TURBO
An aerospace update from GE in India
Edition - 5
Join us at Aero India 2023 to explore GE engines changing the future of flight
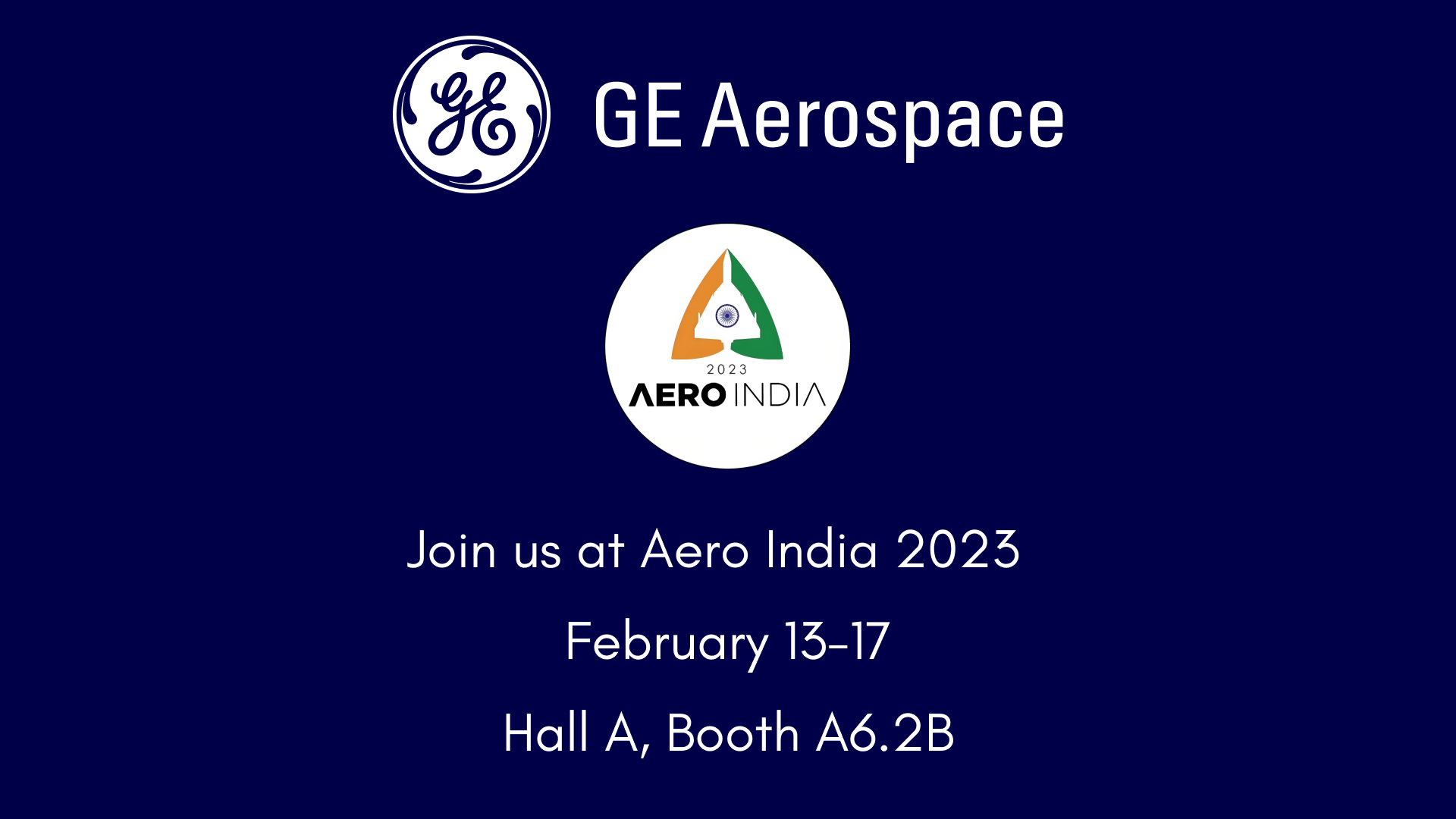
Be it LM2500, the versatile and fuel-efficient gas turbine, or the F414-GE-400 engine that provides up to 35% more thrust to combat-proven aircrafts, GE technology combines reliability, maintainability, and performance.
