In January, GE Vernova announced that it will invest nearly $600 million in its U.S. manufacturing facilities over the next two years to expand capacity to meet increasing energy demands — relying on an especially dynamic group of engineers: the executive site leaders steering operations at GE Vernova’s more than 115 manufacturing facilities. These experts bring an engineer’s skills in innovation and problem-solving to the giant, complex, and human-powered mechanism that is a manufacturing plant.
In celebration of National Engineers Week — whose 2025 theme is “Design Your Future” — we sat down with leaders at three GE Vernova plants. Here they share their insights and experiences at these key locations in the company’s growing energy business network, where increased capacity brings new opportunities for engineers like them to excel day in and day out.
Jason Reagan: Moving Around and Learning
More than half of the $300 million GE Vernova is investing in its Gas Power business will go to South Carolina’s Greenville gas turbine facility, to help meet a global surge in demand for electricity equipment, add an estimated 650 new jobs, and push someone like Jason Reagan to the very top of his game. Reagan is the executive plant manager for the Greenville Gas Power Manufacturing site. “The capacity ramp we’re preparing for is something we haven’t seen in the last 20 or 25 years,” he says. “So we’ve got to prepare not only this factory, but our business, really quickly. This requires super creative thinking and problem-solving, to transform this shop much more quickly than most people would have expected.” It’s the kind of challenge that drew Reagan to operations in the first place.
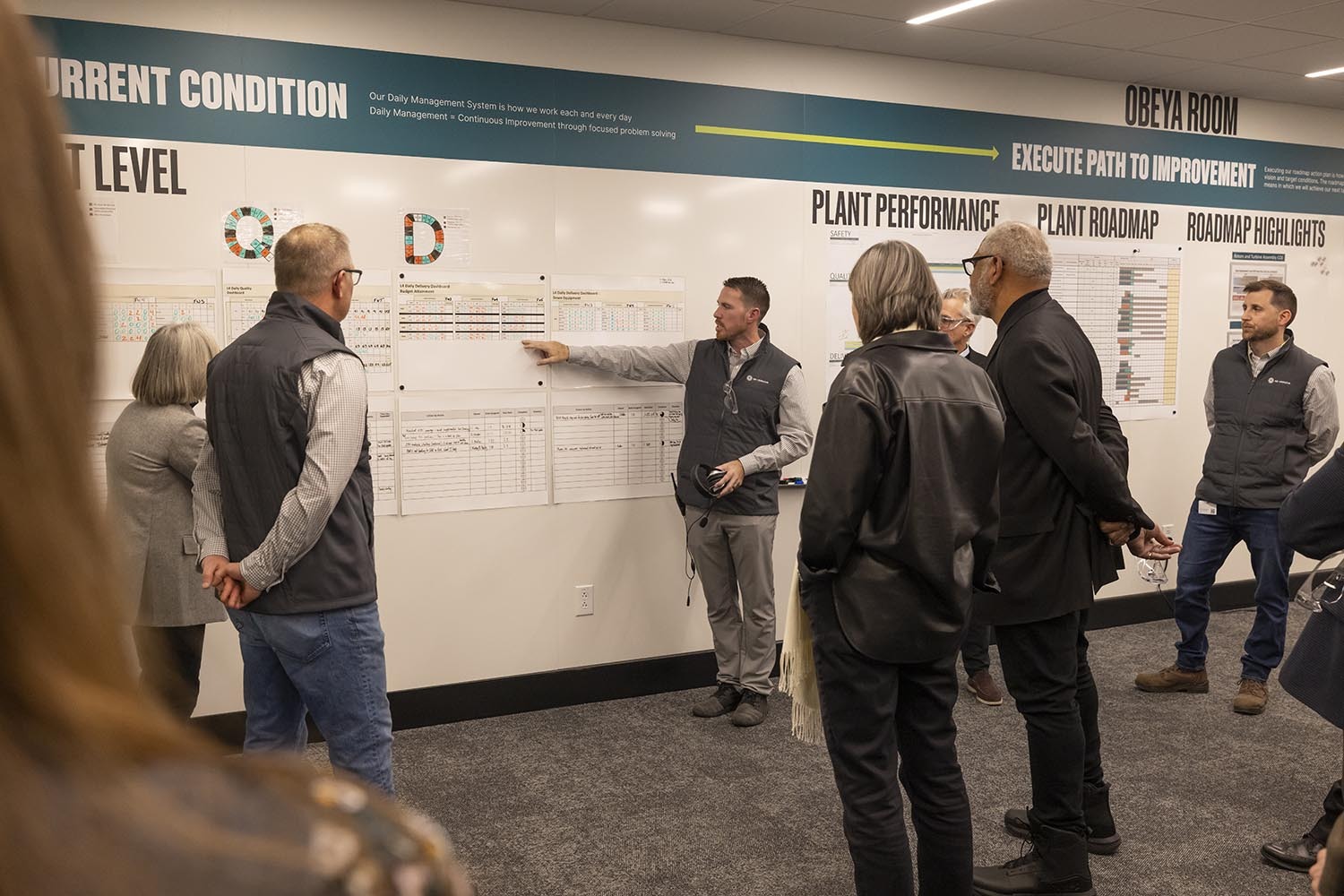
“I studied aerospace engineering in college but realized I didn’t want a standard design engineering path,” Reagan explains. “I was more hands-on oriented. I wanted to move around and learn more.” During his two-year tenure with the Operations Management Leadership Program (OMLP), he gained work experience in Virginia, South Carolina, Texas, and New York. At each stop, Reagan says, “I learned different technologies, and I was working with some of the smartest people in the world. There’s no other company in the world that can execute what we can, and with a company this size, there are always new opportunities that challenge me.”
