Calculations
Overview of TM Calculations
A Corrosion Analysis includes one or more assets and all the TM-specific records that are linked to them. As you conduct a Corrosion Analysis, various calculations and validations are performed, and the results are stored in various records involved in the Corrosion Analysis.
In this section of the documentation, we provide descriptions of the calculations and validations that are performed within a Corrosion Analysis. These descriptions are classified according to the type of record for which the calculation or validation is performed:
- Asset Corrosion Analysis: Stores summary information and calculations that are performed using the information in the related Thickness Measurement Location and Thickness Measurement records.
-
TML Corrosion Analysis: Stores summary information and calculations performed using the information in related Thickness Measurement Location and Thickness Measurement records.
-
Thickness Measurement: Stores measurement data and performs calculations. The values calculated in Thickness Measurement records are used for calculating values in the associated TML Corrosion Analysis record.
Thickness Monitoring uses specific formulas, equations, and estimation methods to arrive at the values that are stored in these records. In order to understand the information that is displayed to you for a given analysis, you must understand how the values were determined.
Measurement Calculations
Measurement data is stored in three fields in Thickness Measurements:
- Readings: Stores one or more values representing thickness measurement data collected at a specific TML.
- Uncorrected Measurement: Stores the unadjusted measurement value.
- Measurement Value: Stores the final, adjusted measurement value.
Measurement data is stored in three fields in Thickness Measurements:
- Readings: Stores one or more values representing thickness measurement data collected at a specific TML.
- Uncorrected Measurement: Stores the unadjusted measurement value.
- Measurement Value: Stores the final, adjusted measurement value.
Measurement data is recorded in these fields according to the following workflow:
- When a Thickness Measurement is created, you enter data into the Readings field.Note: Readings can be added by accessing the Thickness Measurement directly, using the Measurement Data Entry Workspace, or using a datalogger.
- A calculation is performed against the values in the Readings field, and the result is used to populate the Uncorrected Measurement field automatically.
- The Measurement Value field is populated automatically with the value in the Uncorrected Measurement field.Note: The Uncorrected Measurement field is meant to serve as an intermediate storage location between the Readings field and the Measurement Value field. In baseline Thickness Monitoring, the Measurement Value is simply populated with the value in the Uncorrected Measurement field. You can create custom rules to perform additional adjustment or correction calculations.
The type of calculation that is performed in step 2 is determined by the settings defined for measurement readings in the TM Admin Preferences. The baseline TM product offers three calculation options: Average, Minimum, and Maximum.
Consider a Thickness Measurement that contains the following values in the Readings field:
- 0.3
- 0.31
- 0.317
In this case:
-
Using the Average calculation method, the Uncorrected Measurement value would be calculated as the average of the three values in the Readings field, 0.309.
- Using the Minimum calculation method, the Uncorrected Measurement value would be set to 0.31.
- Using the Maximum calculation method, the Uncorrected Measurement value would be set to 0.317.
Datasheet Calculations
Asset Corrosion Analysis > Average Corrosion Rate
Asset Corrosion Analysis > Statistical Corrosion Rate
TML Corrosion Analysis/Corrosion Analysis Settings > Short Term Corrosion Rate
TML Corrosion Analysis > Factor Remaining Life Date
About Interpolation
Thickness Monitoring (TM) can determine which Allowable Stress value to use for calculating T-Min and Maximum Allowable Working Pressure by looking in the Piping Stress reference table or the PV Stress reference table and finding a record where the Material Specification, Material Grade, and Design Code match exactly the values in the Thickness Measurement Location (TML).
Details
Multiple records with varying temperatures and stress values may exist for a given combination of Material Specification, Material Grade, and Design Code values. So, after a match is found on Material Specification, Material Grade, and Design Code, Thickness Monitoring (TM) evaluates Design Temperature.
If the Design Temperature in the TML is an exact match to a temperature value in a Piping Stress or PV Stress record, TM will simply use the corresponding Allowable Stress value. For example, consider a TML that contains the following values:
- Material Specification = SA-216
- Material Grade = B
- Design Code = ASME B31.3
- Design Temperature = 100
Now, consider a Piping Stress record that contains the following values:
- Material Specification = SA-216
- Material Grade = B
- Design Code = ASME B31.3
- Design Temperature = 100
- Allowable Stress = 20000
In this case, the values in the TML are an exact match to the values in the Piping Stress record. Therefore, TM will use the Allowable Stress value of 20000 to calculate Maximum Allowable Working Pressure and T-Min.
If the Piping Stress or PV Stress reference table does not contain an exact match on the Design Temperature defined in the TML, TM will use one the following methods for determining Allowable Stress, depending upon whether or not the Application Settings specify that interpolation should be used:
-
If interpolation should not be used, TM will use the Allowable Stress value for the lower bound temperature value.
-
If interpolation should be used, TM will determine the interpolated stress value using the values that exist in the Piping Stress table.
When Interpolation Is Used
If TM cannot find an exact match in the Piping Stress or PV Stress reference table, and the Application Settings specify that interpolation should be used, TM will calculate the interpolated Allowable Stress value using the temperature and stress values that make up a range that includes the TML Design Temperature.
For example, consider a Piping Stress reference table that contains the following two records.
