
You can access the images stored within reference documents of a record in the image gallery. The gallery is provided in the inspection, its related records, and checklist categories. The image gallery displays images that have either been directly stored as reference documents within APM or provided as a reference document with an external network path.
The Description text box contains the value entered in the Description field of the currently selected reference document. This text box is disabled.
If the currently selected reference document is related to either a General Finding or a Checklist Finding record, the Finding Summary text box contains the value entered in the Finding Summary field of the finding record. This text box is disabled.
Access the Inspection Details Section
Procedure
Access Inspection Checklist
Procedure
Results
- You can now make adjustments to the Inspection Data section by accessing the Record Manager.
Create an Inspection
Before You Begin
If the asset that you are using does not have any existing inspections, you must access it through the Asset Hierarchy.
Procedure
Results
- Inspection findings will be generated based on your Inspection Scope and your Inspection Profile settings.
- The new inspection is saved. You can modify the inspection by accessing the datasheet, and then selecting
to save your changes.
- Full Inspection Event Family findings will be generated automatically.
- Checklist Inspections will never be generated automatically.
- Other Event Families will require event configurations.
- If you selected an Inspection Event that represents a Checklist Configuration Template, the Inspection Event from the family defined for the Checklist Configuration Template is generated, and all Checklist Findings defined by the Checklist Configuration Template are created.
- You can now access offline inspections.
What To Do Next
Assign Inspections to a User
Procedure
Delete an Inspection
Bulk Review Inspections
Procedure
Lock an Inspection
About This Task
After you create an Inspection record, you can lock it so that others cannot modify it. Locking the Inspection record ensures that the information that you provided is not deleted or modified.
Procedure
Results
All fields except for the following become disabled:
- Inspection Document Status
- Inspection Lock
- Reviewers Name
- Reviewers Comments
- Final Inspection Lock
- Published
View Related Record
Procedure
Add a Related Record
Procedure
Results

Link a Related Record to an Inspection
Procedure
Access Image Gallery for a Related Record
Procedure
Link Reference Document to an Inspection
Procedure
Results
Access Images for a Reference Document
Procedure
Unlink a Related Record from an Inspection
Procedure
Delete a Related Record
Procedure
Access Inspection Reports
Procedure
Access Reference Documents
Procedure
Add Inspection Confidence Evaluations
Procedure
Results
Review Inspection Confidence Evaluation
Before You Begin
- Make sure that the Risk Analyst resource role is assigned to you.
- Make sure that the Allow Risk Analyst to Review Inspection Confidence Evaluation Records check box is selected in Application Configurations section of the Inspection Configuration workspace.
Procedure
Results
- Any user who does not have the Risk Analyst resource role cannot add, update, or modify the Inspection Confidence Evaluation records.
- Your user name appears above the section to indicate other users about who locked the Inspection Confidence Evaluation records.
Delete Inspection Confidence Evaluations
Procedure
Update an Inspection Health Assessment
Procedure
Update a Checklist Category Health Assessment
Procedure
Bulk Printing of Inspection Reports
Using the bulk print functionality, you can generate multiple Inspection Reports at a time. The generated reports are stored in a location configured in SQL Server Reporting Services (SSRS). After you successfully generate the reports, you can download the reports as a .zip file.