In operations, these come every day. “We do have a general structure,” says Reagan, who employs lean manufacturing principles throughout the day. “Using lean tools such as daily management allows us to get a health status of all 1.5 million square feet of the factory in a short time period each morning. This ensures that we focus on the top safety, quality, and delivery challenges that could stop us from winning the day.”
Keeping the plant moving through a host of unplanned but inescapable hiccups requires all the engineering skills that Reagan has. “They’re all really centered around problem-solving,” he says. “That’s paramount in what we do every day to make the operation successful and help the team reach its potential. And as things ramp up, it only gets more exciting.”
Brandy McGraw: Pride in Community
Brandy McGraw is the executive site leader at GE Vernova’s Pensacola, Florida, facility, a location that manufactures wind turbine components and is one of four wind-power plants in which GE Vernova is investing a total of nearly $100 million. Helming this plant at such a moment is “the culmination of every experience I’ve had,” she says, “in terms of quality, materials, safety, leadership, development, cost control, innovation.” And it’s a much richer experience than anything McGraw imagined would come from her degrees in chemical engineering and industrial systems before she discovered broader vistas through the OMLP. “Right away, I really liked the culture of GE Vernova,” she says. “You can take on as big a challenge as you want. Get involved in a whole range of areas and try out different leadership opportunities.”
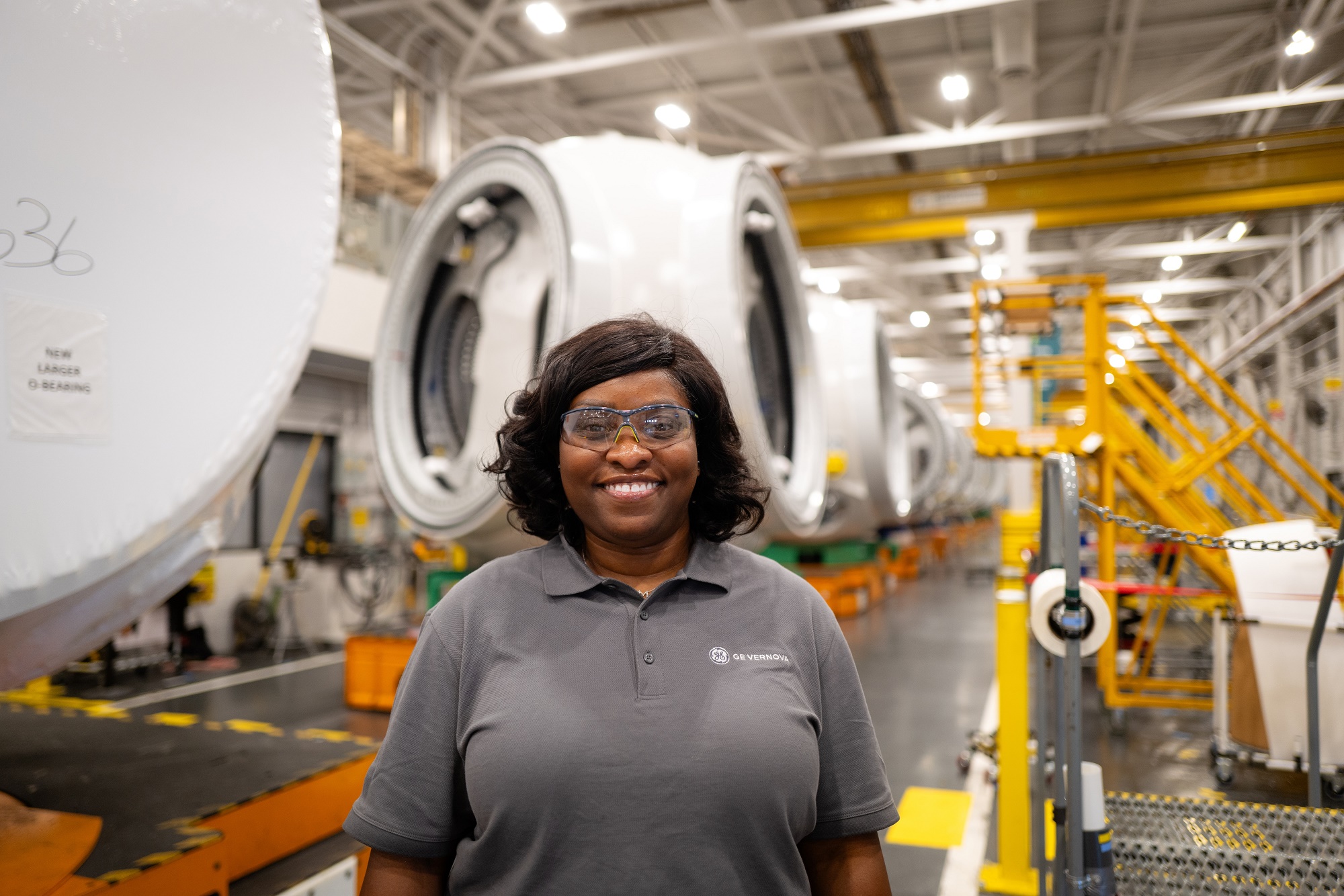
Now that she’s in a key leadership position, McGraw focuses on key business priorities — safety, quality, delivery, and cost — directing her problem-solving skills to improvements in the process. “My broader team is global, so we meet very early in the morning and then I head into the shop,” she says. After a genba walk — the lean term for a grounding walk through the entire site — McGraw drills down into any issues it might have raised. “I’ll get into the details of a problem or a challenge that we’re facing or an