Field | Record #1 | Record #2 |
---|---|---|
Material Specification | SA-403 | SA-403 |
Material Grade | WP316 | WP316 |
Design Code | ASME B31.3 | ASME B31.3 |
Design Temperature | 100 | 200 |
Allowable Stress | 20000 | 18000 |
Now, consider a TML that contains the following values:
- Material Specification = SA-403
- Material Grade = WP316
- Design Code = ASME B31.3
- Design Temperature = 150
The TML Design Temperature falls within the range established by the two Piping Stress records in the table. Linear interpolation assumes that stress varies linearly as a function of temperature within the defined range. Using this assumption, the Allowable Stress at 150 degrees can be calculated using the following formula:
Sx = S1 - (T1 - Tx) / (T1 - T2) * (S1 - S2)
Where:
- Sx = Allowable Stress for the TML
- S1 = Allowable Stress at Lower Boundary
- S2 = Allowable Stress at Upper Boundary
- T1 = Temperature at Lower Boundary
- Tx = Temperature defined for TML
- T2 = Temperature at Upper Boundary
Given the values from our example, we calculate Sx as:
Sx = 20000 - ((100 - 150) / (100 - 200) * (20000 - 18000))
So:
Sx = 19000
This interpolated Allowable Stress value will then be used to populate the Allowable Stress field in the TML.
When Interpolation Is Not Used
If TM cannot find an exact match in the Piping Stress or PV Stress reference table, and the Application Settings specify that interpolation should not be used, TM will use an Allowable Stress value that corresponds to the lowest temperature value in the temperature range that includes the TML Design Temperature.
For example, consider a Piping Stress reference table that contains the following two records.
Field | Record #1 | Record #2 |
---|---|---|
Material Specification | SA-403 | SA-403 |
Material Grade | WP316 | WP316 |
Design Code | ASME B31.3 | ASME B31.3 |
Design Temperature | 100 | 200 |
Allowable Stress | 20000 | 18000 |
Now, consider a TML that contains the following values:
- Material Specification = SA-403
- Material Grade = WP316
- Design Code = ASME B31.3
- Design Temperature = 150
In this case, the Design Temperature in the TML is not an exact match to a Piping Stress record. The TML Design Temperature, however, does fall within the temperature range established by the two Piping Stress records in the table. So, in this case, TM will use the record that contains the most conservative (i.e., lowest) Allowable Stress value. Therefore, in this case, an Allowable Stress value of 18,000 will be used in the TML.
About the Calculated T-Min Formulas
- Creating custom rules in the Rules Library.
- Modifying Thickness Monitoring Rules Lookup records, or creating new ones to reference those rules in the T-Min Formula Rule or MAWP Formula Rule field, as appropriate.
T-Min Formulas
The following table lists the baseline T-Min formulas included in Thickness Monitoring (TM). The execution of the algorithms listed in this table are contingent on certain required fields in TMLs.
Algorithm | Description | Formula | Variables | T-Min Formula Rule |
---|---|---|---|---|
Piping B31.1 1995 | ASME Design Code Power Piping B31.1 |
T-Min, [unit of measure] = (Pi * Do) / 2 ((S * E) + (Pi * y))
|
| Rules Library\Meridium\Thickness Monitoring\T-Min Calculator\TMinCalculator\CalculateTMinASME B31 1 1995 |
Piping B31.3A 1995 | ASME Design Code Process Piping B31.3a | T-Min, [unit of measure] = ( Pi * Do ) / 2 ( ( S * E ) + ( Pi * y ) ) |
| Rules Library\Meridium\Thickness Monitoring\T-Min Calculator\TMinCalculator\CalculateTMinASME B31 3A 1995 |
Piping B31.3B 1995 | ASME Design Code Process Piping B31.3b | T-Min, [unit of measure] = ( Pi * Do ) / 2 * ( S * E ) |
| Rules Library\Meridium\Thickness Monitoring\T-Min Calculator\TMinCalculator\CalculateTMinASME B31 3B 1995 |
Piping B31.3C 1995 | ASME Design Code Process Piping B31.3c | T-Min, [units of measure] = ( Do / 2 ) * 1 - SQRT( ( S * E - Pi ) / ( S * E + Pi ) ) |
| Rules Library\Meridium\Thickness Monitoring\T-Min Calculator\TMinCalculator\CalculateTMinASME B31 3C 1995 |
Piping B31.3D 1995 | ASME Design Code Process Piping B31.3d | T-Min, [units of measure] = Pi * ( Do + 2 * C ) / 2 * ( ( S * E - Pi * ( 1 - y ) ) |
| Rules Library\Meridium\Thickness Monitoring\T-Min Calculator\TMinCalculator\CalculateTMinASME B31 3D 1995 |
Piping B31.4 1995 | ASME Design Code Pipeline Transportation Systems for Liquid Hydrocarbons and Other Liquids B31.4 | T-Min, [units of measure] = ( Pi * Do ) / ( 2 * S ) |
| Rules Library\Meridium\Thickness Monitoring\T-Min Calculator\TMinCalculator\CalculateTMinASME B31 4 1995 |
Piping B31.8 1995 | ASME Design Code Gas Transmission and Distribution Piping Systems B31.8 | T-Min, [units of length] = ( Pi * Do ) / ( 2 * Str * T * E * F ) |
