“It takes a village to raise a child” is an African proverb that explains how it requires inputs from many different people with many different roles to do the important and challenging job of raising a child. It also takes a village of experts from around the world to design, manufacture, test, ship, and install the thousands of wind turbines that are coming together at what is expected to become the largest wind project in U.S. history — if not the entire Western Hemisphere. Team members from across GE Vernova’s global Wind organization have been working together, leaning into expertise found in all corners of the country, and helping make their mark on the megaproject that is SunZia. Join us on a tour of the sites and meet the people bringing this project to life.
Real-World Testing at Lubbock, Texas
Under the hot West Texas sun, Matt Dudon gears up for a turbine climb. Harness? Check. Headlamp? Check. Hardhat, safety goggles, and steel-toed boots? Check, check, and check.
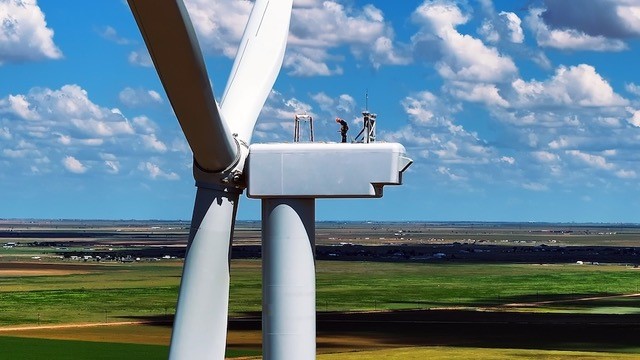
Matt is a systems engineer for GE Vernova’s workhorse onshore wind turbine, the 3.6MW-154m. This wind turbine gets its name from its ability to generate 3.6 megawatts (MW) of power and the 154-meter diameter of its rotor blades. In his role, Matt spends his days testing and validating the company’s technology, including visits to the turbine’s prototype (pictured above and at top), which spins in the skies over Lubbock, Texas.
The prototype serves as a real-world testing and training tool that gives teams early insight into how a turbine will be built and operate before it’s manufactured to scale and constructed out in the field. Today Matt will climb nearly 100 yards up and into the newest wind turbine to get a firsthand look at the next-generation technology he and his colleagues have spent years developing.
A Megaproject in Corona, New Mexico
Under the same sun 250 miles west, the first commercial 3.6MW-154m turbines have made their way to Pattern Energy’s SunZia Wind Project, where a team of more than 2,500 people are working to construct a massive renewable energy infrastructure site that includes 674 of these GE Vernova turbines (pictured below under construction). They’ll contribute more than 2.4 gigawatts (GW) of energy to the site’s total 3.5 GW of total power output.
Dubbed a “megaproject” because of its sheer size and scope, SunZia sets the record for the largest onshore wind turbine order GE Vernova has ever received. Once complete, the project will generate enough energy to produce the equivalent amount of electricity needed to support the needs of approximately 3 million Americans living in the southwestern U.S.
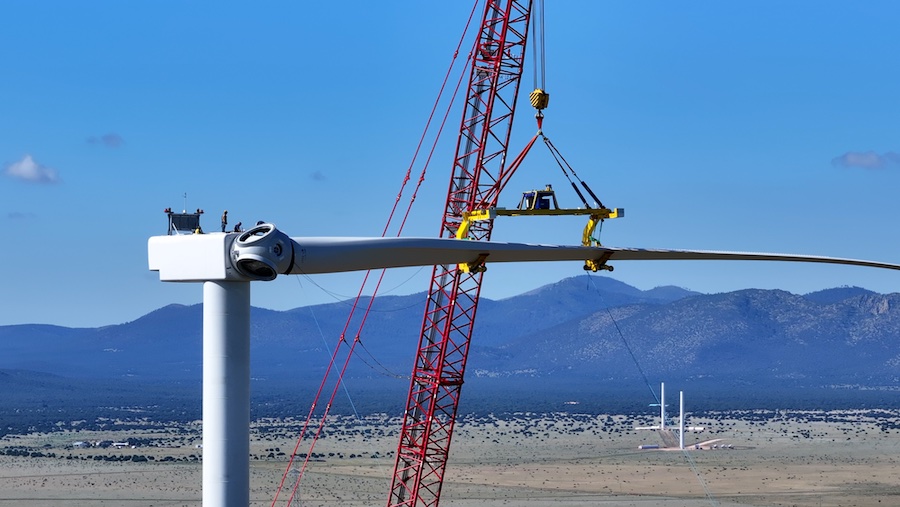
The 3.6MW-154m is what the company is calling its “next-generation workhorse,” considering that it builds on the back of its bestselling 2.8MW-127m technology. The 2-MW technology has made its mark as the most installed wind turbine in North America, even finding itself at SunZia’s neighbor to the north, Western Spirit Wind (pictured below), GE Vernova and Pattern Energy’s first venture into a gigawatt-scale project, with 377 of the machines. Drawing on more than 200 million operating hours from its predecessor, the new 3.6-MW turbine uses its proven designs to improve durability and efficiency.