area where we’re implementing some proactive change,” she explains. Whenever possible, she encourages collaboration with the plant manufacturing engineers and design engineers. “When you bring those two engineering brain types together early in the process,” she says, “you can foresee potential manufacturing problems instead of working through trial and error.”
McGraw has also developed strong bonds with the community of Pensacola, working on a talent pipeline with a local university, collaborating with local officials on logistics, and seeing the appreciation the city has for GE Vernova. “We’re in a relatively small area with a small manufacturing footprint,” she says, “so the community is extremely proud to have us here, and really hopeful about what GE Vernova’s continued investment brings.” The journey to her leadership role helped strengthen her sense of mission to serve as a positive steward of her team, her community, and the GE Vernova mission to electrify and decarbonize the globe. “When you move around a lot and connect with people, you recognize that no matter what city, country, or continent you’re on, everybody wants the same things: to know they’re safe, that they can take care of their family, and that there’s a positive future.”
Benjamin Acevedo: Quickly Creating Connections
Benjamin Acevedo manages GE Vernova’s Grid Solutions plant in Clearwater, Florida, which produces capacitors and instrument transformers and is one of two plants where GE Vernova is investing a combined $20 million to meet rising global demand for high-voltage grid equipment. Like Reagan and McGraw, Acevedo was an engineering grad who wanted to work in operations. Unlike the other two, he came upon this desire during his college years at the University of Puerto Rico, when he became a hardcore fan of the Canadian TV series How It’s Made.
“I know it’s funny, but getting to see how a product is developed from start to finish, then delivered to a customer?” Acevedo says. “That’s something I pretty much did fall in love with. I didn’t want a desk job where I’d design something I probably won’t even see until maybe many years later, and I liked the fast-paced environment of manufacturing.”