To know more about our proven and powerful technology, visit us at Booth A6.2B in Hall A, Aero India 2023 from February 13-17.
For updates from Aero India 2023, follow us on
The final delivery of the last 747 signals the dawn of a new era for GEnx
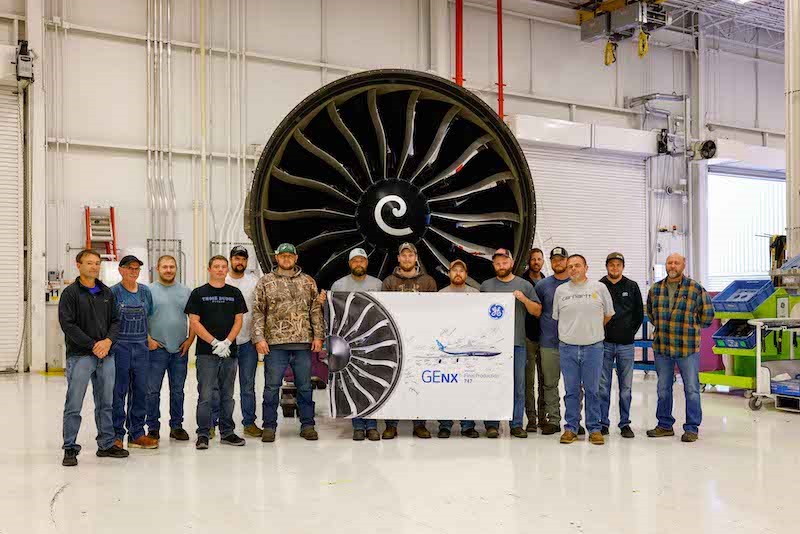
The last 747-8F freighter recently rolled out of the completion center at Boeing’s wide-body aircraft factory in Everett, Washington. It is powered by GEnx-2B engines which rolled off the line at GE Aerospace’s engine production and assembly facility in Durham, North Carolina.
Dave Kircher, who serves as the general manager of the GEnx product line, can’t help but think of all the people who worked on the program before him, going all the way back to 1974, when a CF6-powered 747 passenger plane took off for the first time. “I think of all these retired GE-ers that I know who worked on the CF6 engine to get the whole thing launched,” he says. “And now, nearly 50 years later, the last plane is going to be delivered. It’s a historic moment.”
“This product is just going to keep working for our customers,” Kircher says. “The 747 freighter is such an efficient airplane. It hauls a lot of volume, and with the nose opening you can get huge things inside of it. It’s going to keep flying for a long time.”
That’s the objective. And to achieve it, the GEnx team has a number of technical innovations on hand to improve engine performance and increase what’s known as “time on wing.” GE’s 360 Foam Wash, developed with the help of GE Research in Niskayuna, New York, cleans engines like the GEnx that over time can see a buildup of cement-like dust particles due to exposure to hot and harsh climates. By breaking down and removing the buildup, 360 Foam Wash can help improve engine compressor efficiency, reduce fuel consumption, lower CO2 emissions, and extend time between shop visits.
The information contained herein is of a general nature and the publishers regret that they cannot accept liability for errors & omissions contained in this newsletter. Readers are advised to seek specialist advice before acting on the information contained which is of general use & may not be appropriate for the reader’s particular circumstances and/or situation. The views and opinions expressed herein are those of the authors/individuals and do not necessarily represent the views and opinions of GE. No part of this newsletter or any part of the contents may be reproduced, stored in a retrieval system or transmitted in any form without the permissions of the publishers in writing.