The bulk printing process consists of the following steps:
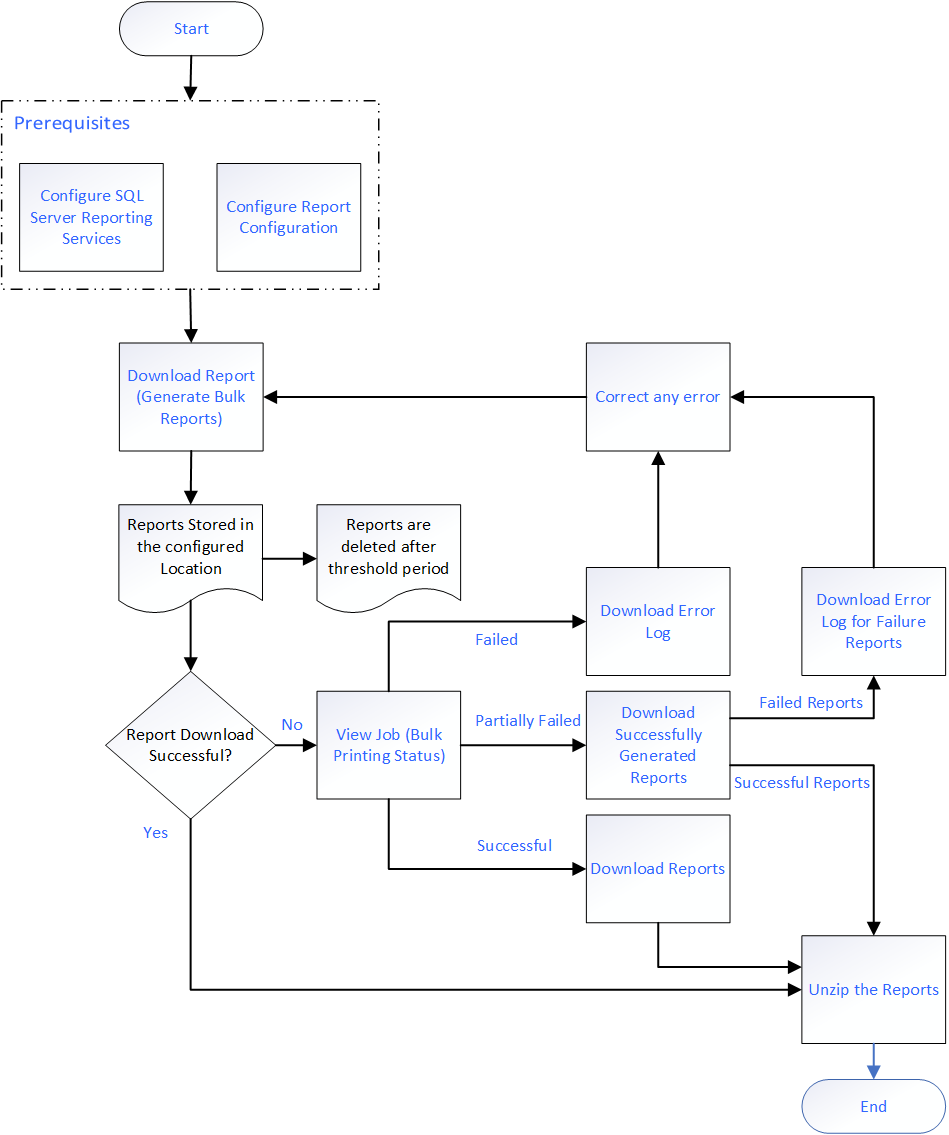
Print Bulk Inspection Reports
Before You Begin
- Make sure that following fields are configured in SQL Server Reporting Services:
- Bulk Report Storage Path
- Bulk Report Storage User Name
- Bulk Report Storage User Password
- Bulk Report Storage Threshold (Days)
- Make sure that a default report is configured in the Family Reports section of the family associated to the Inspection.
- Make sure that the families of the selected Inspections contain only SSRS reports with a single parameter.
Procedure
What To Do Next
View Bulk Printing Status
About This Task
- In progress: Contains the print jobs that are currently in progress.
- Successful: Contains the print jobs that are successfully completed. You can download the reports and the log files from this section.
- Failed: Contains the print jobs that failed. The print job fails if any of the selected Inspection Report generation fails. From this section, you can download the error log and the Inspection Reports that are successfully generated.
Procedure
Download Bulk Inspection Reports
Before You Begin
- Access the Report Configuration page and complete the configurations to store the generated reports.
- Make sure that a default report is configured in the Family Reports section of the family associated to the Inspection.