Navigating outage delivery during peak periods
Power plant outage management during peak periods presents a unique set of challenges that demands carefully planning outage delivery strategies, clear communication, and collaboration between service providers and customers. Each element is essential in meeting project deadlines and ensuring safety, quality, and customer satisfaction. This blog explores common obstacles in planned maintenance outages, effective outage management strategies to overcome them, and the critical role of customer collaboration in outage planning.
Challenges in outage delivery
Peak period pressure: During peak seasons, such as spring and fall, the demand for outage services surges, resulting in resource constraints and scheduling conflicts. Managing these periods requires advanced planning, strategic resource allocation, and contingency planning to mitigate challenges.
Alignment gaps: Miscommunication and misalignment on outage dates, start times, and scope can lead to delays and inefficiencies and impact our ability to meet established deadlines. Establishing clear communication early in planning is crucial to avoid misunderstandings and delays.
Quality of tooling: Issues with tools and equipment, such as damaged or obsolete equipment, can cause significant delays. Inspecting equipment and tools before execution can help ensure they meet safety and operational standards, keeping operations running smoothly during the outage.
Scope and extra work alignment: Outages rarely go exactly as planned, resulting in additional work that can disrupt schedules and budgets. It is essential to align with the customer on the project's scope and establish clear processes and protocols for proactively addressing unscheduled work.
Outage management strategies for optimal outage delivery
Early date confirmation: Securing outage dates well in advance with Customer Portfolio Managers (CPM) allows for better resource planning. This helps ensure all parties are aligned on the start date, scope, and availability of necessary resources, including field engineers, craft labor, tooling, and parts.
Alignment on incremental scope: Regular meetings between customers and service managers are essential to review and coordinate additional scope occurring on-site, including third-party work and any emergent tasks during the outage. Tracking significant milestones and setting clear processes for authorizing extra work will help reduce strain on the project's timeline.
Root cause analysis (RCA) teams: Implementing RCA teams for significant issues and conducting Kaizen events to drive continuous improvement. These initiatives help identify gaps in the process, resulting in implementing corrective action plans to prevent delays or issues in the future.
Enhancing talent and training: Investing in talent development and training enhances expertise and readiness for complex outage scenarios. This focus on skill development is pivotal in maintaining high standards of execution.
Comprehensive tooling and equipment inspections: Regular audits and tool maintenance are crucial proactive measures, recommended to uphold consistent safety and quality standards, and prevent delays caused by unusable equipment.
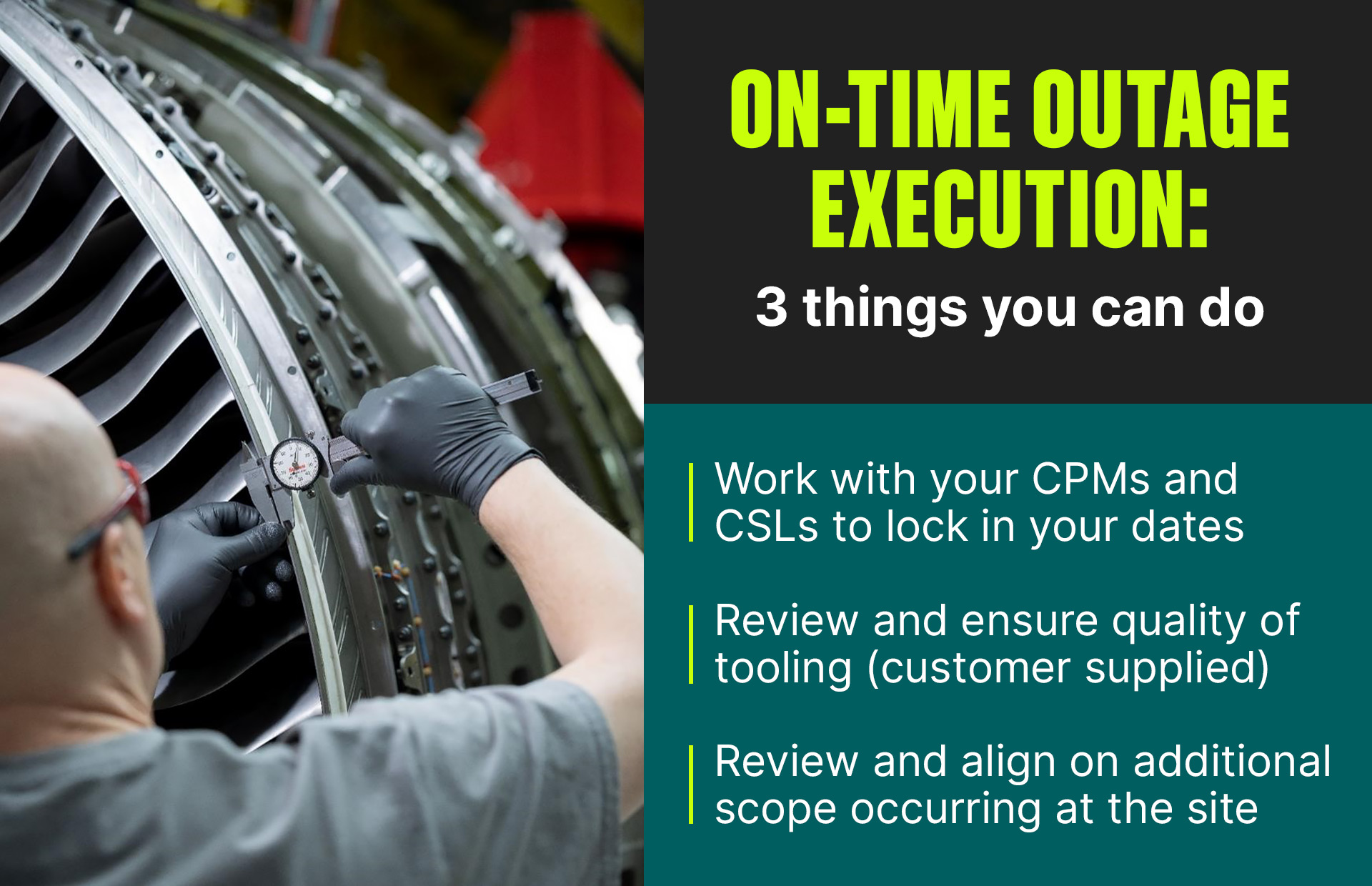