Note: Yield Strength is a reference value from the Piping Stress table and is based on the following fields:
| Rules Library\Meridium\Thickness Monitoring\T-Min Calculator\TMinCalculator\CalculateTMinASME B31 8 1995 |
Pressure Vessel Conical Head Inside Diameter 1995 | T-Min for a conical head (inside diameter) | T-Min, [units of measure] = Pi * Di / ( 2 * cos( a ) * ( S * E - 0.6 * Pi ) ) |
| Rules Library\Meridium\Thickness Monitoring\T-Min Calculator\TMinCalculator\CalculateTMinConicalHeadInsideDiameter 1995 |
Pressure Vessel Conical Head Outside Diameter 1995 | T-Min for a conical head (outside diameter) | T-Min, [units of measure] = Pi * Do / ( 2 * cos( a ) * ( S * Jf + 0.4 * Pi ) ) |
| Rules Library\Meridium\Thickness Monitoring\T-Min Calculator\TMinCalculator\CalculateTMinConicalHeadOutsideDiameter 1995 |
Pressure Vessel Cylindrical Shell Inside Diameter 1995 | T-Min for a cylindrical shell (inside diameter) | T-Min, [units of measure] = Pi * Ri / ( S * E - 0.6 * Pi ) |
| Rules Library\Meridium\Thickness Monitoring\T-Min Calculator\TMinCalculator\CalculateTMinCylindricalShellInsideDiameter 1995 |
Pressure Vessel Cylindrical Shell Outside Diameter 1995 | T-Min for a cylindrical shell (outside diameter) | T-Min, [units of measure] = Pi * Ro / ( S * E + 0.4 * Pi ) |
| Rules Library\Meridium\Thickness Monitoring\T-Min Calculator\TMinCalculator\CalculateTMinCylindricalShellOutsideDiameter 1995 |
Pressure Vessel Shperical Shell Inside Diameter 1995 | T-Min for a spherical shell (inside diameter) | T-Min, [units of measure] = Pi * Ri / ( 2 * S * E - 0.2 * Pi ) |
| Rules Library\Meridium\Thickness Monitoring\T-Min Calculator\TMinCalculator\CalculateTMinSphericalShellInsideDiameter 1995 |
Pressure Vessel Spherical Shell Outside Diameter 1995 | T-Min for a spherical shell (outside diameter) | T-Min, [units of measure] = Pi * Ro / ( 2 * S * E + 0.8 * Pi ) |
| Rules Library\Meridium\Thickness Monitoring\T-Min Calculator\TMinCalculator\CalculateTMinSphericalShellOutsideDiameter 1995 |
Pressure Vessel Ellipsoidal Head Inside Diameter 1995 | T-Min for a ellipsoidal head (inside diameter) | T-Min, [units of measure] = Pi * Di / ( 2 * S * E - 0.2 * Pi ) |
| Rules Library\Meridium\Thickness Monitoring\T-Min Calculator\TMinCalculator\CalculateTMinEllipsoidalHeadInsideDiameter 1995 |
Pressure Vessel Ellipsoidal Head Outside Diameter 1995 | T-Min for a ellipsoidal head (outside diameter) | T-Min, [units of measure] = Pi * Do / ( 2 * S * E + 1.8 * Pi ) |
| Rules Library\Meridium\Thickness Monitoring\T-Min Calculator\TMinCalculator\CalculateTMinEllipsoidalHeadOutsideDiameter 1995 |
Pressure Vessel Torispherical Head Inside Dish Radius 1995 | T-Min for a torispherical head (inside dish radius) | T-Min, [units of measure] = ( Pi * L * ( ( 3 + SQRT( L / Ir ) ) / 4 ) ) / ( 2 * S * E - 0.2 * Pi ) |
| Rules Library\Meridium\Thickness Monitoring\T-Min Calculator\TMinCalculator\CalculateTMinTorisphericalHeadInsideDishRadius 1995 |
Pressure Vessel Torispherical Head Outside Dish Radius 1995 | T-Min for a torispherical head (outside dish radius) | T-Min, [units of measure] = ( Pi * Od * ( ( 3 + SQRT( Od / Ok ) ) / 4 ) ) / ( 2 * S * E + Pi * ( ( 3 + SQRT( Od / Ok ) ) / 4 - 0.2 ) ) |
| Rules Library\Meridium\Thickness Monitoring\T-Min Calculator\TMinCalculator\CalculateTMinTorisphericalHeadOutsideDishRadius 1995 |
Pressure Vessel Hemispherical Head Inside Diameter 1995 | T-Min for a hemispherical head (inside diameter) | T-Min, [units of measure] = Pi * Ri / ( 2 * S * E - 0.2 * Pi ) |
| Rules Library\Meridium\Thickness Monitoring\T-Min Calculator\TMinCalculator\CalculateTMinHemisphericalHeadInsideDiameter 1995 |
Pressure Vessel Hemispherical Head Outside Diameter 1995 | T-Min for a hemispherical head (outside diameter) | T-Min, [units of measure] = Pi * Ro / ( 2 * S * E + 0.8 * Pi ) |
| Rules Library\Meridium\Thickness Monitoring\T-Min Calculator\TMinCalculator\CalculateTMinHemisphericalHeadOutsideDiameter 1995 |
Pressure Vessel Toriconical Head Inside Diameter 1995 | T-Min for a toriconical head (inside diameter) | T-Min, [units of measure] = Pi * Di / ( 2 * cos( a ) * ( S * E - 0.6 * Pi ) ) |
|
Rules Library\Meridium\Thickness Monitoring\T-Min Calculator\TMinCalculator\CalculateTMinToriconicalHeadInsideDiameter 1995 |
Pressure Vessel Toriconical Head Outside Diameter 1995 | T-Min for a toriconical head (outside diameter) | T-Min, [units of measure] = Pi * Do / ( 2 * cos( a ) * ( S * E + 0.4 * Pi ) ) |
| Rules Library\Meridium\Thickness Monitoring\T-Min Calculator\TMinCalculator\CalculateTMinToriconicalHeadOutsideDiameter 1995 |
Pressure Vessel Toriconical Head Knuckle Inside Diameter 1995 | T-Min for a toriconical head knuckle (inside diameter) | T-Min, [units of measure] = ( Pi * ( Di / ( 2 * cos( a ) ) ) * ( ( 3 + SQRT( ( Di / ( 2 * cos( a ) ) / r ) ) / 4 ) ) ) / ( 2 * S * E - 0.2 * Pi ) |
