Six to ten feet below the ground, 12-inch pipes carry natural gas all over America. They wind around electrical conduits and water mains. They bear the weight of daily commutes, delivery trucks, and city buses. And a lot of them are leaking. “Some of these pipes have been in the ground for over 100 years, and they’re only getting older,” says Alexander Duncan, a roboticist at GE Research. “Nobody really thought through how to service them. So it’s now a massive and costly problem for the national infrastructure.”
Duncan works on a multidisciplinary team that’s come up with a potential solution. They call it the PipeLine Underground Trenchless Overhaul system, or “PLUTO” for short. The goal: find a way to repair pipelines without digging huge trenches in the ground to remove and replace damaged pipe — an expensive and disruptive endeavor. The three- or six-legged robot instead crawls through the pipe itself and repairs it from the inside, drawing on GE coating technology used in jet engines. The device has potential to slash the cost of pipeline rehabilitation to as low as $200,000 to $500,000 per mile, from a range of $1 million to $10 million using traditional methods.
The robot is being developed as part of an initiative supported and led by the Advanced Research Project Agency for Energy (ARPA-E). Last week, the PLUTO pipe-building system was awarded a top industry honor as the “Emerging Technology of the Year” at the annual Underground Technologies Construction Conference in Orlando, Florida.
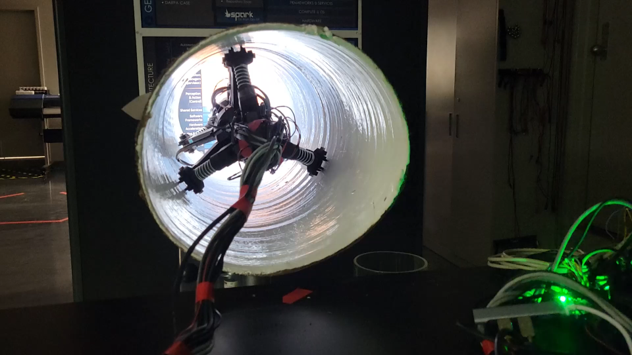
Leaky pipes are a well-known and extensive problem. Trillions of cubic feet of natural gas flow through millions of miles of pipeline throughout the U.S. Along the way, at more points than you can count, fugitive emissions leak methane, a powerful greenhouse gas, into the atmosphere. It’s not getting better. One study estimates that in local distribution pipelines alone there are more than 630,000 leaks.
Old pipes, often made from cast iron or steel, make up only about 3% of the pipes in the ground, yet they account for about 50% of the methane leaks, Duncan says. And because they’ve been built over and around so many times, they’re extremely hard to access. “You end up with a lot of these really interesting geometries and elbows that make it really hard to address more than a very small segment at a time,” Duncan explains. “The ones that are so cost prohibitive or just so technologically difficult to get into are the ones that are essentially being allowed to just continue to put off gas until a solution can be found.”
That’s where GE’s robot comes in.
Based on testing to date, just a small segment of pipe needs to be removed to get the “PLUTO” pipe building system in place. The modular robot rolls along the interior wall of a pipe, scanning with a light-detection sensing system and video to assess the state of the pipe and identify where it needs the most reinforcement. As it backs its way out, that’s when the real action starts. The Robot’s nose is an adjustable, spinning spray head that deposits a two-part epoxy along the pipe’s inner wall. The sprayed-in-place pipe (SIPP) establishes a tight seal with the existing pipe and hardens within four hours, quickly and effectively stopping the leak with minimal digging. As the legacy pipe continues to age and corrode, it can simply fall away, leaving the new epoxy pipe in its place.
The team drew from GE’s decades of experience applying protective coatings to jet engines and gas turbine components and worked with environmental engineering firm Garver, which has expertise in gas transmission. The epoxy material is manufactured by project partner Warren Environmental. The team expects to complete and test an industrial prototype of the robot this summer.
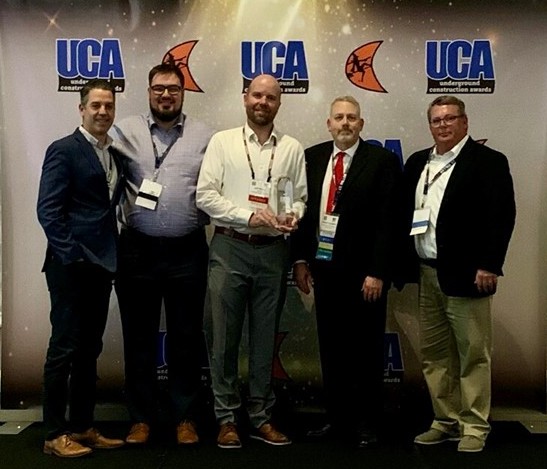
The robot was designed for both strength and versatility, finesse and brute force. Consisting of spidery, triangular-shaped pods, each just a couple of feet long, it can maneuver around elbow joints. Built-in suspension lets it ride smoothly over bumps and debris. With its trio of legs pressing outward and a strong motor, it maintains traction inside a pipe and can tow hundreds of feet of power cable and spray hoses weighing 1,800 pounds. “Our target is a city block,” Duncan says. The goal is to be able to access a pipeline at one intersection, then repair and reinforce the pipes going out in every direction from there.
“As long as we’re supplied with enough material,” says Duncan, “wherever the robot can go, we can repair.”