General Reference
TM Data Model
The following diagram illustrates how families are related within the TM data model. In the following image, boxes represent entity families, and arrows represent relationship families that are configured in the baseline database.
Data Model
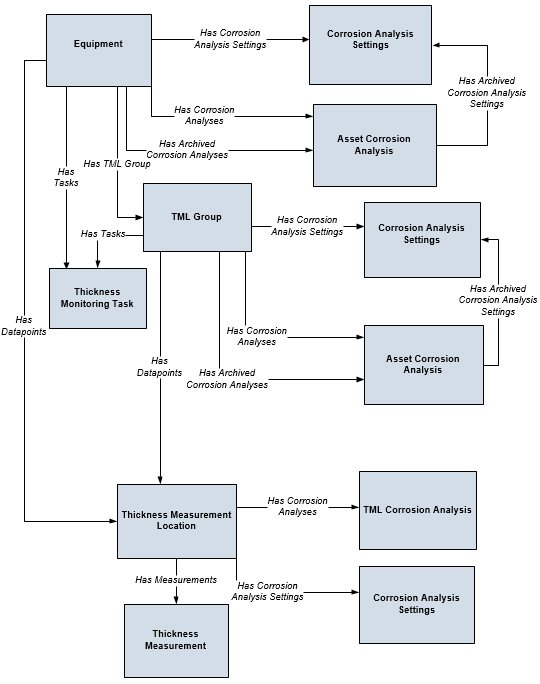
TM Security Groups
The following table lists the baseline Security Groups available for users within this module, as well as the baseline Roles to which those Security Groups are assigned.
Security Group | Roles |
---|---|
MI Thickness Monitoring Administrator |
MI Mechanical Integrity Administrator |
MI Thickness Monitoring Inspector |
MI Mechanical Integrity Administrator MI Mechanical Integrity Power MI Mechanical Integrity User |
MI Thickness Monitoring User |
MI Mechanical Integrity Administrator MI Mechanical Integrity Power MI Mechanical Integrity User |
MI Thickness Monitoring Viewer |
MI APM Viewer MI Mechanical Integrity Viewer |
The baseline family-level privileges that exist for these Security Groups are summarized in the following table.
Family | MI Thickness Monitoring Administrator | MI Thickness Monitoring Inspector | MI Thickness Monitoring User | MI Thickness Monitoring Viewer |
---|---|---|---|---|
Entity Families | ||||
Corrosion | View, Update, Insert | View, Update, Insert | View, Update, Insert | View |
Datapoint | View, Update, Insert | View, Update, Insert | View, Update, Insert | View |
Datapoint Measurement | View, Update, Insert, Delete | View, Update, Insert, Delete | View, Update, Insert | View |
Equipment | View | View | View | View |
Human Resource | View, Update, Insert, Delete | View | View | View |
Inspection Task | View | View, Update | View | View |
Inventory Group Configuration | View | View | View | View |
Materials of Construction | View | View | View | View |
Meridium Reference Tables | View, Update, Insert, Delete | View | View | View |
RBI Inspection Auto-Selection Criteria | View | View | View | View |
Resource Role | View, Update, Insert, Delete | View | View | View |
Security Group | View | View | View | View |
Security User | View | View | View | View |
Settings | View, Update, Insert | View, Update, Insert | View | View |
Task Execution | View, Insert | View, Insert | View | View |
Thickness Monitoring Task | View, Update, Insert, Delete | View, Update, Insert | View, Update, Insert | View |
TML Group | View, Update, Insert, Delete | View, Update, Insert, Delete | View | View |
Relationship Families | ||||
Belongs to a Unit | View, Update, Insert, Delete | View, Update, Insert | View, Update, Insert | View |
Equipment Has Equipment | View | View | View | View |
Group Assignment | View | View | View | View |
Has Archived Corrosion Analyses | View, Update, Insert, Delete | View, Update, Insert, Delete | View, Update, Insert, Delete | View |
Has Archived Corrosion Analysis Settings | View, Update, Insert, Delete | View, Update, Insert, Delete | View, Update, Insert, Delete | View |
Has Archived Subcomponent Analysis Settings | View, Update, Insert, Delete | View, Update, Insert, Delete | View, Update, Insert, Delete | View |
Has Archived Subcomponent Corrosion Analyses | View, Update, Insert, Delete | View, Update, Insert, Delete | View, Update, Insert, Delete | View |
Has Corrosion Analyses | View, Update, Insert, Delete | View, Update, Insert, Delete | View, Update, Insert, Delete | View |
Has Corrosion Analysis Settings | View, Update, Insert, Delete | View, Update, Insert, Delete | View, Update, Insert, Delete | View |
Has Datapoints | View, Update, Insert, Delete | View, Update, Insert, Delete | View, Update, Insert, Delete | View |
Has Inspections | None | None | None | View |
Has Measurements | View, Update, Insert, Delete | View, Update, Insert, Delete | View, Update, Insert, Delete | View |
Has Roles | View, Update, Insert, Delete | View | View | View |
Has Task Execution | View, Insert | View, Insert | View | View |
Has Task Revision | View, Insert | View, Insert | View | View |
Has Tasks | View, Insert | View, Insert | View, Insert | View |
Has TML Group | View, Update, Insert, Delete | View, Update, Insert, Delete | View | View |
Is a User | View | View | View | View |
User Assignment | View | View | View | View |
The following table lists the baseline Security Groups available for users within this module, as well as the baseline Roles to which those Security Groups are assigned.