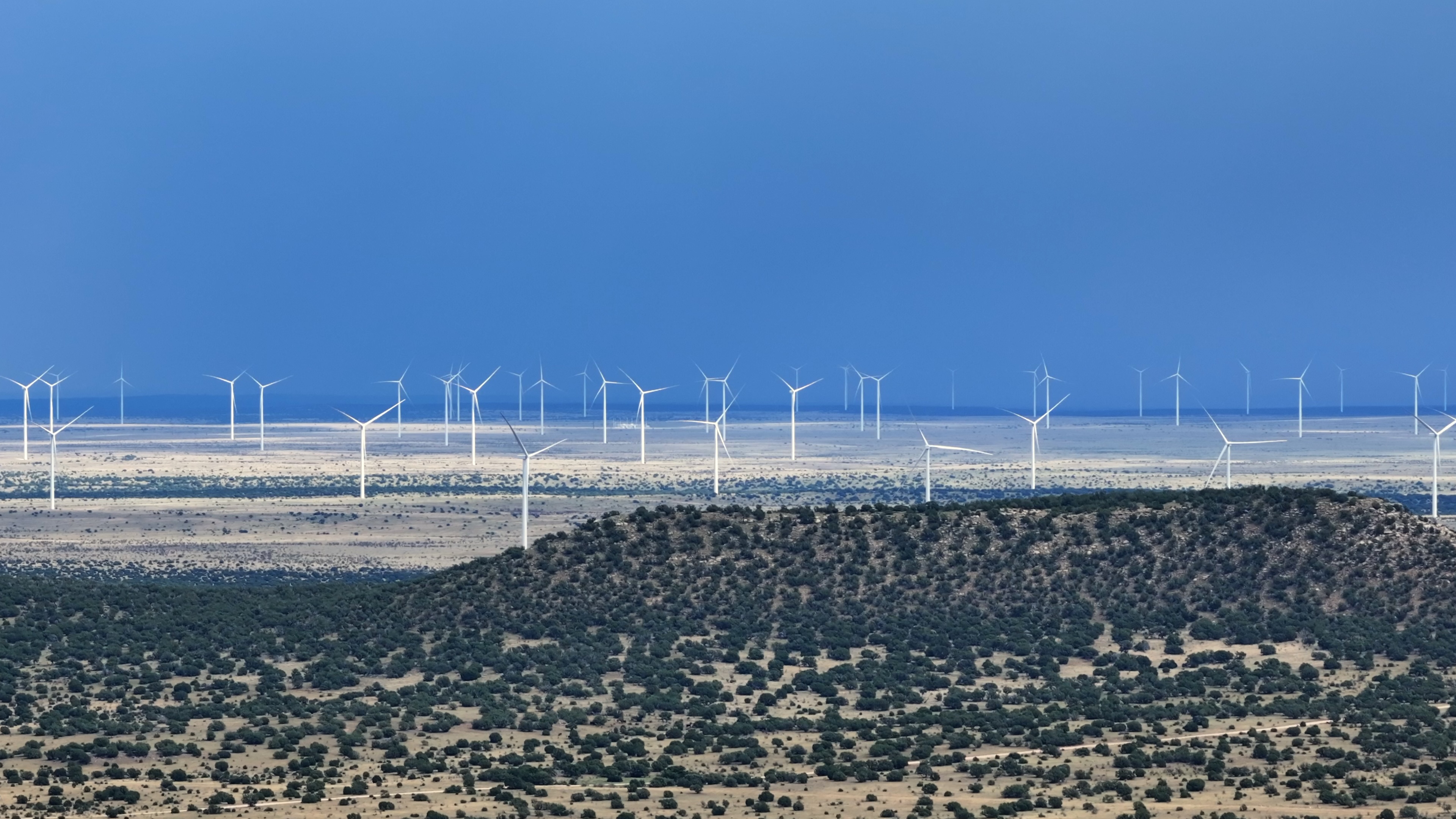
Manufacturing Blades at Grand Forks, North Dakota
Thirteen hundred miles north, GE Vernova’s Grand Forks blade factory is producing wind turbine blades that it will ship to the site. The power-generating arm of the wind turbine goes through a complex manufacturing process. This is why team members from all across the Wind business collaborated with their peers at GE Vernova’s Advanced Research Center to create and introduce the Digital Blade Certificate, a new process rooted in the company’s commitment to ensuring that blades leave the factory with consistent high quality.