| Rules Library\Meridium\Thickness Monitoring\T-Min Calculator\TMinCalculator\CalculateTMinToriconicalHeadKnuckleInsideDiameter 1995 |
Pressure Vessel Toriconical Head Knuckle Outside Diameter 1995 | T-Min for a toriconical head knuckle (outside diameter) | T-Min, [units of measure] = ( Pi * ( Di / ( 2 * cos( a ) ) ) * ( ( 3 + SQRT( ( Di / ( 2 * cos( a ) ) / r ) ) / 4 ) ) ) / ( 2 * S * E + Pi * ( ( 3 + SQRT( ( Di / ( 2 * cos( a ) ) / r ) ) / 4 ) - 0.2 ) ) |
| Rules Library\Meridium\Thickness Monitoring\T-Min Calculator\TMinCalculator\CalculateTMinToriconicalHeadKnuckleOutsideDiameter 1995 |
Pressure Vessel Pipe Nozzle Inside/Outside 1995 | T-Min for a pipe nozzle | T-Min, [units of measure] = Pi * Do / ( 2 * S * E ) |
| Rules Library\Meridium\Thickness Monitoring\T-Min Calculator\TMinCalculator\CalculateTMinPipeNozzle 1995 |
Tank Riveted Shell 1995 | T-Min for a riveted shell | T-Min, [units of measure] = 2.6 * D * G * ( H - 1 ) / ( Ds * E ) |
| Rules Library\Meridium\Thickness Monitoring\T-Min Calculator\TMinCalculator\CalculateTMinRivetedShell 1995 |
Tank Welded Shell 1995 | T-Min and Allowable Stress for a welded shell |
For this algorithm, Allowable Stress is also calculated. If the Course Number field is great than 2: S = Min( 0.88 * Y, 0.472 * Ts ) If the Course Number field is 1 or 2: S = Min( 0.80 * Y, 0.429 * Ts ) The T-Min formula is: T-Min, [units of measure] = ( 2.6 * D * G * ( H - 1 ) ) / ( S * E ) |
| Rules Library\Meridium\Thickness Monitoring\T-Min Calculator\TMinCalculator\CalculateTMinWeldedShell 1995 |
Tank Floor Plate 1995 | T-Min for floor plate |
If Pd or Pl = True, then: T-Min, [units of measure] = 0.05 If Pd and Pl = False, then: T-Min, [units of measure] = 0.10 |
| Rules Library\Meridium\Thickness Monitoring\T-Min Calculator\TMinCalculator\CalculateTMinFloorPlate 1995 |
Tank Annular Plate Ring 1995 | T-Min for an annular plate ring |
If Specific Gravity is less than 1: T-Min, [units of measure] = 2.34 * D * G * ( H - 1 ) / (Pt) If Specific Gravity is greater than or equal to 1: T-Min, [units of measure] = 2.6 * D * G * ( H - 1 ) / (Pt) |
| Rules Library\Meridium\Thickness Monitoring\T-Min Calculator\TMinCalculator\CalculateTMinAnnularPlateRing 1995 |
Piping B31.3A 1995
Thickness Monitoring determines which formula to use for the Calculated T-Min value by matching values in the TML to values in the Thickness Monitoring Rules Lookup reference table.
Now, consider a TML that contains values in the following required fields:
- Design Code: B31.3
- Code Year (T-Min Formula): 1995
- Piping Formula: A
Based upon the values in the TML:
-
The following function will be used to determine the Calculated T-Min value: Rules Library\Meridium\Thickness Monitoring\T-Min Calculator\TMinCalculator\CalculateTMinASME B31 3A 1995.
-
The following function will be used to calculate the Maximum Allowable Working Pressure: Rules Library\Meridium\Thickness Monitoring\MAWP\MAWPPiping\CalculateMAWP.
Reference Tables that are Used to Calculate Allowable Stress
The following table specifies the reference table that is used to retrieve or calculate the value in the Allowable Stress field in a TML record based on the value in the Component Type field.
Component Type | Reference Table |
---|---|
Piping | Piping Stress |
Pressure Vessel | PV Stress |
Tank | Tank Stress |
The following table provides the list of fields in each of the aforementioned reference tables, and specifies how the fields are mapped to the fields in the TML family. The values in these fields are used to calculate the value in the Allowable Stress field.
This field in the Piping, PV Stress, and Tank Stress reference table... | ...is mapped to this field in the TML family |
---|---|
Allowable Stress | Allowable Stress |
Code Year | Code Year (Allowable Stress Lookup) |
Design Code | Design Code |
Material Grade | Material Grade |
Material Specification | Material Specification |
Material Type | Material Type |
Metal Temperature | Design Temperature |
Minimum Tensile Strength | Minimum Tensile Strength |
Minimum Yield Strength | Minimum Yield Strength |
Maximum Allowable Working Pressure (MAWP) Calculation
Maximum Allowable Working Pressure is calculated for piping and pressure vessel assets and TMLs. Values in the Allowable Stress Reference Table are also used to calculate MAWP.
For assets, the MAWP is the most conservative value from all TMLs associated with the asset and is displayed in the Analysis Output section of the Analysis Overview page.
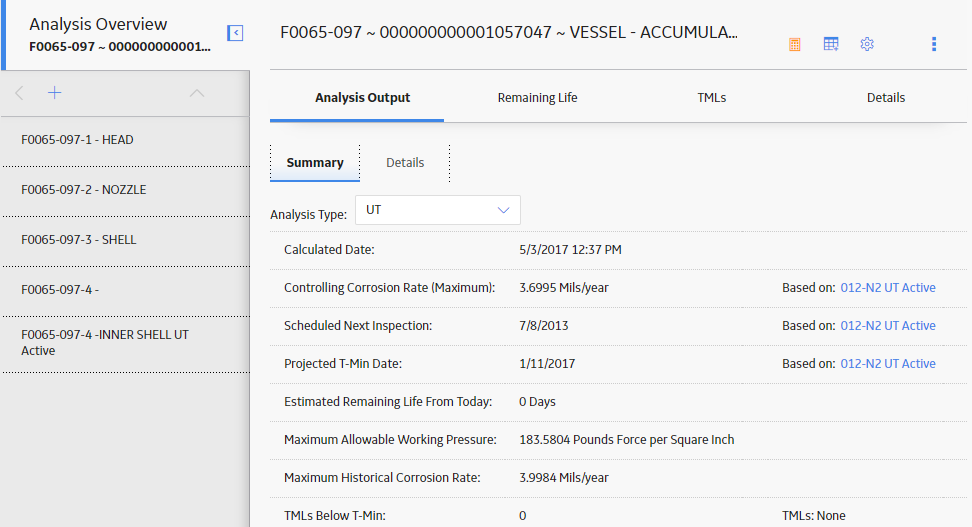
For TMLs, the MAWP is displayed on the Analysis Output section of the Analysis Overview page.