Security Group | Roles |
---|---|
MI Thickness Monitoring Administrator |
MI Mechanical Integrity Administrator |
MI Thickness Monitoring Inspector |
MI Mechanical Integrity Administrator MI Mechanical Integrity Power MI Mechanical Integrity User |
MI Thickness Monitoring User |
MI Mechanical Integrity Administrator MI Mechanical Integrity Power MI Mechanical Integrity User |
MI Thickness Monitoring Viewer |
MI APM Viewer MI Mechanical Integrity Viewer |
The baseline family-level privileges that exist for these Security Groups are summarized in the following table.
Family | MI Thickness Monitoring Administrator | MI Thickness Monitoring Inspector | MI Thickness Monitoring User | MI Thickness Monitoring Viewer |
---|---|---|---|---|
Entity Families | ||||
Corrosion | View, Update, Insert | View, Update, Insert | View, Update, Insert | View |
Datapoint | View, Update, Insert | View, Update, Insert | View, Update, Insert | View |
Datapoint Measurement | View, Update, Insert, Delete | View, Update, Insert, Delete | View, Update, Insert | View |
Equipment | View | View | View | View |
Human Resource | View, Update, Insert, Delete | View | View | View |
Inspection Task | View | View, Update | View | View |
Inventory Group Configuration | View | View | View | View |
Materials of Construction | View | View | View | View |
Meridium Reference Tables | View, Update, Insert, Delete | View | View | View |
RBI Inspection Auto-Selection Criteria | View | View | View | View |
Resource Role | View, Update, Insert, Delete | View | View | View |
Security Group | View | View | View | View |
Security User | View | View | View | View |
Settings | View, Update, Insert | View, Update, Insert | View | View |
Task Execution | View, Insert | View, Insert | View | View |
Thickness Monitoring Task | View, Update, Insert, Delete | View, Update, Insert | View, Update, Insert | View |
TML Group | View, Update, Insert, Delete | View, Update, Insert, Delete | View | View |
Relationship Families | ||||
Belongs to a Unit | View, Update, Insert, Delete | View, Update, Insert | View, Update, Insert | View |
Equipment Has Equipment | View | View | View | View |
Group Assignment | View | View | View | View |
Has Archived Corrosion Analyses | View, Update, Insert, Delete | View, Update, Insert, Delete | View, Update, Insert, Delete | View |
Has Archived Corrosion Analysis Settings | View, Update, Insert, Delete | View, Update, Insert, Delete | View, Update, Insert, Delete | View |
Has Archived Subcomponent Analysis Settings | View, Update, Insert, Delete | View, Update, Insert, Delete | View, Update, Insert, Delete | View |
Has Archived Subcomponent Corrosion Analyses | View, Update, Insert, Delete | View, Update, Insert, Delete | View, Update, Insert, Delete | View |
Has Corrosion Analyses | View, Update, Insert, Delete | View, Update, Insert, Delete | View, Update, Insert, Delete | View |
Has Corrosion Analysis Settings | View, Update, Insert, Delete | View, Update, Insert, Delete | View, Update, Insert, Delete | View |
Has Datapoints | View, Update, Insert, Delete | View, Update, Insert, Delete | View, Update, Insert, Delete | View |
Has Inspections | None | None | None | View |
Has Measurements | View, Update, Insert, Delete | View, Update, Insert, Delete | View, Update, Insert, Delete | View |
Has Roles | View, Update, Insert, Delete | View | View | View |
Has Task Execution | View, Insert | View, Insert | View | View |
Has Task Revision | View, Insert | View, Insert | View | View |
Has Tasks | View, Insert | View, Insert | View, Insert | View |
Has TML Group | View, Update, Insert, Delete | View, Update, Insert, Delete | View | View |
Is a User | View | View | View | View |
User Assignment | View | View | View | View |
Field Mappings in the TMLs Grid
In the Analysis Overview workspace, the grid in the TMLs section displays values in the following fields:
Field | Family |
---|---|
TML ID | Thickness Measurement Location |
Minimum Thickness | Thickness Measurement Location |
Number of Readings | Thickness Measurement Location |
