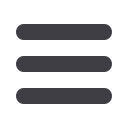
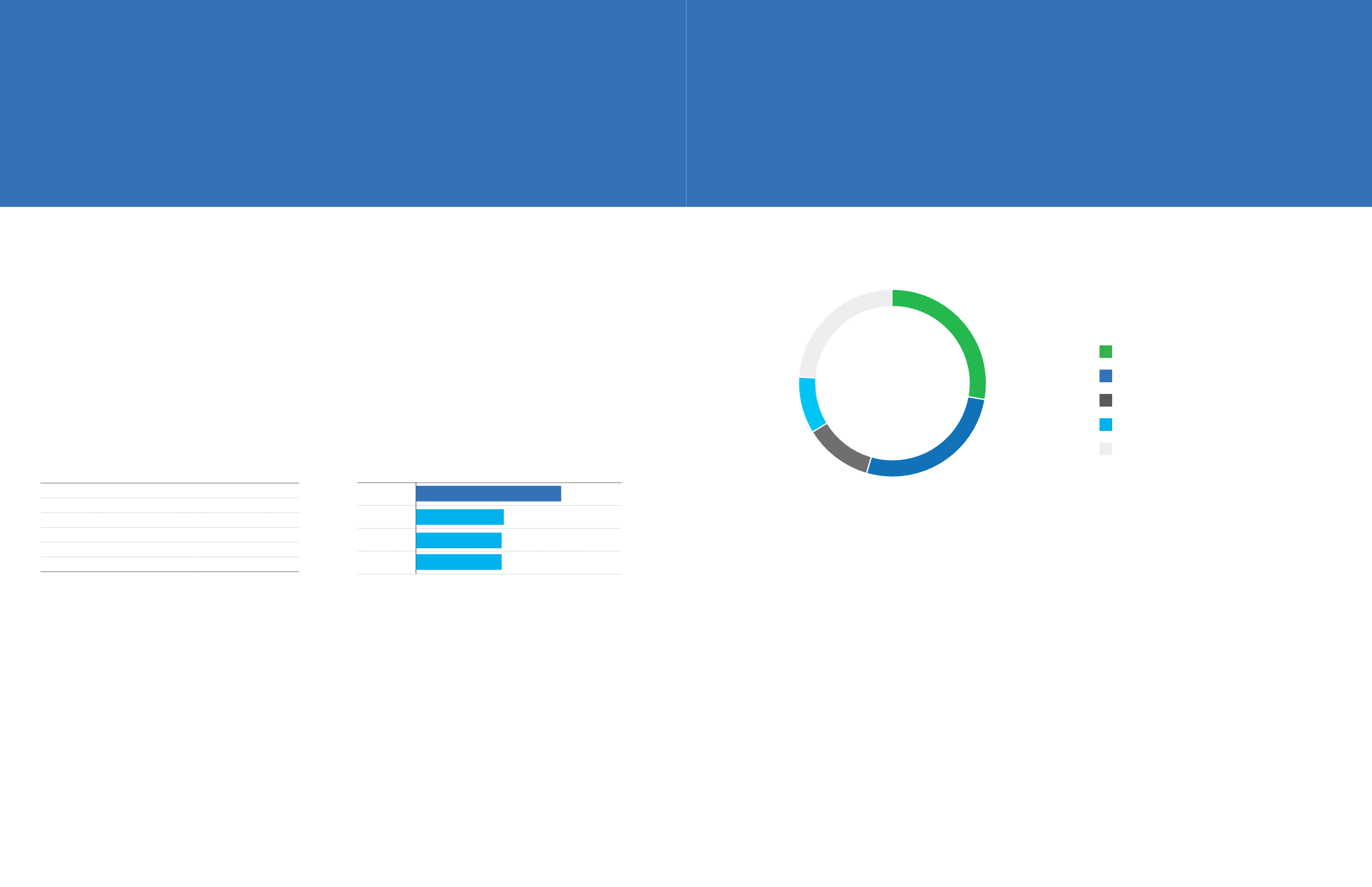
147
Industry Overview
MINING
GE helps customers achieve higher throughput and recovery
with lower maintenance and energy costs
Raw material and energy costs constitute a huge share in production costs. Yet capital expenditure budgets continue to fall while commodity prices are
increasingly under stress. To stay competitive, mining, metals and other heavy industry companies worldwide face many challenges today: reducing costs and
lead time; increasing operational efficiencies; deploying appropriate methods to extract and produce; and maintaining quality and reliability while simultaneously
complying with stringent environmental regulations. Large mines can cover an area of many square miles and require working in ever deeper and more remote
locations. These challenging environments demand increasingly large and more powerful equipment across the entire mining process. As the drive for power
and scale increases, the need for efficiency and reliability grows with it.
