The staff of Power Plant 8 in Riyadh, Saudi Arabia, is busy even on an average workday. But operations ramped up last December when a 25-person crew from GE Vernova assembled at the site for an important planned maintenance project.
Over the next eight days, working in 12-hour shifts around the clock, the team restored one of the four GE Vernova 7F gas turbines installed at the plant to peak condition. Maintenance works like this one, led by GE Vernova in collaboration with Saudi Electricity Company (SEC), owner of Power Plant 8 (PP8), help support years of reliable and efficient power for the residents of Riyadh.
The project also represented an important milestone: It was the first gas turbine outage planned and executed in the country entirely by Saudi engineers, specialists, and technicians, and it highlights GE Vernova’s and SEC’s commitment to fostering local talent.
“To execute a full outage with all Saudi nationals, from the service manager to the tool keeper, was a dream come true,” says Asma Aba Al-Khail, the resource manager for GE Vernova’s field services unit in Saudi Arabia, who was part of the first female-field-engineer-led outage. “Since my first day with the company, we have supported every effort to give back to our communities and empower local workers. I’m honored to be part of GE Vernova’s success.”
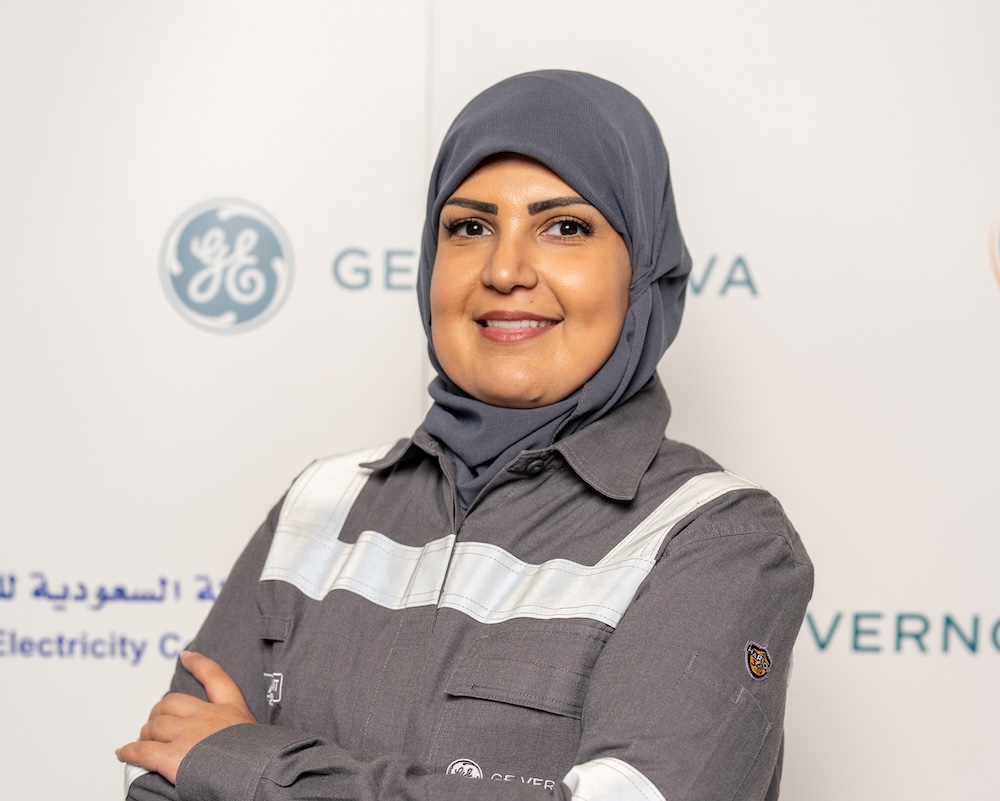
The prestigious achievement was celebrated on February 24 in the presence of senior energy industry stakeholders from across the public, private, and not-for-profit sectors at GE Vernova’s New Era of Energy event, held under the patronage of Saudi Arabia’s Ministry of Energy.
Making the Most of Downtime
Like any other machinery, gas turbines need regular maintenance. Every four or five years, units are taken offline for inspection, repairs, and potentially upgrades — an event called an outage. Because the grid is designed to be redundant, the utility can reroute power from other sources to cover the dip in capacity, so customers don’t usually notice a change in service during the weeks of an outage.