Corrosion Rate | TML Corrosion Analysis |
Factor Remaining Life Date | TML Corrosion Analysis |
Scheduled Next Inspection Date | TML Corrosion Analysis |
Projected T-min Date | TML Corrosion Analysis |
Last Measurement Value | TML Corrosion Analysis |
Last Measurement Date | TML Corrosion Analysis |
Near Measurement Value | TML Corrosion Analysis |
The values in the Remaining Life column are calculated based on the current date and the value in the Projected T-Min Date field in the TML Corrosion Analysis family. This value is displayed in years.
About Allowable Stress
This topic has been intentionally excluded from the GE Digital APM product documentation website. This topic is available to you via the product documentation that is provided within the GE Digital APM system.
About Color-Coding
Color-coding lets you see at a glance whether certain conditions exist for a given Thickness Measurement Location (TML) or Thickness Measurement. A color-coding category is assigned to each TML or Thickness Measurement based on the following criteria:
Category | Visual Cue | Criteria for a TML | Criteria for a Thickness Measurement |
---|---|---|---|
Below T-Min |
| The value in the Measurement Value field in the latest Thickness Measurement is less than the value in the Minimum Thickness field. | The value in the Measurement Value field is less than the value in the Minimum Thickness field in the associated TML. |
Overdue |
![]() | The value in the Scheduled Next Inspection Date or the Projected T-min Date field is earlier than the current date. | N/A |
High Loss |
![]() |
The decrease in the measurement value of the latest Thickness Measurement compared to that of the previous one is greater than or equal to a specified percentage. Note: The default value is 30 percent. You can, however, modify this value.
|
The decrease in the measurement value of the latest Thickness Measurement compared to that of the previous one is greater than or equal to a specified percentage. Note: The default value is 30 percent. You can, however, modify this value.
|
Growth |
![]() | The measurement value of the latest Thickness Measurement is greater than that of the previous one. | The measurement value of the latest Thickness Measurement is greater than that of the previous one. |
Normal |
![]() | The TML does not meet the criteria for any of the aforementioned categories. | The Thickness Measurement does not meet the criteria for any of the aforementioned categories. |
These categories appear at the top of the TMLs section in the Analysis Overview workspace. The number in parentheses next to each category indicates the number of records that meet the criteria for each category. The visual cue appears in each row in the list of TMLs and Thickness Measurements.
Even if a TML or a Thickness Measurement meets the criteria for more than one category, only one color-code is assigned to each record, based on the following priority:
- Below T-Min
- Overdue
- High Loss
- Growth
Example: Color-Coding
Suppose a TML contains the following field values:
- Minimum Thickness: 1.2 inches
- High Loss: 10 percent (as specified on the TM Admin Preferences page)
Suppose the TML contains the following Thickness Measurements.
Measurement ID | Measurement Value (inches) |
---|---|
TM-1 | 1.34 |
TM-2 | 1.20 |
The following table describes the color-coding category that will be applied to each Thickness Measurement.
Measurement ID | Color-Coding Category | Reason |
---|---|---|
TM-1 | Normal |
The Measurement Value does not meet the criteria for any other categories. |
TM-2 | High Loss |
The percentage of decrease between the latest Measurement Value (1.20 inches) and the previous one (1.34 inches) is greater than 10 percent. |
Suppose you have created two more Thickness Measurements with the following Measurement Values:
Measurement ID | Measurement Value (inches) |
---|---|
TM-3 | 1.01 |
TM-4 | 1.21 |
The following table describes the color-coding category that will be applied to each Thickness Measurement.