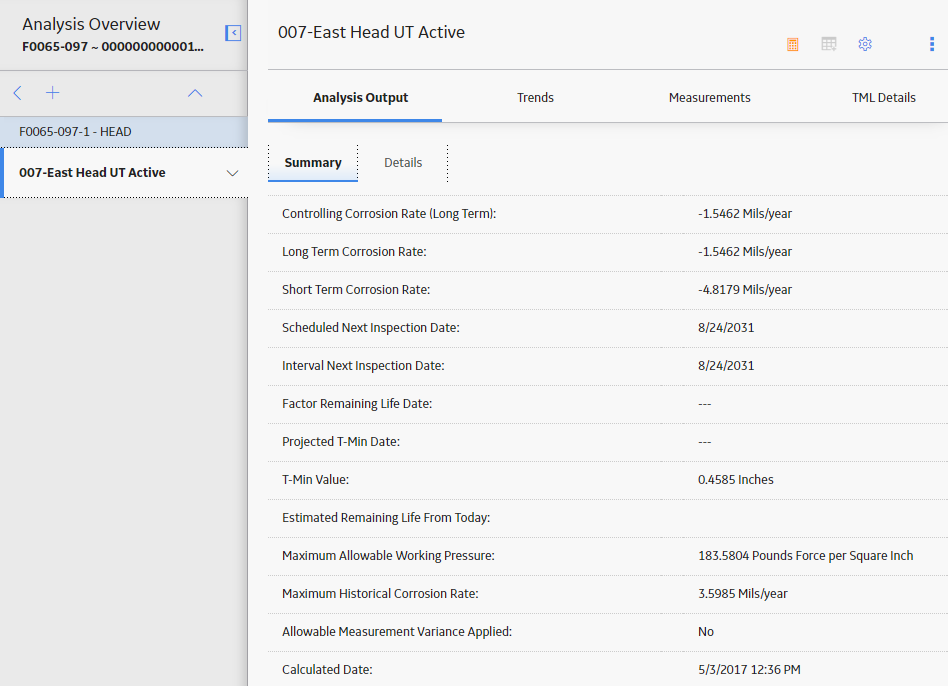
MAWP Requirements: Piping
The Piping MAWP can be calculated for the following design codes:
- B31.1
- B31.3
- B31.4
- B31.8
For the GE Digital APM system to calculate the MAWP for piping, the following values are required:
- In the Thickness Monitoring Location Record:
- Allowable Stress.
- Code Year.
-
Design Code.
- Joint Factor
-
Outside Diameter.
-
In the Thickness Measurement Record, the Last Measurement Value.
-or-
In the Thickness Monitoring Location Record, the Nominal Thickness.
-
In the TML Corrosion Analysis, the Controlling Corrosion Rate.
-or-
In the Corrosion Analysis Settings, Minimum Corrosion Rate
- A positive value for t-actual.
MAWP Requirements: Pressure Vessel
The pressure Vessel MAWP can be calculated only for TMLs whose design code is ASME VIII DIV 1 and whose Component Type or Vessel Type is Cylindrical Shell.
For the GE Digital APM system to calculate the MAWP for pressure vessels, the following values are required:
- In the Thickness Monitoring Location Record:
- Allowable Stress.
- Code Year.
- Design Code.
- Joint Factor.
- Inside Radius
-
In the Thickness Measurement Record, the Last Measurement Value.
-or-
In the Thickness Monitoring Location Record, the Nominal Thickness.
-
In the TML Corrosion Analysis, the Controlling Corrosion Rate.
-or-
In the Corrosion Analysis Settings, Minimum Corrosion Rate
- A positive value for t-actual.
MAWP Formula: Piping
The MAWP formula for Piping is calculated using the formula 2 S F t / D where:
MAWP (Pounds Force per Square Inch) = 2 * Allowable Stress * Joint Factor * t / Outside Diameter
...where:
- S = Allowable Stress (Pounds Force per Square Inch)
- F = Joint Factor
-
t = t-actual - 2(C-rate * I-interval)
...and:
- t-actual = The value in the Last Measurement field from the Measurement family in inches. If this value is not available, then the Nominal Thickness from the TML is used as the t-actual value.
- C-rate = The Controlling Corrosion Rate from the TML Corrosion Analysis in inches per year. If this value is not available, then the Minimum Corrosion Rate from the TML's Corrosion Analysis Settings is used for the C-rate value.
-
I-interval = The value in the Scheduled Next Date - Last Measurement Date field in years. If this value is not available, then the value in the Default Inspection Interval field from the TML's Corrosion Analysis Settings page is used for the I-interval value.
- D = Outside Diameter (inches)
MAWP Formula: Pressure Vessels
The MAWP formula for Pressure Vessels is calculated using the formula S F t / R + 0.6 t where:
MAWP (Pounds Force per Square Inch)= Allowable Stress * Joint Factor * t / Inside Radius + 0.6 * t
...where:
- S = Allowable Stress (Pounds Force per Square Inch)
- F = Joint Factor
-
t = t-actual - 2(C-rate * I-interval)
...and:
- t-actual = The value in the Last Measurement field from the Measurement family in inches. If this value is not available, then the Nominal Thickness from the TML is used as the t-actual value.