TOP 2015 BUSINESS IMPERATIVES FOR
MINING COMPANIES
RELATIONSHIP BETWEEN COMMODITY
PRICES AND MARKET CAPITALIZATION
FACTS & FIGURES
90% 6-12
15%
OF MACHINERY FAILURES
WERE PREDICTABLE THROUGH
MONITORING
MINING ENVIRONMENTS CAN
REDUCE MOTOR LIFE FROM AN
AVERAGE OF 5-10 YEARS DOWN
TO ONLY 6-12 MONTHS
IN THE U.S., IT IS ESTIMATED
THAT ENERGY USAGE ACCOUNTS
FOR MORE THAN 15% OF TOTAL
MINING PRODUCTION COSTS
BUSINESS IMPERATIVES FOR 2015
%
Cost management
36%
Productivity
24%
M&A
13%
Capital expenditures
13%
Financing
7%
Other
7%
Relationship between current commodity prices
and market cap
R
2
, 2000-13
Mining
Oil and gas
Flat steel
Pulp
0.86
0.50
0.49
0.49
148
Developments in Mining
RELIABILITY, SAFETY AND SUSTAINABILITY
Mining
Across the world, regional energy shortages have compelled some mines to sharply curtail their power consumption. In the U.S., it is estimated that energy usage
accounts for more than 15% of total mining production costs and that mines use 3% of all industrial energy. These realities have become part of a powerful set
of factors that, along with economic challenges, the accompanying fall in commodity prices, and the growing awareness of climate change is driving the mining
industry to become more energy-efficient and find cost-effective ways to perform their operations. Accordingly, the mining community is being challenged to
find electrical equipment and systems solutions that make mining operations: 1) reliable, efficient, and continuous; 2) safer and protected; and 3) sustainable.
Mining companies are looking at cutting costs by, among other things, using more efficient equipment to ease energy demand. That challenges mines to
maintain a delicate balance which maximizes productivity and quality and minimizes energy consumption and environmental impact. To get the best of both
of those worlds, mining operators need product suppliers to furnish them with the integrated process control systems that can make their plants more reliable
and efficient. They also need tools that tell them why downtime is occurring at the time of the outage so it can be prevented.
Mining is a physically hazardous business, and – since mining accidents hurt people, process continuity, production and the bottom line – it is not surprising that
ensuring workplace safety is a major concern of 71% of the Mincom survey respondents.
Mining processes typically impact land, water, and energy utilization. That’s why mining companies, like other good corporate citizens, have the desire and
obligation to contribute to the greater public good by limiting the effects of their operations upon people and natural resources. One way the industry can do this
is to cultivate renewable resource strategies that conserve—and preserve—the environment. As ever-more-stringent environmental regulations are enacted,
this approach becomes increasingly attractive.
FATALITIES BY ACCIDENT CLASS AT SURFACE MINING LOCATIONS (2009-2013)
20.4%
31.9%
23.9%
11.5%
12.4%
Powered haulage
Machinery
Falling, rolling or sliding rock or material
Slip or fall of person
All other