Measurement ID | Color-Coding Category | Reason |
---|---|---|
TM-1 | Normal |
The Measurement Value does not meet the criteria for any other categories. |
TM-2 | Normal |
Although the percentage of decrease in the Measurement Value (1.20 inches) from the previous one (1.34 inches) is greater than 10 percent, since this is no longer the latest Thickness Measurement, the category Normal is applied instead of High Loss. |
TM-3 | Below T-Min | The Measurement Value (1.01 inches) is less than Minimum Thickness (1.2 inches). |
TM-4 | Growth | The Measurement Value (1.21 inches) is greater than the previous one (1.01 inches). |
Suppose the current date is December 31, 2017, and the TML Corrosion Analysis associated with the TML contains the following field values:
- Scheduled Next Inspection Date: January 01, 2018
- Projected T-min Date: January 02, 2018
For the TML, color-coding category is applied based on the following logic:
- Below T-Min: The value in the Measurement Value field (1.21 inches) of the latest Thickness Measurement (TM-4) is greater than the value in the Minimum Thickness field (1.2 inches). Therefore, the category Below T-Min is not applied to the TML.
- Overdue: The Scheduled Next Inspection Date (January 01, 2018) and the Projected T-Min Date (January 02, 2018) are later than the current date ( December 31, 2017). Therefore, the category Overdue is not applied to the TML.
- High Loss: There is no decrease in the Measurement Value of the latest Thickness Measurement (1.21 inches) compared to that of the previous one (1.01 inches). Therefore, the category High Loss is not applied to the TML.
- Growth: The Measurement Value of the latest Thickness Measurement (1.21 inches) is greater than that of the previous one (1.01 inches). Therefore, the category Growth is applied to the TML.
About the Measurement Data Entry (MDE) Workspace
The Measurement Data Entry workspace is used for entering Thickness Measurement readings for multiple TMLs. It is divided into two areas: the common measurement data section, and the data entry grid.
Common Measurement Data
The common measurement data section appears at the top of the Measurement Data Entry workspace, and allows you to define values that will be distributed to cells in the corresponding columns for each Thickness Measurement Location (TML) listed in the data entry grid.
The Common Measurement Data section provides three boxes in which you can enter data:
- Measurement Taken Date
- Measurement Taken By
- Temperature
You can customize this section to make additional boxes available. Data entered in these boxes becomes the default value in the corresponding cell in each row.
Changes to the common measurement data section will not be applied to any rows in the data entry grid that already contain data.
Data Entry Grid
The data entry grid appears below the common measurement data section. The grid will be populated with one row for each TML linked to the record that you selected when accessing the Measurement Data Entry workspace.
By default, the grid is sorted in ascending order according to the value in the TML ID column.
Some TMLs will require you to enter multiple readings, as determined by the value in the Number of Readings field in a TML. You can enter multiple readings on the data entry grid by specifying the values separated by semi-colon or by selecting in the row corresponding to a TML. A measurement value will be determined based on the readings.
TM Folder
Graphs
The Catalog folder \\Public\Meridium\Modules\Thickness Monitoring\Graphs contains the following items.
Item Name | Behavior and Usage |
---|---|
Corrosion Rate Dist | This graph appears on the Thickness Monitoring Overview page, and is based on the Corrosion Distribution query. It displays the corrosion rates of assets with calculated Asset Corrosion Analyses, ordered from highest rate of corrosion to lowest. |
Remaining Life Less than 180 Months Graph | This graph appears on the Thickness Monitoring Overview page, and is based on the Remaining Life Less than 180 Months query. It displays the remaining life of assets with calculated Asset Corrosion Analyses, ordered from lowest remaining life to highest. |
Queries
The Catalog folder \\Public\Meridium\Modules\Thickness Monitoring\Queries contains the following items.