The Digital Blade Certificate uses technology including artificial intelligence and machine learning to enhance the work of experienced human inspectors, focusing on areas within the blade that people can’t access. Small machines, or “crawlers” (pictured above), traverse the interior and exterior of blades to take high-resolution imagery that’s then inspected and used to identify minuscule deviations, so teams can make corrections before the blades come off the line.
A Turbine’s Journey Starts in Pensacola, Florida
The beating heart of the turbine, the machine head, starts its life in Florida. GE Vernova’s Pensacola factory manufactures and assembles components for the 2-MW, 3-MW, and repower onshore wind product lines. The first batch of new machine heads came off the line here in July, and a steady flow has been making the 1,200-mile journey to the SunZia project site ever since.
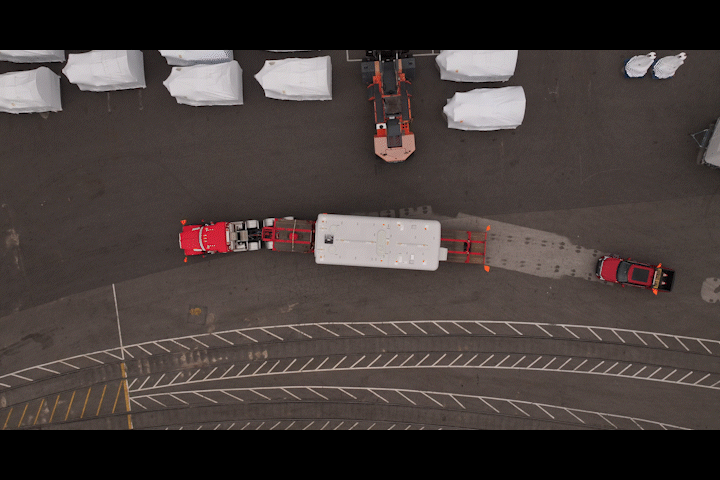
Logistics Safety and Quality Engineer Jamie France (pictured below) knows well what it takes to get components from Pensacola to remote sites like this. Her standard day includes working with a variety of transport companies to haul massive turbine components like the nacelle pictured above from the factory to wind farms that are often in remote locations. She also played a critical role in the design process. Having logistics in the mix early on helped minimize design-related challenges that could come with the shipping constraints of the U.S., the turbine’s primary home base.
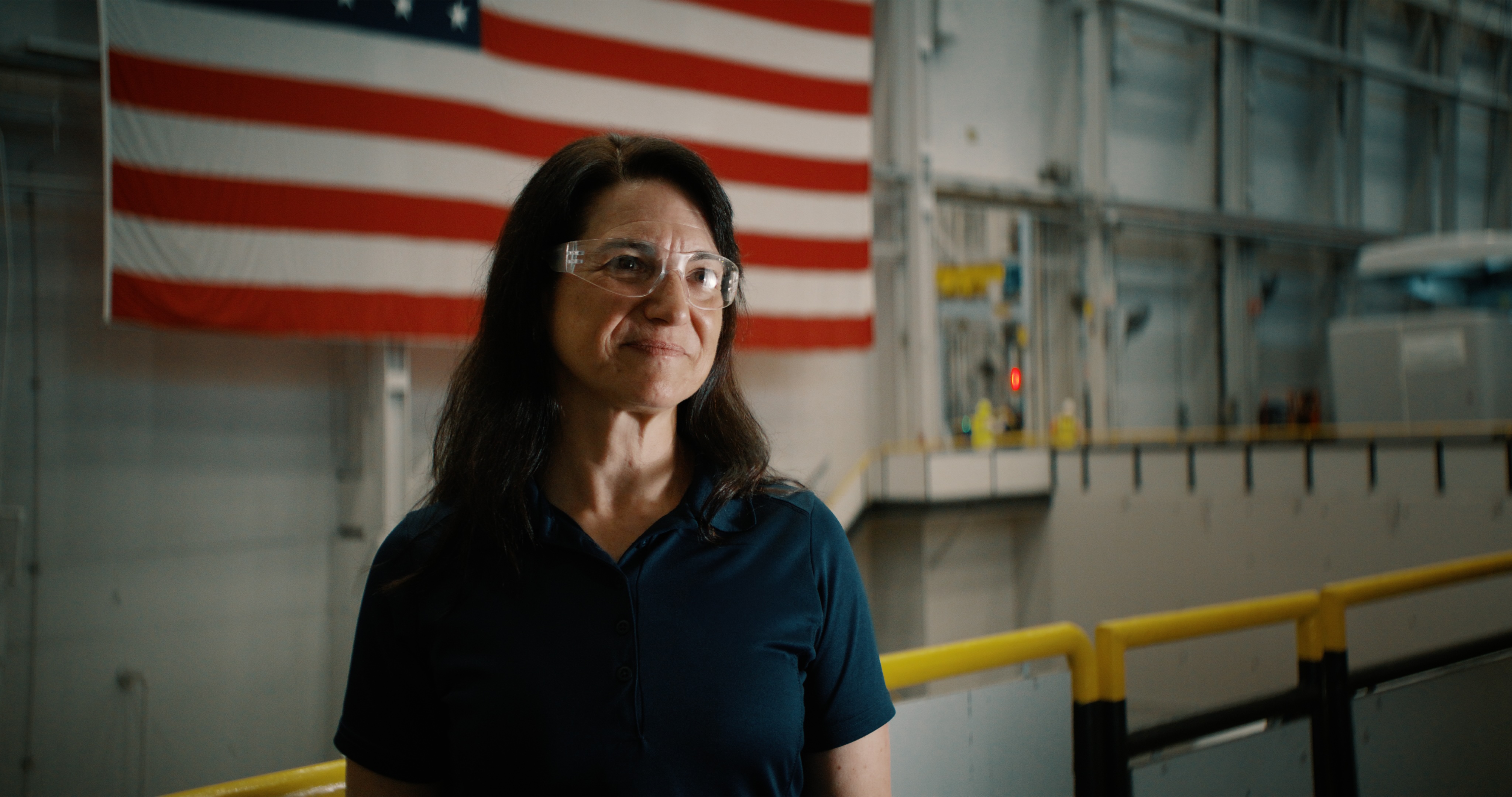
As the energy transition accelerates and the demand for renewable energy increases, megaprojects like SunZia are looking like a new norm. GE Vernova’s answer to this is in its scalable, reliable workhorse products. And as they evolve and generate more megawatts, it becomes even more important to address the full technology life cycle, mitigating risks and challenges across the work taking place in factories, on the roads, and in the field, and working to guarantee reliability and availability for their customers and energy off-takers for decades.