But behind the scenes, crews are working on a tight deadline to get the turbine back into operation. Each of the four 7F and ten 7E gas turbines at PP8 play a vital role in meeting the capital’s growing electricity demands. Because the scheduled outage presents a once-or-twice-a-decade opportunity for maintenance and repairs, technicians use the time to complete hundreds of mechanical tasks — often on complex parts that must fit together like puzzle pieces, separated by gaps narrower than a human hair.
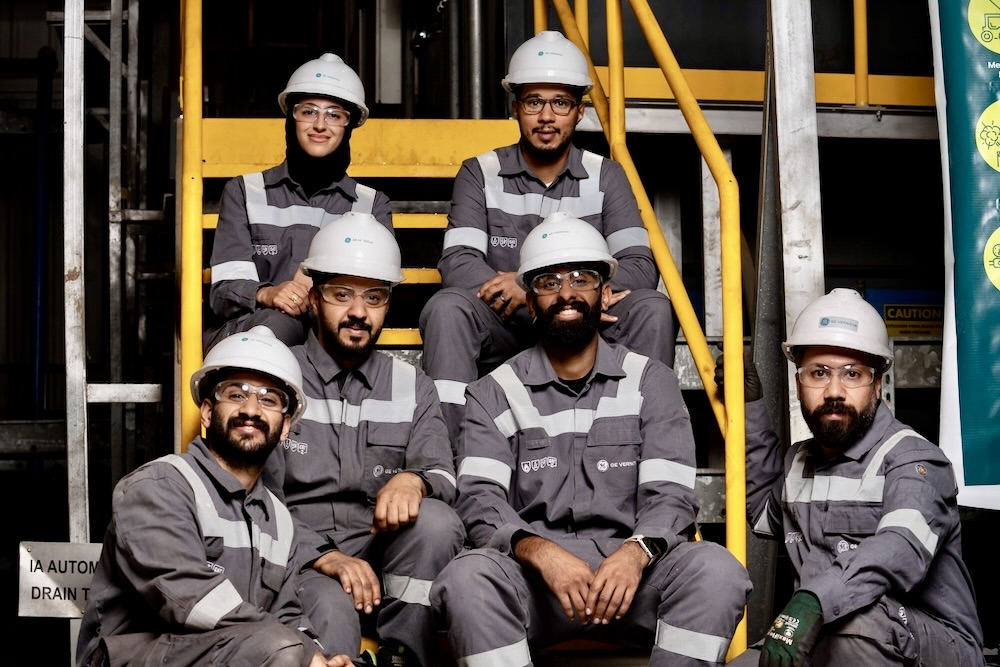
Highly technical and often physically demanding, the work requires intense focus and close coordination between engineers, technicians, safety personnel, and equipment specialists. To help ensure that the PP8 outage ran smoothly, during the past two years, GE Vernova was committed to hiring, training, and monitoring the team’s performance to improve any gaps.
And because outages can pose risks for field crews — caused by, say, hot surfaces, pressurized fuel, electric arcs, or rotating blades — the team’s environmental health and safety (EHS) specialists, Sarah Al Fardan and Jumana Al Abdulsalam, implemented GE Vernova’s strict safety procedures at the plant. Aba Al-Khail remembers that “we were on top of everything,” identifying and eliminating hazards to prevent any injury. As a result, the field service personnel completed their tasks without any incidents, injuries, or near misses.
“Safety was our number-one priority,” Al Fardan says. “I’m really proud that we succeeded, and we did it safely and ahead of schedule, also thanks to the adoption of lean methodologies.”