Item Name | Behavior and Usage |
---|---|
Assets Near or Past Retirement | Used on the Thickness Monitoring Overview workspace to return a list of all assets with Asset Corrosion Analyses that are within 5 years of or past the retirement date. The list is displayed when you select the Assets Near or Past Retirement Date tab. |
Assets with TM Tasks | Used on the Thickness Monitoring Overview workspace to return a list of all assets with Thickness Monitoring Tasks. The list is displayed in the TM Tasks box. |
AvailableTMTasks | Returns all Thickness Monitoring Tasks related to the supplied assets. |
Corrosion Distribution | Used to populate the data in the Corrosion Rate Distribution graph on the Thickness Monitoring Overview workspace. |
Degradation Rates Greater than Expected | Used to populate the list in the Degradation Distribution box on the Thickness Monitoring Overview workspace. |
Excessive Corrosion | Used on the Thickness Monitoring Overview workspace to return all assets with Asset Corrosion Analyses, and a Controlling Corrosion Rate greater than 20 Mils/year. The list is displayed when you select the Excessive Corrosion tab. |
Measurement Input Reference | Returns TMLs and additional reference data used for entering Thickness Measurements in the Measurement Data Entry workspace. |
Measurements Near or Less than T-Min | Used on the Thickness Monitoring Overview workspace to return all assets with measurements that fall within 10 Mils or less of T-Min. |
Remaining Life Less than 180 Months | Used to populate the data in the Remaining Life graph on the Thickness Monitoring Overview workspace. |
Thickness Inspections | Used on the Thickness Monitoring Overview workspace to return all assets with a Next Inspection Date, including past dates. This list is displayed when you select the Thickness Inspections tab. |
TM Assets | Used on the Thickness Monitoring Overview workspace to display a list of all assets with Thickness Monitoring data linked to the selected Functional Location. |
TM Assets Requiring a Calculation | Used on the Thickness Monitoring Overview workspace to display a list of all assets with Asset Corrosion Analyses that must be recalculated. This list is displayed when you select the Assets Requiring a Calculation Assets Requiring a Calculation tab. |
TM Overview Filter Parameters | None |
TML Groups for an Asset | Returns a list of all TML Groups linked to the selected asset. |
TMLs for an Asset | Returns a list of all TMLs linked to the selected asset or TML Group. |
TM Rules Lookup
Thickness Monitoring includes a set of baseline Thickness Monitoring Rules Lookup records and the associated Rules Library projects. You can use the baseline records as they are delivered, or you can modify them to suit your specific needs. Like all reference table records, Thickness Monitoring Rules Lookup records are best viewed through a query. You can manage Thickness Monitoring Rules Lookup records via the TM Admin Preferences page.
Thickness Monitoring Rules
The following table provides a list of the fields that exist in the Thickness Monitoring Rules Lookup family, descriptions of these fields, and information about any corresponding Thickness Measurement Location (TML) fields.
Field Name | Field Description | Corresponding TML Field |
---|---|---|
Asset Type | Contains a value that identifies the type of equipment to which a TML is linked. The value in this field determines which values are available in the Design Code field. For example, when Piping is selected in the Asset Type field, only piping design codes will appear in the Design Code field. | This field exists simply to facilitate the creation of new Thickness Monitoring Rules Lookup records by filtering values in the Design Code field. |
Code Year |
Contains a list of years associated with the selected Design Code. | Code Year (T-Min Formula) |
Design Code | Contains a list of design codes that are appropriate for the equipment type selected in the Asset Type field. |
Design Code |
Component Type | Contains a list of component types. |
Determined by the equipment type, which is derived from the value in the Design Type field, and can be any of the following fields:
|
Formula Classification | Contains a list of formula classifications. |
Determined by the equipment type, which is derived from the value in the Design Type field, and can be any of the following fields:
|
T-Min Formula Rule | Contains a reference to a project in the Rules Library. | This value is derived for each TML based on values in other fields. Although the derived value is not stored in the TML itself, it identifies the formula that will be used to determine the Calculated T-Min value for a TML. |
MAWP Formula Rule | Contains a reference to a project in the Rules Library. | This value is derived for each TML based upon values in other fields. Although the derived value is not stored in the TML itself, it is used to determine the Maximum Allowable Working Pressure value for a TML. |
Default Datalogger Settings
This following table provides a list of default settings for each datalogger. You must review them and modify if needed before sending or receiving data from a datalogger.
Datalogger | Connection Type | Baud Rate | COM Port | Datalogger Service Port |
---|---|---|---|---|
GE DMS Go | USB | N/A | N/A | 2014 |
GE DMS Go+ | USB | N/A | N/A | 2014 |
GE DMS2 | Serial | Per Device Setting | COM1 | 2014 |
Olympus (Panametrics) 37DL Plus Ultrasonic Thickness Gage | Serial | 1200 | COM1 | 2014 |
Olympus (Panametrics) 38DL Plus Ultrasonic Thickness Gage | USB | N/A | N/A | 2014 |
Limitations When Using Dataloggers
This topic provides a list of limitations when using each type of datalogger.