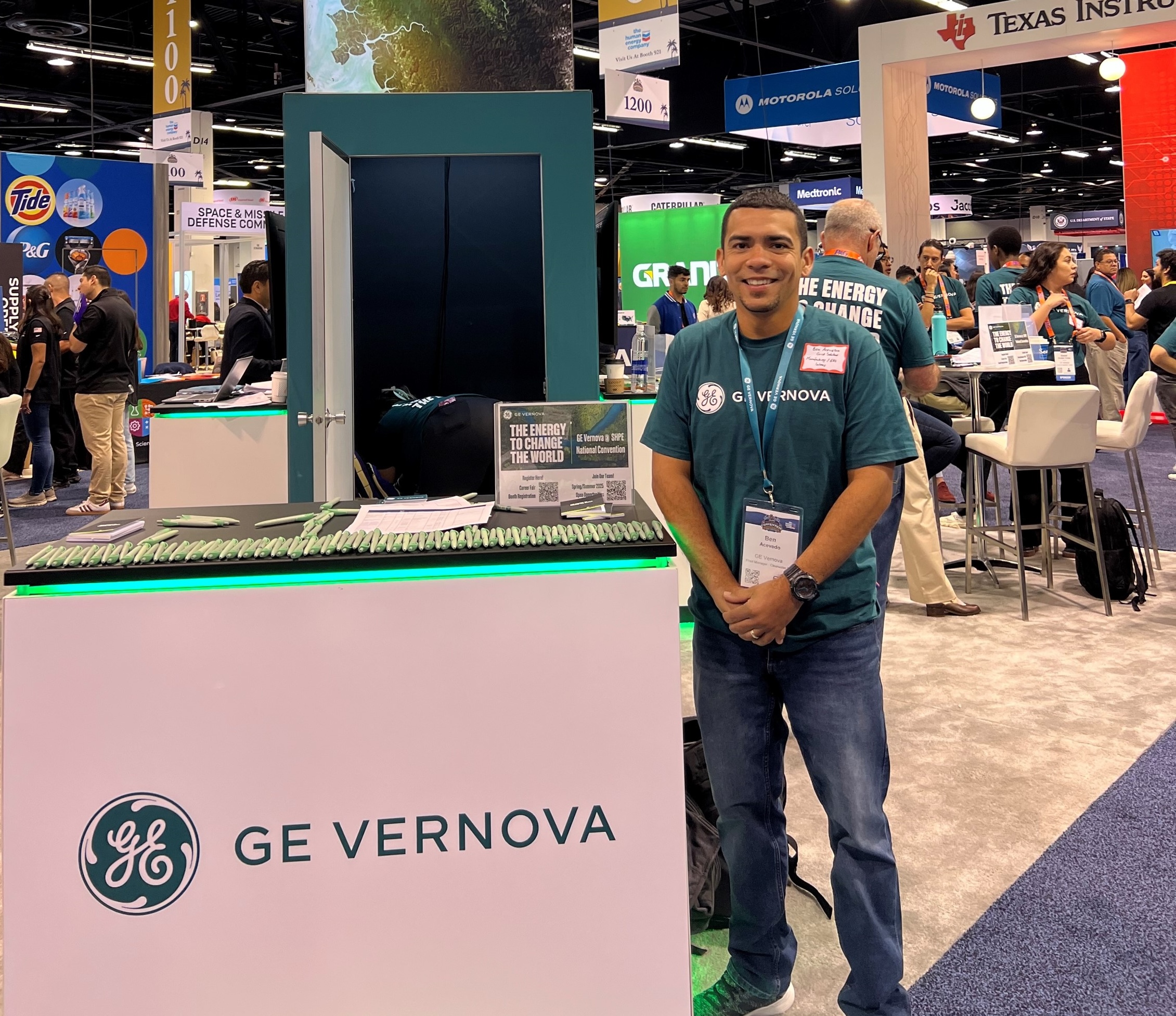
He saw just how fast-paced things could get when he oversaw the complex transfer of work processes for a New Hampshire-based product line to the Clearwater location. “New equipment, acquisition, hiring and training a lot of people, and doing it all without any disruption of the supply chain,” he says. “That really pushed my abilities to innovate and quickly create connections with people.”
Acevedo especially values the visible, palpable progress he gets to witness in operations. “Your decisions impact 700 people, so when, for example, people feel secure in their jobs, that’s very fulfilling.” He advises those just starting out to explore all opportunities available during college — internships, co-ops, student organizations — but stresses his satisfaction in the high-pressure role he’s come to love. “You’re applying engineering skills to real-life challenges, but since everything is target-driven, you really see your wins. And you see how much you do to uplift the whole team.”