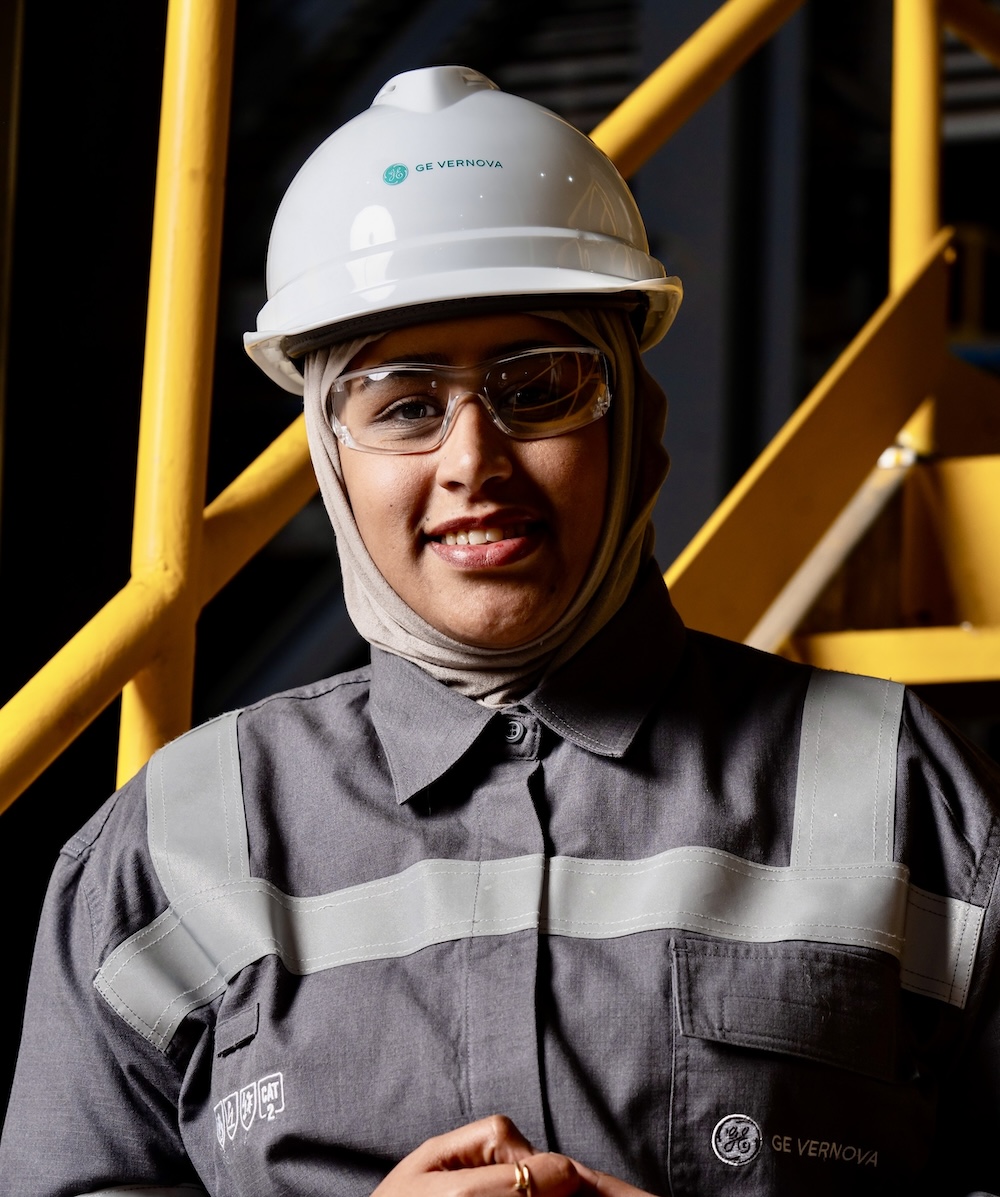
As they oversaw the team, Al Fardan and Al Abdulsalam were guided by the principles of lean, a management philosophy intended to eliminate waste. One of lean’s core methodologies is to define the safest and most efficient procedures for each task. Called “standard work” in lean terminology, these protocols were made available to the team on-site via Live Outage, a web-based digital mega-repository of information on every type of outage. Using large touch-screen monitors and weatherproof tablets, workers follow step-by-step instructions augmented by photos of the machinery and videos of every operation. Live Outage tracks their progress in real time, with status bars for each of the hundreds of tasks that need to be completed. Safety measures are built into the standard work, and Live Outage displays checklists that remind the team to put on personal protective equipment, for example, or to keep clear when cranes are extracting heavy components from the turbine. As a result, Live Outage helps teams complete their work more safely — and as much as 40% faster.