GE DMS Go and GE DMS Go+
- You must specify a directory in the File Directory box. Files will be sent to and received from the Meridium folder that is created in the specified directory.
-
The GE DMS Go and GE DMS Go+ devices use only the first 32 characters of the file name that is used to send data. If the file name is longer than 32 characters, a message appears, specifying the original item name and the truncated item name.
If multiple files are sent to the device, and the first 32 characters of the file names are the same, then a single file will be created on the device using the first 32 characters, which stores the data in all the files.
- The GE DMS Go and GE DMS Go+ devices use only the first 16 characters of the TML ID. If the TML ID is longer than 16 characters, a message appears, specifying that the TML ID will be truncated to 16 characters.Important: Because of the truncation, if duplicate TML IDs are created in the device, it collects data from both the locations. However, while receiving the data, it updates the data only for the first TML ID.
GE DMS2
-
The GE DMS2 device uses only the first 32 characters of the file name that is used to send data. If the file name is longer than 32 characters, a message appears, specifying the original item name and the truncated item name.
If multiple files are sent to the device, and the first 32 characters of the file names are the same, then a single file will be created on the device using the first 32 characters, which stores the data in all the files.
- The GE DMS2 device uses only the first 16 characters of the TML ID. If the TML ID is longer than 16 characters, a message appears, specifying that the TML ID will be truncated to 16 characters.Important: Because of the truncation, if duplicate TML IDs are created in the device, it collects data from both the locations. However, while receiving the data, it updates the data only for the first TML ID.
Olympus (Panametrics) 37DL Plus Ultrasonic Thickness Gage
- The Olympus (Panametrics) 37DL Plus Ultrasonic Thickness Gage does not accept Asset IDs containing lowercase characters.
Olympus (Panametrics) 38DL Plus Ultrasonic Thickness Gage
- The Olympus (Panametrics) 38DL Plus Ultrasonic Thickness Gage does not accept Asset IDs containing lowercase characters.
TM URLs
There is one URL route associated with Thickness Monitoring: tm. The following table describes the various paths that build on the route, and the elements that you can specify for each.
Element | Description | Accepted Value(s) | Notes |
---|---|---|---|
tm/unit: Opens the Thickness Monitoring Overview workspace. tm/unit/<UnitEntityKey>: Displays the selected unit on the Thickness Monitoring Overview workspace. | |||
<UnitEntityKey> | Specifies the Functional Location or Unit you want to view in TM. | Any Entity Key that corresponds to a Unit or Functional Location. | Required. |
tm/asset/<AssetEntityKey>: Displays the selected asset in the Analysis Overview workspace. tm/asset/<AssetEntityKey>/settings: Displays the selected asset in the Corrosion Analysis Settings workspace. tm/asset/<AssetEntityKey>/input: Displays the selected asset in the Measurement Data Entry workspace. | |||
<AssetEntityKey> | Specifies the asset you want to view in TM. | Any Entity Key that corresponds to an asset. | Required. |
tm/asset/<AssetEntityKey>/subcomponent/<TMLGroupEntityKey>: Displays the selected TML Group in the Analysis Overview workspace. tm/asset/<AssetEntityKey>/subcomponent/<TMLGroupEntityKey>/settings: Displays the selected TML Group in the Corrosion Analysis Settings workspace. tm/asset/<AssetEntityKey>/subcomponent/<TMLGroupEntityKey>/input: Displays the selected TML Group in the Measurement Data Entry workspace. | |||
<TMLGroupEntityKey> | Specifies a TML Group linked to an asset that you want to view in TM. | Any Entity Key that corresponds to a TML Group. | Required. |
tm/asset/<AssetEntityKey>/tml/<TMLEntityKey>: Displays the selected TML in the Analysis Overview workspace. tm/asset/<AssetEntityKey>/tml/<TMLEntityKey>/settings: Displays the selected TML in the Corrosion Analysis Settings workspace. | |||
<UnitEntityKey> | Specifies a TML linked to an asset that you want to view in TM. | Any Entity Key that corresponds to a TML. | Required. |
Example URLs