- C-rate = The Controlling Corrosion Rate from the TML Corrosion Analysis in inches per year. If this value is not available, then the Minimum Corrosion Rate from the TML's Corrosion Analysis Settings is used for the C-rate value.
- I-interval = The value in the Scheduled Next Date - Last Measurement Date field in years. If this value is not available, then the value in the Default Inspection Interval field from the TML's Corrosion Analysis Settings page is used for the I-interval value.
- R = Inside Radius (inches)
Example: Piping
Consider an example, where the following values are defined in the Thickness Measurement Location record:
- Allowable Stress = 16600 Pounds Force Per Square Inch
- Joint Factor = 1
- Nominal Thickness = 2.5 inches
- Last Measurement: 0.75 inches
- Controlling Corrosion Rate = 1.2 mils/year OR 0.0012 inches
- Schedule Next Date - Last Measure Taken Date = 0 years
- Outside Diameter = 10 inches
Based on these values, the Maximum Allowable Working Pressure is calculated as:
MAWP = 2 S F t / D;
...where:
- t = t-actual - 2 (C-rate * I interval)
- t = 0.75 - 2 (0.0012*0)
- t = 0.75
MAWP = 2 * 16600 * 1 * 0.75 / 10
MAWP = 2490 Pounds Force Per Square Inch
Example: Pressure Vessel
Consider an example, where the following values are defined in the Thickness Measurement Location record:
- Allowable Stress = 16600 Pounds Force Per Square Inch
- Joint Factor = 1
- Nominal Thickness = 2.5 inches
- Last Measurement: 0.75 inches
- Controlling Corrosion Rate = 1.2 mils/year OR 0.0012 inches
- Schedule Next Date - Last Measure Taken Date = 1 year
- Inside Radius = 10 inches
Based on these values, the Maximum Allowable Working Pressure is calculated as:
MAWP = 2 S F t /R+0.6t;
...where:
- t = t-actual - 2 (C-rate * I interval)
- t= 0.75 - 2 (0.0012*1)
- t = 0.7476
MAWP = 16600 * 1 * 0.7476/ 2+0.6*0.7476(12410/ =
MAWP = 5068.20 Pounds Force Per Square Inch
About Fields Required for Calculated T-Min
Thickness Monitoring (TM) provides a set of baseline formulas that can be used for determining the Calculated T-Min value. For these calculations to be successful, inputs are needed in certain fields. These inputs come from the TMLs for which the calculations are being performed. If the required fields are empty, TM will not be able to determine the Calculated T-Min value for a given TML.
The following section details fields that must be populated in TMLs in order for Calculated T-Min values to be returned using the baseline T-Min formulas. The lists of required fields are organized according to equipment type, which is derived using the value in the Design Code fields and other fields in each TML.
Piping T-Min Calculations
This section outlines the fields that are required for TM to determine the Calculated T-Min value for TMLs with the value B31.1, B31.1 A, B31.1 B, B31.1 C, B31.3 D, B31.4, or B31.8 in the Design Code field.
The following table lists additional fields that may be required based on the value in the Design Code and Piping Formula fields.
Design Code | Piping Formula | Design Factor | Joint Factor | Mechanical Allowance | Temperature Factor | Allowable Stress | Design Pressure | Outside Diameter | Yield Strength |
---|---|---|---|---|---|---|---|---|---|
B31.1 | N/A | N/A | Required | N/A | Required | Required | Required | Required | N/A |
B31.3 | A | N/A | Required | N/A | Required | Required | Required | Required | N/A |
B31.3 | B | N/A | Required | N/A | N/A | Required | Required | Required | N/A |
B31.3 | C | N/A | Required | N/A | N/A | Required | Required | Required | N/A |
B31.3 | D | N/A | Required | N/A | Required | Required | Required | Required | N/A |
B31.4 | N/A | N/A | N/A | N/A | N/A | Required | Required | Required | N/A |
B31.8 | N/A | Required | Required | N/A | Required | N/A | Required | Required | Required |
- Design Code
- Code Year (Allowable Stress Lookup)
- Material Specification
- Material Grade
Pressure Vessel T-Min Calculations
This section outlines the fields that are required for TM to determine the Calculated T-Min value for TMLs with the value ASME VIII DIV 1 in the Design Code field.
The following table is for TMLs with the value Inside in the PV Formula field. The table lists additional fields that may be required based on the value in the Vessel Type field.
Vessel Type | Apex Angle | Dish Radius | Inside Diameter | Inside Radius | Knuckle Radius |
---|---|---|---|---|---|
Conical Head | Required | N/A | Required | N/A | N/A |
Cylindrical Shell | N/A | N/A | N/A | Required | N/A |
Ellipsoidal Head | N/A | N/A | Required | N/A | N/A |
Hemispherical Head | N/A | N/A | N/A | Required | N/A |
Spherical Shell | N/A | N/A | N/A | Required | N/A |
Toriconical Head | Required | N/A | Required | N/A | N/A |
Toriconical Head, Knuckle Portion | Required | N/A | Required | N/A | Required |
Torispherical Head | N/A | Required | N/A | N/A | Required |
The following table is for TMLs with the value Outside in the PV Formula field. The table lists additional fields that may be required based on the value in the Vessel Type field.
