Rust never sleeps. Time is money. These two ancient adages drive a cycle of rejuvenation at GE Vernova’s remanufacturing facility in Noblejas, Spain, where wind industry operators from around the world seek renewal for their aging equipment. Here in this rural hamlet south of Madrid, GE Vernova’s Onshore Wind business started out small a decade ago, turning around a few dozen orders each year, mostly for its own benefit. By last year, however, volumes of equipment repaired in the site had risen more than 250%, according to Sergio Barroso, global remanufacturing leader at GE Vernova Onshore Wind. And more recently, a 2021 expansion increased the facility’s floor space from 9,000 to 14,000 square meters (97,000 to 150,000 square feet). All of this growth was driven not only by the overall expansion of global wind power, but by Noblejas’ ability to refurbish and ship out everything from driveshafts to gearboxes manufactured by GE Vernova and other original equipment manufacturers (OEMs), such as Siemens and Vestas. The goal shared by everyone is clear and simple: Keep downtime to a minimum, so the global wind fleet can keep spinning.
“Customers tell us we make their life easier, since Noblejas serves as their one-stop service shop for gearboxes, generators, and transformers. And it services their other broad OEM equipment as well,” says Jennifer Slatter, EMEA services sales leader at GE Vernova Onshore Wind. The center keeps a diverse and efficient store of inventory — the value to customers being parts on demand. And now that Noblejas is a much higher-throughput operation, keeping it that way requires a kind of dance around that inventory. Barroso explains that customers welcome immediate shipping of remanufactured replacement parts well before they ship their old stock to Spain. They only need to pick up the phone and they can have their order in as little as two weeks. “We support them with ready-to-share units, as they require,” he says.
But customers must play their part in this orchestrated dance as well, by committing to ship their worn-out gear within a fixed, limited period. If customers already have a replacement unit in their stock, they can also send Noblejas their worn-out component and the shop will provide them with remanufacturing services, not unlike when someone takes their car in to a repair shop. The center specializes in land-based turbines ranging from 1.5 megawatts (MW) up to 5 MW.
The inventory dance is also informed by statistical modeling, which uses a statistically driven mixed pull model based on lean methodology to predict a plausible breakdown rate for each coming year. The Onshore Wind business maintains a database of its global fleet of turbines, all of varying ages, which also logs hours of running time. Some turbines are young; others are old. “So what we do is predict demand for the next 12 months,” says Barroso, and that helps the repair center manage the longer lead time to remanufacture something like a gearbox, which can take 10 to 12 weeks. “We use that statistical model to purchase parts, bearings, gears, castings, forgings, spacers, pipes, and so on,” he says. “After all, downtime costs money.”
Noblejas thus sits at the center of a global support system for the wind industry, where orders come from as far away as South America. Yes, that’s a long way to go, but the expertise and capability mean it’s worth it. Barroso says it’s the aim of GE Vernova to make sure a customer’s investment in refurbished equipment makes a healthy, solid return by working reliably. Or like new. Indeed, the Noblejas remanufacturing process goes beyond mere repair, upgrading old stock with as much new engineering as possible. “We bring a lot of new advances in bearings to each job, for example, so when that turbine is back at home, up and running, it is expected to last longer, it is expected to perform better.” A constant, friendly dialogue with customers also keeps a healthy feedback loop rolling forward so that evolving improvements are captured and put into practice.