Example URL | Destination |
---|---|
tm/unit | The Thickness Monitoring Overview workspace. |
tm/unit/2305330 | The Thickness Monitoring Overview workspace for the specified unit. |
tm/asset/2509505 | The Analysis Overview workspace for the specified asset. |
tm/asset/2509505/settings | The Corrosion Analysis Settings workspace for the specified asset. |
tm/asset/2509505/input | The Measurement Data Entry workspace for the specified asset. |
tm/asset/2509505/subcomponent/3476094 | The Analysis Overview workspace for the TML Group with Entity Key 3476094, which is linked to the asset with Entity Key 2509505. |
tm/asset/2509505/subcomponent/3476094/settings | The Corrosion Analysis Settings workspace for the TML Group with Entity Key 3476094, which is linked to the asset with Entity Key 2509505. |
tm/asset/2509505/subcomponent/3476094/input | The Measurement Data Entry workspace for the TML Group with Entity Key 3476094, which is linked to the asset with Entity Key 2509505. |
tm/asset/2509505/tml/6225073 | The Analysis Overview workspace for the TML with Entity Key 6225073, which is linked to the asset with Entity Key 2509505. |
tm/asset/2509505/tml/6225073/settings | The Corrosion Analysis Settings workspace for the TML with Entity Key 6225073, which is linked to the asset with Entity Key 2509505. |
TM System Code Tables
The following table lists the System Code Tables used to support various functions throughout Thickness Monitoring.
Table ID | Table Description | Usage |
---|---|---|
CITP | Corrosion Inspection Type |
Populates the Corrosion Inspection Type field in Corrosion Analysis Settings. You can modify the System Codes in this System Code Table if you want to use custom TML Analysis Types. |
CRAM |
Corrosion Analysis Methods |
Unknown |
DPAC | Datapoint Access | Populates the Access field in TMLs. |
DPCN | Datapoint Condition | Unknown |
DPCR | Datapoint Corrosion Analysis Methods | Populates the Corrosion Rate Options in Corrosion Analysis Settings. |
DPIN | Datapoint Insulation | Unknown |
DPTP | Datapoint Type | Unknown |
DSCD | Design Code | Populates the Design Code list in TMLs. |
INST | Inspection Status Code | Unknown |
INSM | Inspection Interval Types | Unknown |
MI ASSET TYPE | Asset Type | Populates the Asset Type list in Thickness Monitoring Rules Lookup records. |
MI RESOURCE ROLE | List of user roles | Populates the Role list in Resource Role records. |
MI STATUS INDICATOR | TML Status Indicator | Populates the Status Indicator list in TMLs. |
PIPFMU | Pipe Formula | Populates the Formula Classification list in Thickness Monitoring Rules Lookup records. |
PVFMU | Pressure Vessel Formula | Populates the Formula Classification list in Thickness Monitoring Rules Lookup records. |
SLCR | Straight Line Corrosion Methods | Unknown |
T MIN CUSTOM EQUATIONS | T-Min Calculator Custom Equations | Unknown. |
STCR | Statistical Corrosion Methods | Unknown |
TNKT | Tank Type | Populates the Component Type list in Thickness Monitoring Rules Lookup records. |
VSTP | Vessel Type | Populates the Component Type list in Thickness Monitoring Rules Lookup records. |
Other standard System Code Tables, such as UOME, MATG, and MATL, are also used in Thickness Monitoring.
TM Site Filtering
All of the families included in the Thickness Monitoring module employ the GE Digital APM Site Control. This means that you can access or modify only the records in TM that are assigned to the same site to which you are assigned.
Example: Viewing TMLs
Consider an organization that has three sites, Site X, Site Y, and Site Z.
- TML A: Assigned to Site X
- TML B: Assigned to Site Y
- TML C: Assigned to Site Z
-
TML D: No site assigned (global record)
Note: A global record in TM only occurs if there was an error in the data load or if the site location was changed by a Super User. Global records are not recommended Best Practices in TM.
Scenario 1: User assigned to only Site X
When this user accesses the TMLs from an analysis, he or she will see:
- TML A
- TML D
Scenario 2: User assigned to both Site X and Site Y
When this user accesses the TMLs from an analysis, he or she will see:
- TML A
- TML B
- TML D
Scenario 3: Super User
When this user accesses the TMLs from an analysis he or she will see:
- TML A
- TML B
- TML C
- TML D