Vessel Type | Apex Angle | Dish Radius | Outside Diameter | Outside Radius | Knuckle Radius |
---|---|---|---|---|---|
Conical Head | Required | N/A | Required | N/A | N/A |
Cylindrical Shell | N/A | N/A | N/A | Required | N/A |
Ellipsoidal Head | N/A | N/A | Required | N/A | N/A |
Hemispherical Head | N/A | N/A | N/A | Required | N/A |
Pipe Nozzle | N/A | N/A | Required | N/A | N/A |
Spherical Shell | N/A | N/A | N/A | Required | N/A |
Toriconical Head | Required | N/A | Required | N/A | N/A |
Toriconical Head, Knuckle Portion | Required | N/A | Required | N/A | Required |
Torispherical Head | N/A | Required | N/A | N/A | Required |
Tank T-Min Calculations
This section outlines the fields that are required for TM to determine the Calculated T-Min value for TMLs with the value API 653 in the Design Code field.
The following tables lists the required fields based on the value in the Tank Type field.
Tank Type | Required Fields |
---|---|
Annular Ring |
Note: GE Digital APM uses the values in the preceding fields to calculate the Allowable Stress value for this TML. The calculated value is then used to retrieve the appropriate T-Min value from the Tank T-Min Annular Ring reference table. |
Floor Plate |
Note: Because these are logical fields, they always contain a value (i.e., Yes or No). The Calculated T-Min value can be determined even if the check boxes in these fields are cleared. |
Riveted Shell |
Note: An Allowable Stress value of 21000 is always used for determining the Calculated T-Min value for this TML. If a value other than 21000 exists in the Allowable Stress field of these records, that value will be ignored, and 21000 will be used in its place. |
Roof Plate | No baseline formulas are provided to calculate the T-Min value for TMLs with the baseline value Roof Plate in the Tank Type field. |
Welded Shell |
|
Interpret the Calculation Details
Each section contains specific information about that TML and the calculation that was performed against it.
The Calculation Status dialog box is divided into the following sections for each TML:
TML : <TML ID>
...where <TML ID> is the TML ID of the TML whose calculation details you are viewing. This section displays the following information:
- By User: The User ID of the Security User who saved the current Minimum Thickness value.
- On Date: The date on which the current Minimum Thickness value was last saved.
- Proposed T-Min Value: The most conservative (i.e., highest) T-Min value, based on the User Defined, Calculated, Nominal, and Default T-Min values.
- Proposed Source: The source that determined the Proposed T-Min Value.
- Calculated T-Min Value: The value calculated by the T-Min Calculator.
Calculated T-Min Details
This section displays the following information:
- Formula Used: The location in the Rules Library where the formula that was used to calculate the Calculated T-Min value is stored.
Nominal T-Min value
- Nominal T-Min value: The Nominal T-Min value that was retrieved using the Piping Nominal T-Min reference table.
- Values used for the lookup: The fields in the TML that were used to retrieve the Nominal T-Min value.
Default T-Min value
This section displays the value that is stored in the Default T-Min field in the Corrosion Analysis Settings record that is linked to the TML.
User Defined T-Min value
This section displays the value specified in the User Defined box for the TML in the T-Min Calculator workspace.
Piping Nominal T-Min Reference Table
Records in the Piping Nominal T-Min family make up the Piping Nominal T-Min reference table, which Thickness Monitoring uses to locate the appropriate Nominal T-Min value for each Thickness Measurement Location (TML) when you calculate T-Min values. Since the baseline GE Digital APM product does not include any records in the Piping Nominal T-Min family, you must create these records manually using values from industry standards. After these records exist, when you calculate T-Min values, the GE Digital APM system will map values from fields in the TMLs to values in the corresponding fields in Piping Nominal T-Min records to find the associated Nominal T-Min value.
Details
The following table lists the default fields in the Piping Nominal T-Min family and the corresponding fields in the Thickness Measurement Location (TML). The table provides the full list of mappings for all fields in the Piping Nominal T-Min family. Each mapping with be used only if that field is selected to be used for Nominal T-Min retrieval according to the settings on the TM Admin Preferences page.
Piping Nominal T-Min Field | Corresponding Thickness Measurement Location Field |
---|---|
Design Code | Design Code |
Material Grade | Material Grade |
Material Specification | Material Specification |
Material Type | Material Type |
Nominal Pipe Diameter | Piping Nominal Diameter |
Nominal T-Min | None. Values from input fields are used to find the corresponding Nominal T-Min value, which is used to populate the Nominal T-Min cell in the T-Min Calculator workspace. |
Pipe Type | None. This field cannot be selected in the Fields for Nominal T-Min Lookup list on the TM Admin Preferences page and has no corresponding TML field. Therefore, it will never be used for looking up Nominal T-Min values. |
Piping Nominal Diameter
When you create a Thickness Measurement Location, the Piping section of the datasheet contains the fields in the Thickness Measurement Location family, that are used to determine the values in the Nominal Thickness and Outside Diameter fields.
The following table shows how the fields in the Pipe Properties reference table correspond to and interact with fields in the Thickness Measurement Location family.
This field in the Pipe Properties reference table... | ...corresponds to this field in the TML family | Comments |
---|---|---|
Nominal Diameter - DN | Piping Nominal Diameter - DN |
The value in this field is selected by the user or populated automatically. You are required to select a value for either the Nominal Diameter - DN or the Nominal Diameter - NPS field. Once either value has been specified, the other field is populated automatically by the Pipe Properties reference table DN data is considered a dimensionless designator, meaning that it does not have an assigned unit of measure and is determined by ASME specifications. |
Nominal Diameter - NPS | Piping Nominal Diameter - NPS |
The value in this field is selected by the user or populated automatically. You are required to select a value for either the Nominal Diameter - DN or the Nominal Diameter - NPS field. Once either value has been specified, the other field is populated automatically by the Pipe Properties reference table. NPS data is considered a dimensionless designator, meaning that it does not have an assigned unit of measure and is determined by ASME specifications. |
Nominal Wall Thickness | Nominal Thickness | The value in this field is populated by the Pipe Properties reference table. |
Outside Diameter | Outside Diameter | The value in this field is populated by the Pipe Properties reference table. |
Schedule | Schedule | The value in this field is selected by the user or populated automatically. |
Example: Populating Fields on the Thickness Measurement Location Datasheet
Suppose you that you are starting with a blank TML datasheet, and you select the following values in the Piping section:
- Piping Nominal Diameter -NPS field: 0.125. Based on this selection, the Piping Nominal Diameter - DN field is automatically looked up in the Pipe Properties reference table, and the field value is set to 6.