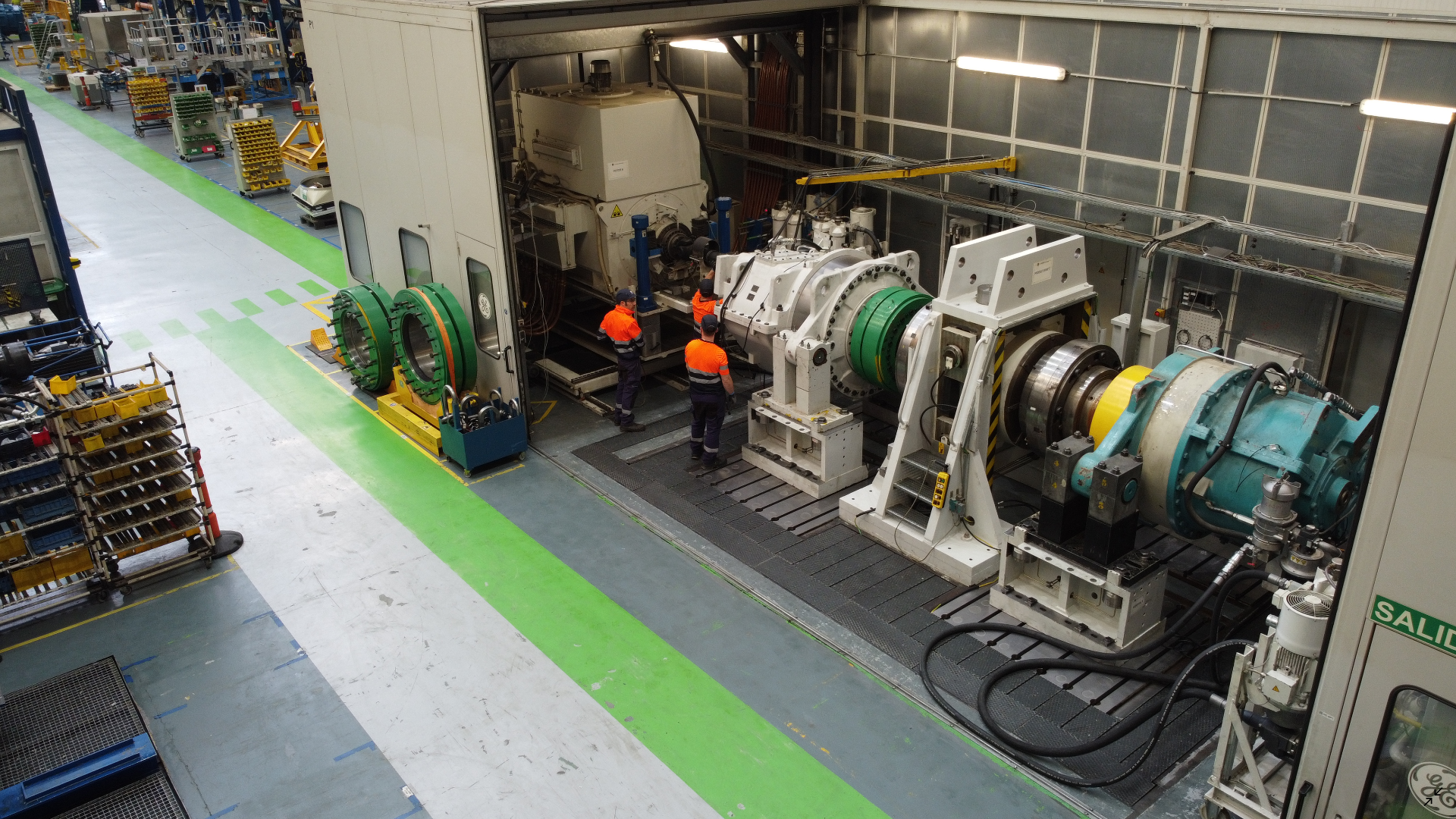
When customers do get a chance to visit the center, “their first words are usually ‘Wow!’” says Slatter. “Noblejas is organized with lean and clean assembly lines and state-of-the-art equipment. It utilizes advanced technology washing machines, measuring equipment, kinematic simulation software, re-grinding equipment, and grand test stands,” she adds.
The work being done in Noblejas is part of GE Vernova’s broader focus on building a more sustainable electric power system. As part of its recently launched sustainability framework, the “conserve” pillar emphasizes the company’s commitment to innovate more while using less, safeguarding natural resources through its 4Rs circularity approach (rethink, reduce, reuse, and recycle). As a prime example of “reuse,” Noblejas’ remanufacturing prowess aims to be a key lever to extend material durability and contribute to sustainability and carbon footprint reduction, while seeking to optimize wind farms’ operational costs and curbing the demand for more steel. Steel (along with cement) is one of the most carbon-intensive materials, and Barroso estimates that last year 4,500 metric tons of new steel demand was avoided by the center’s rejuvenation of old stock. “So in terms of sustainability and the circular economy, we play an interesting role.”
The GE Vernova team sees tremendous opportunity ahead in global wind power, with its installed base expected to grow by 15% on average every year. That anticipated growth is expected to expand the use of repair facilities, as the world needs to keep all the old turbines running in the field while adding new turbines to the total fleet. Because the fuel is free-flowing, time is money. And rust never sleeps.