TURBO
An aerospace update from GE in India
Edition - 7
GE Aerospace partners Vistara and Boeing to create a new milestone in Indian aviation
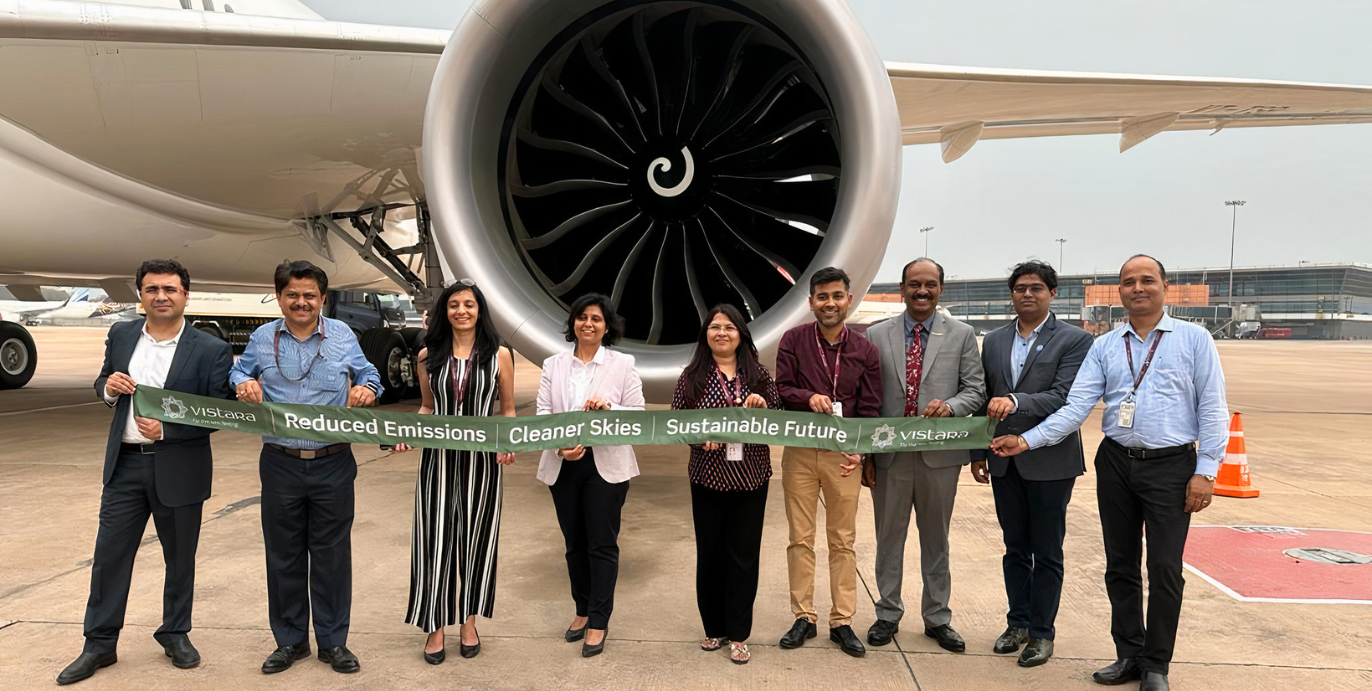
GE Aerospace’s GEnx engine recently powered the industry’s first wide-body aircraft on a long-haul route using Sustainable Aviation Fuel (SAF). The ferry flight from Charleston, South Carolina, in the United States, to New Delhi, India, used a blend of 30% SAF with conventional jet fuel.
“GE Aerospace is committed to helping our customers reduce emissions with advanced, more efficient propulsion technologies like the GEnx engine. Collaborations like this, that bring a long-haul flight using SAF for the first time to India, show what solutions are possible on a global scale towards the aviation industry’s net zero ambitions,” says Dave Kircher, General Manager of the GEnx Engine Program for GE Aerospace.
The GEnx engine is a high-thrust jet engine developed for the 787 Dreamliner and 747-8 airplane. Compared to its predecessor, the CF6, the GEnx engine is up to 15% more fuel efficient with up to 15% fewer CO2 emissions. Representing a giant leap forward in propulsion technology, GEnx uses lightweight, durable materials and advanced design processes to reduce weight, improve performance, and lower maintenance, making it the best engine choice for many long-haul flights.
GE Aerospace has been actively involved in assessing and qualifying SAF since 2007. It works closely with producers, regulators, and operators to help ensure SAF can be widely adopted for use in aviation.
“The GEnx engine, like all GE Aerospace engines, can operate on approved SAF blends today. Compatibility with existing aircraft engines is one of the reasons SAF is critical to helping the aviation industry reach its goal to be net zero by 2050 and collaborations like this encouraging greater adoption of SAF globally helps bring us closer to this target,” shares Vikram Rai, GE Aerospace’s Country Head for India & Indonesia.
Understanding SAF and why it matters
Sustainable Aviation Fuel (SAF) can be sourced from various feedstocks, like oils from plants, algae or greases but ends up being the same hydrocarbon kerosene that we know as jet fuel. Gurhan Andac, Engineering Technical Leader, Aviation Fuels and Additives, GE Aerospace, shares insights on SAF in a conversation with Craig Salvati, XLP Project Team Member, GE Aerospace.
Andac explains that the primary components of SAFs are hydrocarbons, the same element used in making conventional fuels. But SAF is derived from both synthetic sources and renewable resources, making it more environmentally friendly. It is made from plant oils, algae, fats, waste products, sugars, alcohols, greases, etc. It can be sourced sustainably, making it more aligned with environmental, social, and governance (ESG) goals. Using SAF will help restore ecological balance, avoid depletion of resources, and lower the industry’s carbon footprint.
Satish Prabhakaran and his team from GE Research are designing a high-tech ‘Suitcase’ for electric air travel

Satish Prabhakaran, a technology leader at GE Research in Schenectady, New York, heads a team that is taking on one of the toughest modern day engineering challenges: electric air travel.
With aviation accounting for about 2.5% of global CO2 emissions, hybrid electric propulsion technologies could do a lot to help bring the number down. Prabhakaran explains, “The hybrid system needs a robust and sophisticated power train to process the electricity produced by the airplane’s power plant — in this case, a gas turbine — which drives the craft’s propellers. Since altitudes of 35,000 feet impose limits on space and weight, this crucial electronic componentry needs to be compact and light, we’re actually aiming for the size of a suitcase.”
Prabhakaran has long been an expert miniaturist. He developed several cutting-edge magnetic components for mobile computing applications as part of his PhD. But they were too large and heavy to fit onto microprocessors. “In order to shrink the components, I had to learn material science and develop new clean-room processes,” he explains. He and his team are learning many new skill sets to shrink aircraft engine components for flight. But the components need to be more than just compact. They have to be safe, reliable, and top-of-class as the plane will have high voltages and carry people.
When Prabhakaran isn’t in the lab finding new ways to shrink components, he’s acting as a go-between for the technical and business teams at GE Research’s aviation-focused programs. He’s also an important ambassador for the hybrid electric program and regularly explains the research to businesses and government bodies helping to support the initiative.
The information contained herein is of a general nature and the publishers regret that they cannot accept liability for errors & omissions contained in this newsletter. Readers are advised to seek specialist advice before acting on the information contained which is of general use & may not be appropriate for the reader’s particular circumstances and/or situation. The views and opinions expressed herein are those of the authors/individuals and do not necessarily represent the views and opinions of GE. No part of this newsletter or any part of the contents may be reproduced, stored in a retrieval system or transmitted in any form without the permissions of the publishers in writing.