When it comes to Jamie’s role and the responsibilities that come with it, the focus is clear: “The number one goal of my work is to protect people, and then protect the quality of the item we’re delivering for our customers,” she says.
Winds of Change
Back in Lubbock, Matt Dudon comes back down-tower with a smile on his face, ready to take his learnings back to the team. In a rapidly growing industry like wind, he knows there’s always more to do, more to learn, and more to continuously improve upon. To him, that’s OK — it’s a dream job, even.
Matt fell in love with designing wind turbines in college, and he’s heard SunZia described as the “Hoover Dam of renewable energy.” He considers it a pivotal point not just for renewable energy in the United States but for the whole wind industry moving forward.
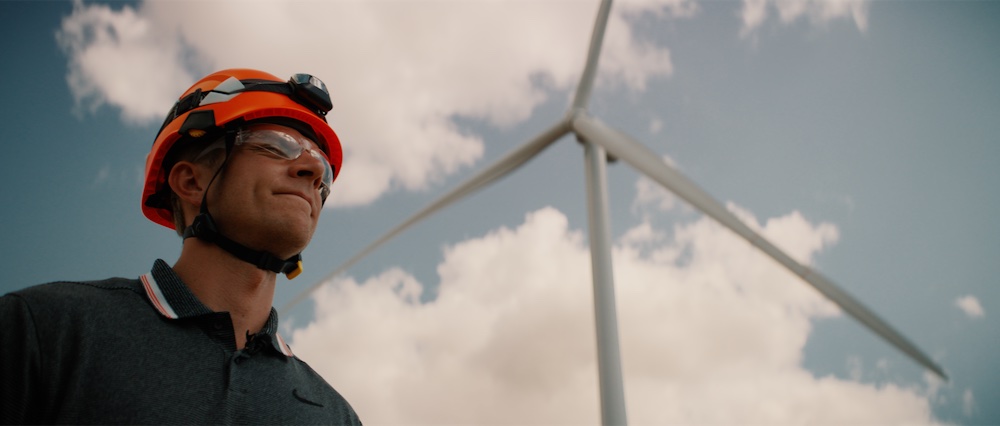
“I have a one-year-old daughter, and I spend a lot of time thinking about what I’m going to tell her as she grows up and starts to understand what my job is,” he says. “I think about how cool it’s going to be someday to say, ‘See those wind turbines? I helped design those, and they’re putting renewable electrons on the grid.’ I want her to grow up in a world with clean air and energy security. I want her to enjoy everything that I got to enjoy.”
Learn more about SunZia, the 3.6MW-154m workhorse turbine, and the Pensacola manufacturing plant in GE Vernova’s upcoming video Winds of Change. Get a behind-the-scenes look at what you can expect with the preview below.
This article contains forward-looking statements, which provide current expectations based on certain assumptions. Except as required by law, we disclaim any obligation to update these statements.
Images: GE Vernova