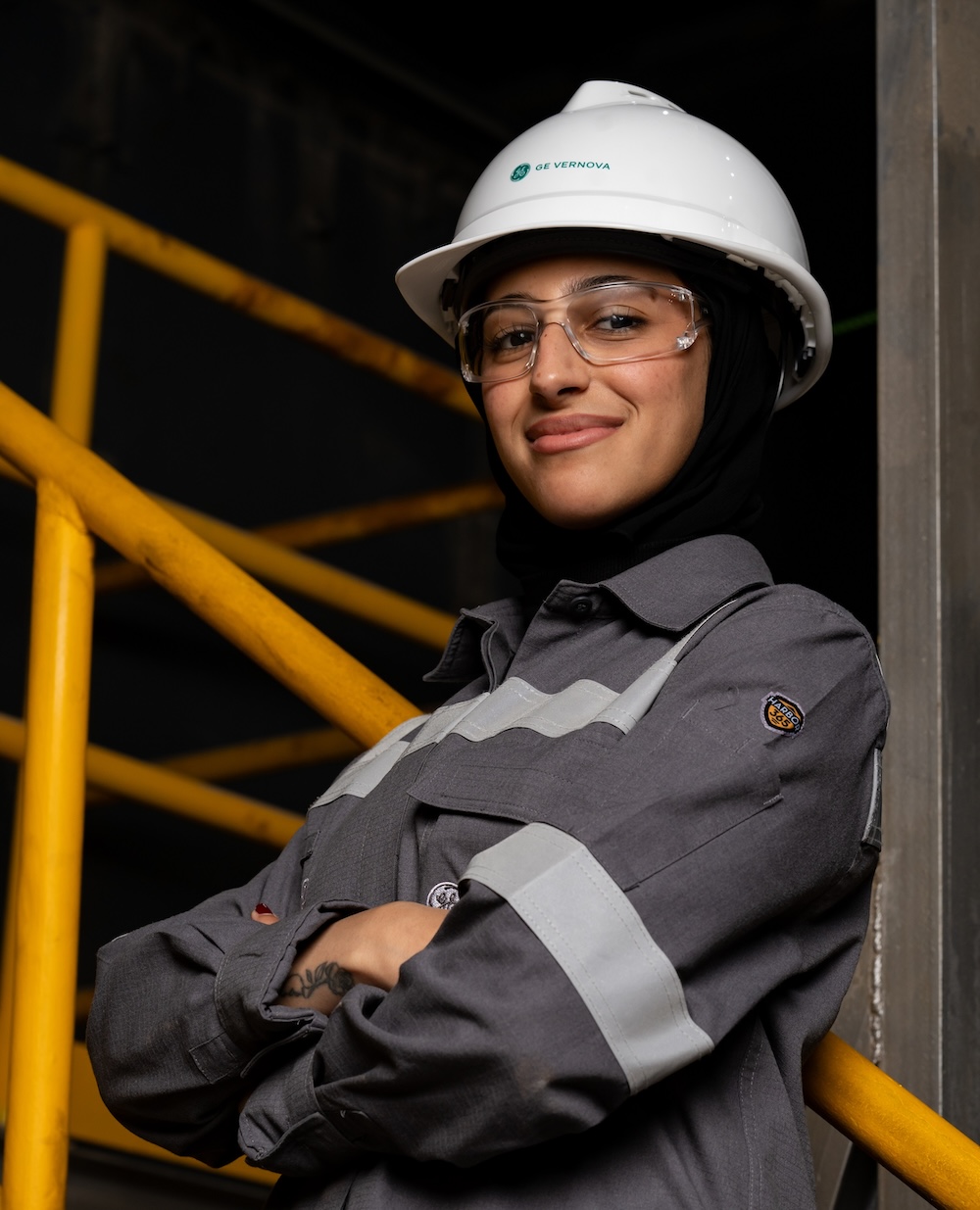
In keeping with that trend, the Saudi team finished days ahead of schedule, an achievement they also credit to cohesive teamwork. Because many members of the crew had worked together for more than a decade and all of them were Saudi nationals, they quickly fell into step on the plant floor.
Breaking Barriers
All told, their achievement was a decade in the making, the culmination of years of comprehensive training, certifications, accreditations, practical experience, and professional development for local talent — made possible by a growing interest in technical careers among the Saudi generation now entering the workforce. The inclusion of women on the team — something Aba Al-Khail says would have been “unimaginable” at the beginning of her career — signals another ongoing shift. In their years on the job, Aba Al-Khail, Al Fardan, and Al Abdulsalam have watched the culture evolve — and helped push it forward.
“It used to be very challenging to work on-site as a woman,” Al Fardan says. “But minds are changing. Now people understand that we can do the job.”
“To have women on the team was a moment of pride that I cannot even describe. Some people still say ‘females can’t do it,’” Aba Al-Khail adds. “I’d been the only woman in my department for a long time. We couldn’t have done this without the company believing in us, and now we’re ready for whatever comes next.”