- Schedule field: 40(s).
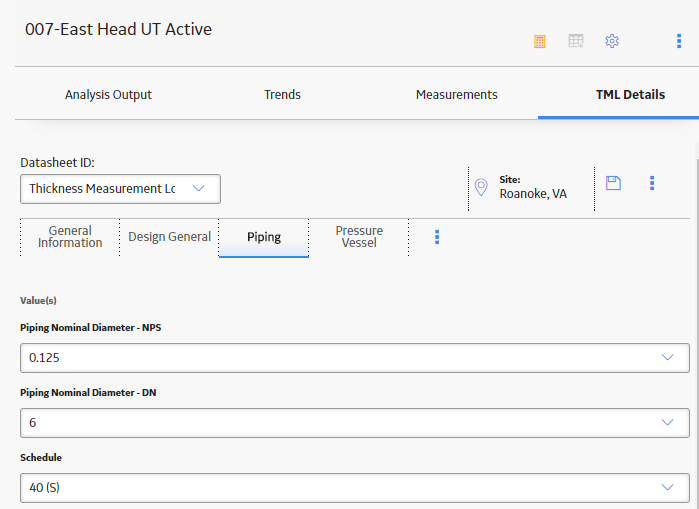
As a result, the following fields are populated automatically in the Design General section:
- Nominal Thickness field: 0.068 (inches).
- Outside Diameter field: 0.405 (inches).
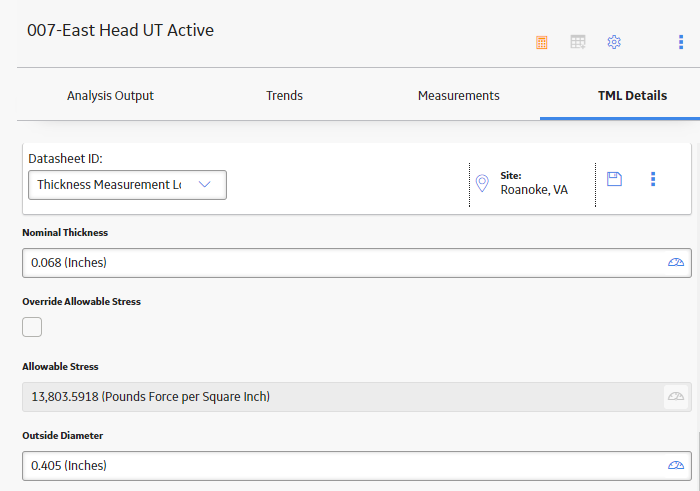
Tank T-Min Annular Ring Reference Table
Records in the Tank T-Min Annular Ring family make up the Tank T-Min Annular Ring reference table, which GE Digital APM uses to locate the appropriate Calculated T-Min value for each Thickness Measurement Location (TML) with the value API 653 in the Design Code field and Annular Ring in the Tank Type field.
The baseline GE Digital APM product does not include any records in the Tank T-Min Annular Ring family. For Calculated T-Min values to be determined, you must create Tank T-Min Annular Ring records using values from industry standards.
Details
The following table lists the default fields in the Tank T-Min Annular Ring family and the corresponding fields in the Thickness Measurement Location family.
Tank T-Min Annular Ring Field | Corresponding TML Field | Notes |
---|---|---|
Hydrostatic Test Stress Lower Bound | Allowable Stress | The Hydrostatic Test Stress Lower Bound field establishes the lower boundary of a stress range. An Allowable Stress value from a TML that falls within the established range is considered a match. |
Hydrostatic Test Stress Upper Bound | Allowable Stress | The Hydrostatic Test Stress Upper Bound field establishes the upper boundary of a stress range. An Allowable Stress value from a TML that falls within the established range is considered a match. |
Plate Thickness Lower Bound | Plate Thickness | The Plate Thickness Lower Bound field establishes the lower boundary of a plate thickness range. A Plate Thickness value from a TML that falls within the established range is considered a match. |
Plate Thickness Upper Bound | Plate Thickness | The Plate Thickness Upper Bound field establishes the upper boundary of a plate thickness range. A Plate Thickness value from a TML that falls within the established range is considered a match. |
T-Min | Minimum Thickness | The T-Min value that corresponds to the stress range and plate thickness range identified by the Allowable Stress and Plate Thickness values in the TML becomes the Calculated T-Min value for that record. This value can be used to populate the Minimum Thickness field in the TML, or a user-defined value can be specified instead. |
Reading Tolerance
The Reading Tolerance setting determines how much variation is allowed between values in the Readings field. When values are entered in the Readings field, they are averaged. Then, the Reading Tolerance value is used to determine which values fall within an acceptable range of the average value. If any of the values fall outside of the acceptable range, the value in the Readings Pass/Fail field is set to Fail.
- 0.3
- 0.31
- 0.36
The average of these three values is 0.3233. The GE Digital APM system evaluates each individual Reading value and determines whether it falls within 0.03 inches of the average value. If all the readings are within the range, then the measurement is set to Pass. If any or the reading is outside the range, then the measurement is set to Fail.
Reading Value | Reading Value Within the Range? | Pass/Fail Result |
---|---|---|
0.3 | Yes | Pass |
0.31 | Yes | Pass |
0.36 | No | Fail |
Since one of the readings failed the Reading Tolerance evaluation, the value in the Reading Pass/Fail field is set to Fail.